En marge du CP+ 2023, nous avons eu l’occasion de visiter l’usine de Fujifilm de Taiwa, dans la préfecture de Miyagi. C’est ici que sont assemblés de nombreux appareils photo et objectifs premium de Fujifilm, dont le GFX100S ainsi que le dernier téléobjectif XF 150-600 mm f/5.6-8 R LM OIS WR. Le rôle de l’usine de Taiwa est également stratégique dans la conception des nouveaux produits du constructeur. Allez, mettez vos charlottes, on vous emmène avec nous pour cette visite d’usine.
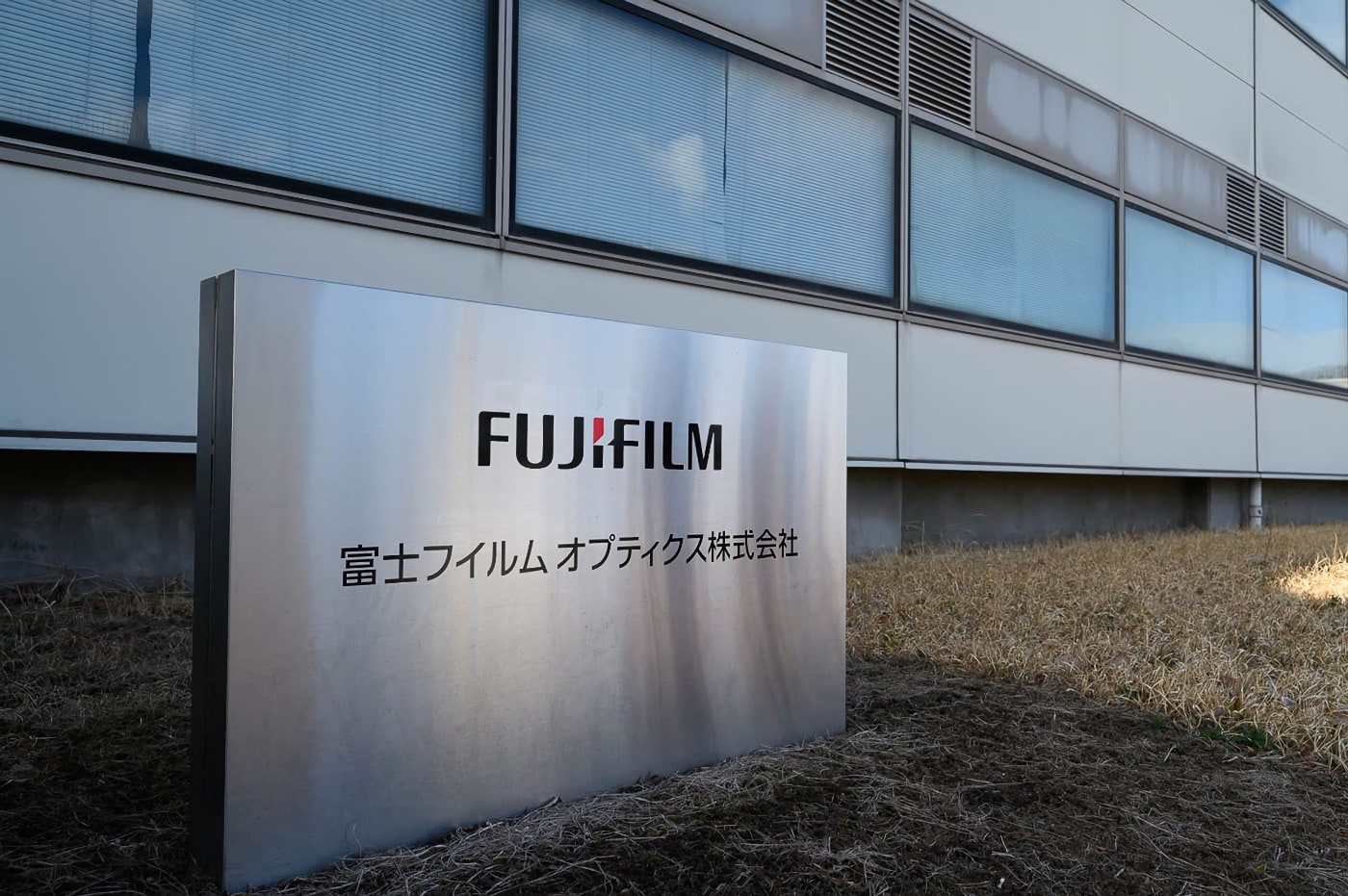
Sommaire
Usine Fujifilm Taiwa, un peu d’histoire
L’usine Fujifilm de Taiwa est située proche de Sendai, dans la préfecture de Miyagi. Elle se situe à plus de 380 km de Tokyo, soit environ à 2h15 de Tokyo en Shinkansen puis taxi. Comme nous allons le découvrir, l’usine de Taiwa (officiellement Fujifilm Optics Co, Ltd) est un élément stratégique pour le constructeur japonais.
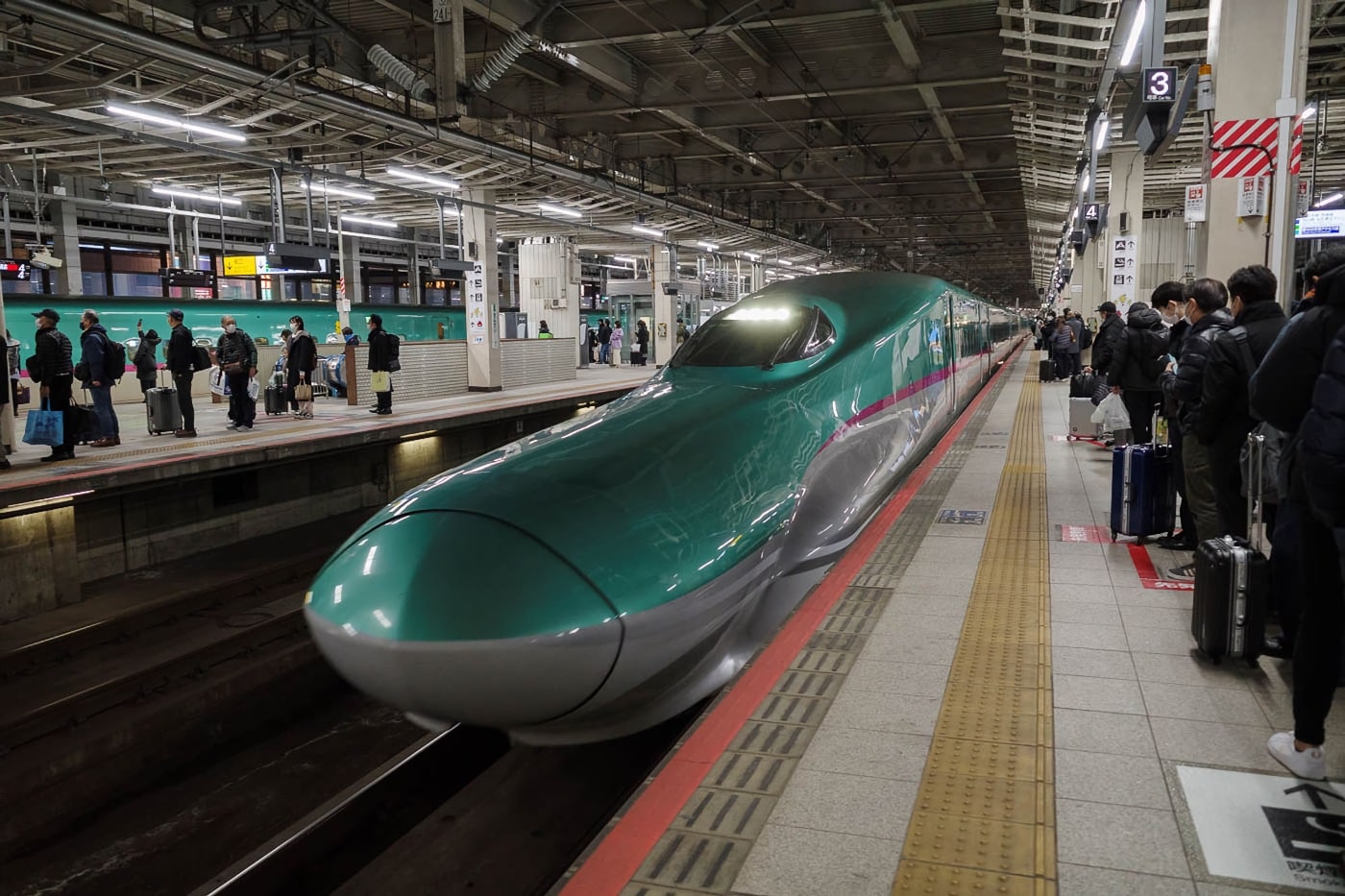
Cette usine a été inaugurée en 1968 afin de concevoir et produire les objectifs Fujinon. Depuis, de nombreux objectifs ont été fabriqués à Taiwa. En 2010, Fujifilm Optics Co, Ltd a été créé suite à la fusion de deux filiales Fujifilm dédiées à la production d’objectifs. En plus des boîtiers et objectifs, la société fabrique différents composants comme des lentilles en verre et en plastique, des produits optiques à couche mince et des moules d’injection. Petite anecdote : l’objectif le plus ancien encore fabriqué dans cette usine est le XF 35 mm f/1,4 R, sorti en 2012.
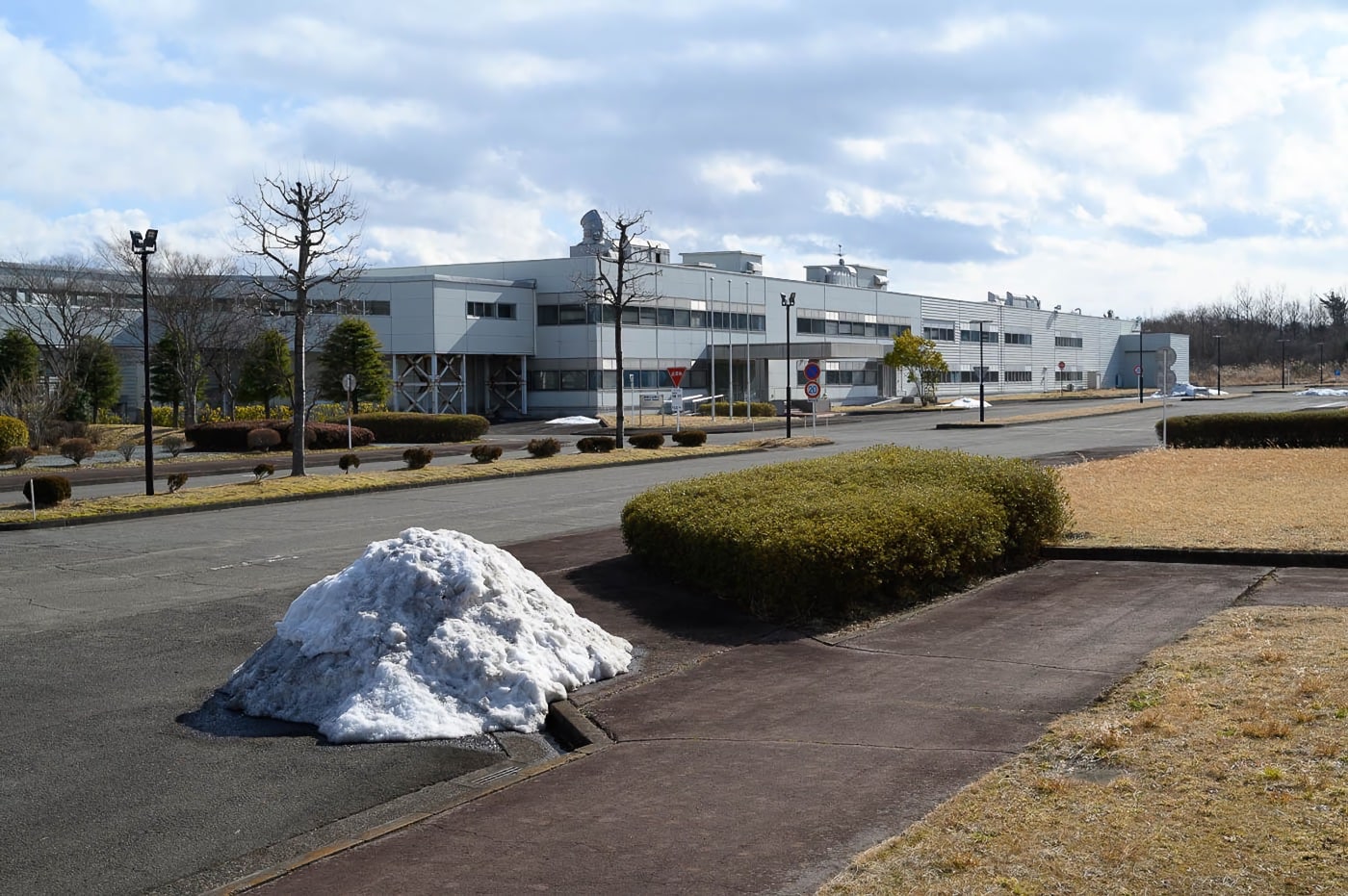
Mais l’histoire n’a pas été un long fleuve tranquille. Le 11 mars 2011 à 14h46 heure locale, un séisme de magnitude 9 ébranle le Japon. S’ensuit un violent tsunami dont les répercussions sont aujourd’hui bien documentées, notamment à Fukushima et sa région.
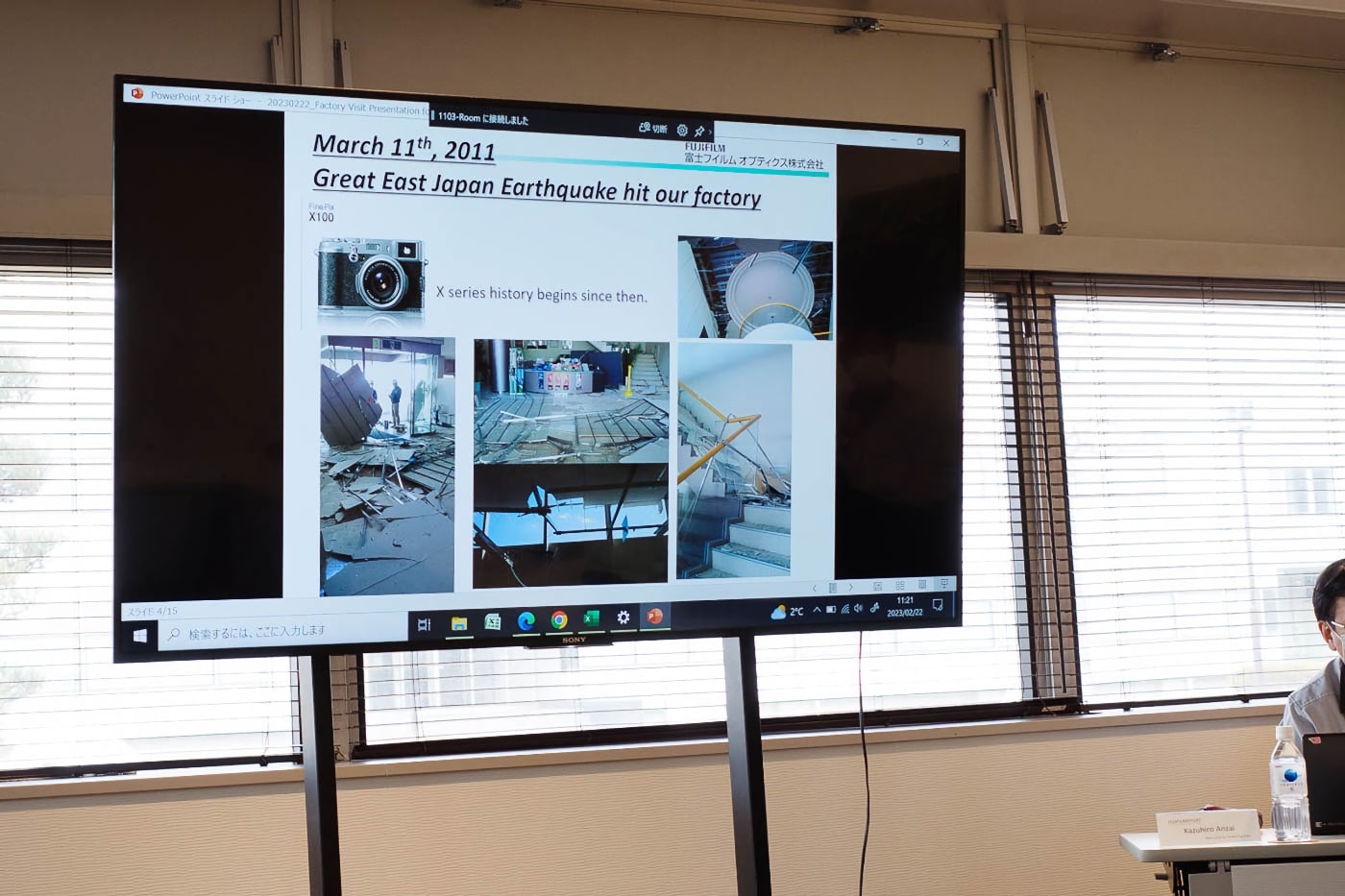
À Taiwa, alors que l’usine Fujifilm débutait la production de la série X avec le premier compact Fujifilm X100, les plafonds et climatisations se sont écroulés et les fenêtres ont explosé. Sur place, impossible de maintenir la production. Les équipes passeront 10 jours à nettoyer l’usine, ainsi qu’à déplacer les machines dans le second bâtiment, le premier n’étant plus opérationnel.
Ainsi, le 23 mars, soit 11 jours seulement après le tremblement de terre, la production redémarre, poussée par la passion des employés pour qui le développement du premier boîtier de la série X était très important. 12 ans après le tremblement de terre, l’usine s’est étendue et fabrique de nombreux produits, optiques comme boîtiers.
Taiwa : une pièce maîtresse pour Fujifilm
Actuellement, Fujifilm dispose de 4 usines au Japon. C’est à l’usine de Mito que le moulage des verres est effectué. L’usine de Morigane s’occupe du polissage des lentilles quand l’usine de Sano s’attelle à la fabrication des fûts pour les lentilles. Ces trois usines envoient ensuite leur fabrication à l’usine de Taiwa en charge de l’assemblage final de certains objectifs complexes ainsi que de l’inspection et des derniers ajustements. C’est également à Taiwa que certains boîtiers, dont le GFX100S et le X100V sont fabriqués.
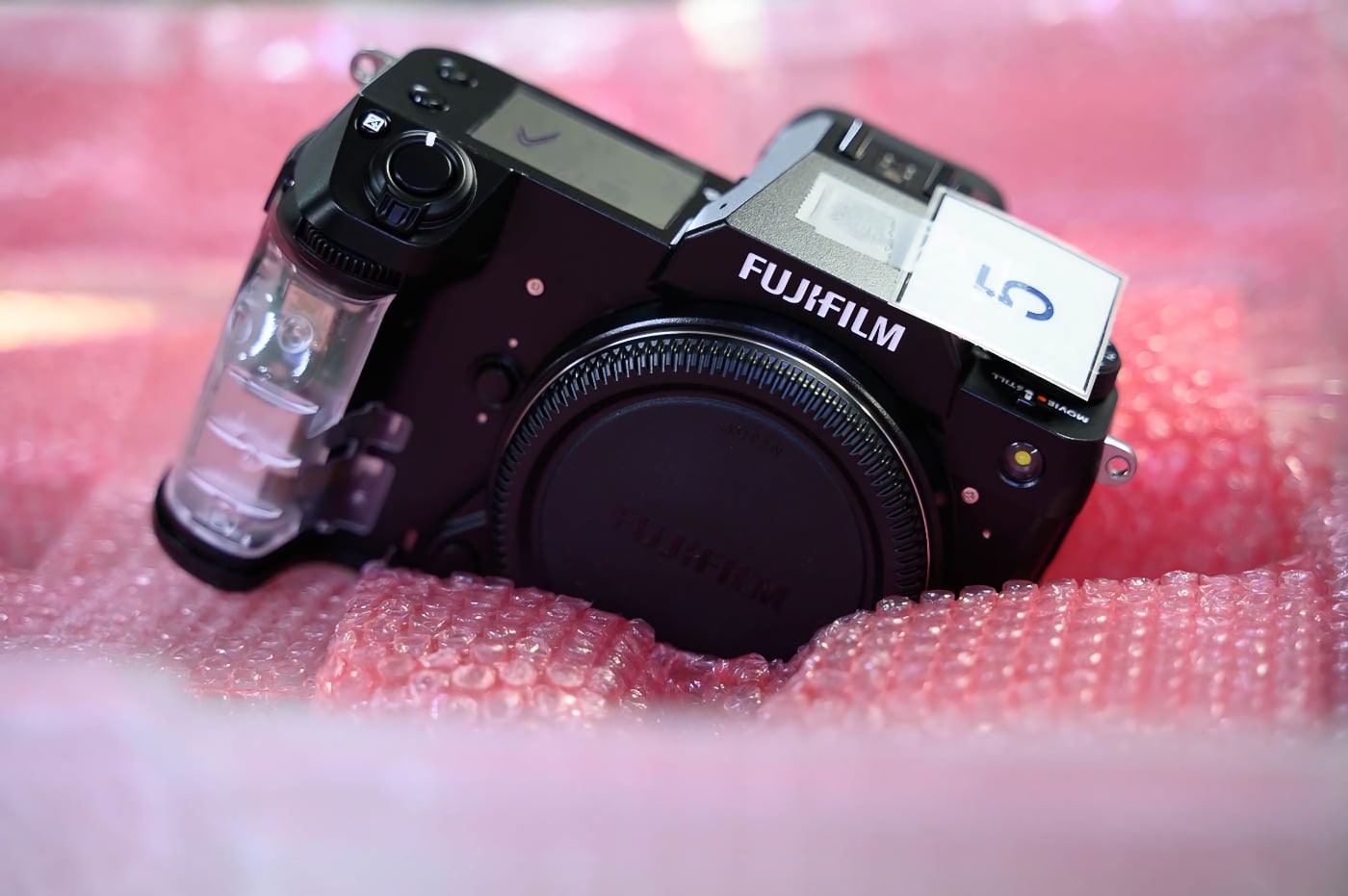
En plus de ces usines au Japon, Fujifilm dispose d’une usine aux Philippines pour le polissage de certaines lentilles et l’assemblage de certains objectifs. Une usine à Suzhou en Chine est également dédié à l’assemblage de certains éléments pour l’usine de Taiwa, ainsi que l’assemblage final de boîtiers photo comme le X-T5.
Grâce à ces différentes usines, Fujifilm fait partie des rares constructeurs photo disposant de ses propres usines avec un processus de fabrication complet, en parlant du moulage des lentilles à l’assemblage et l’inspection finale des produits.
L’usine de Taiwa a différents rôles, notamment liés au contrôle qualité. Ainsi, si Fujifilm a décidé de produire certains boîtiers et objectifs en Chine, la production de prototypes et de modèles en pré-production est toujours effectuée à Taiwa, afin d’en assurer la qualité.
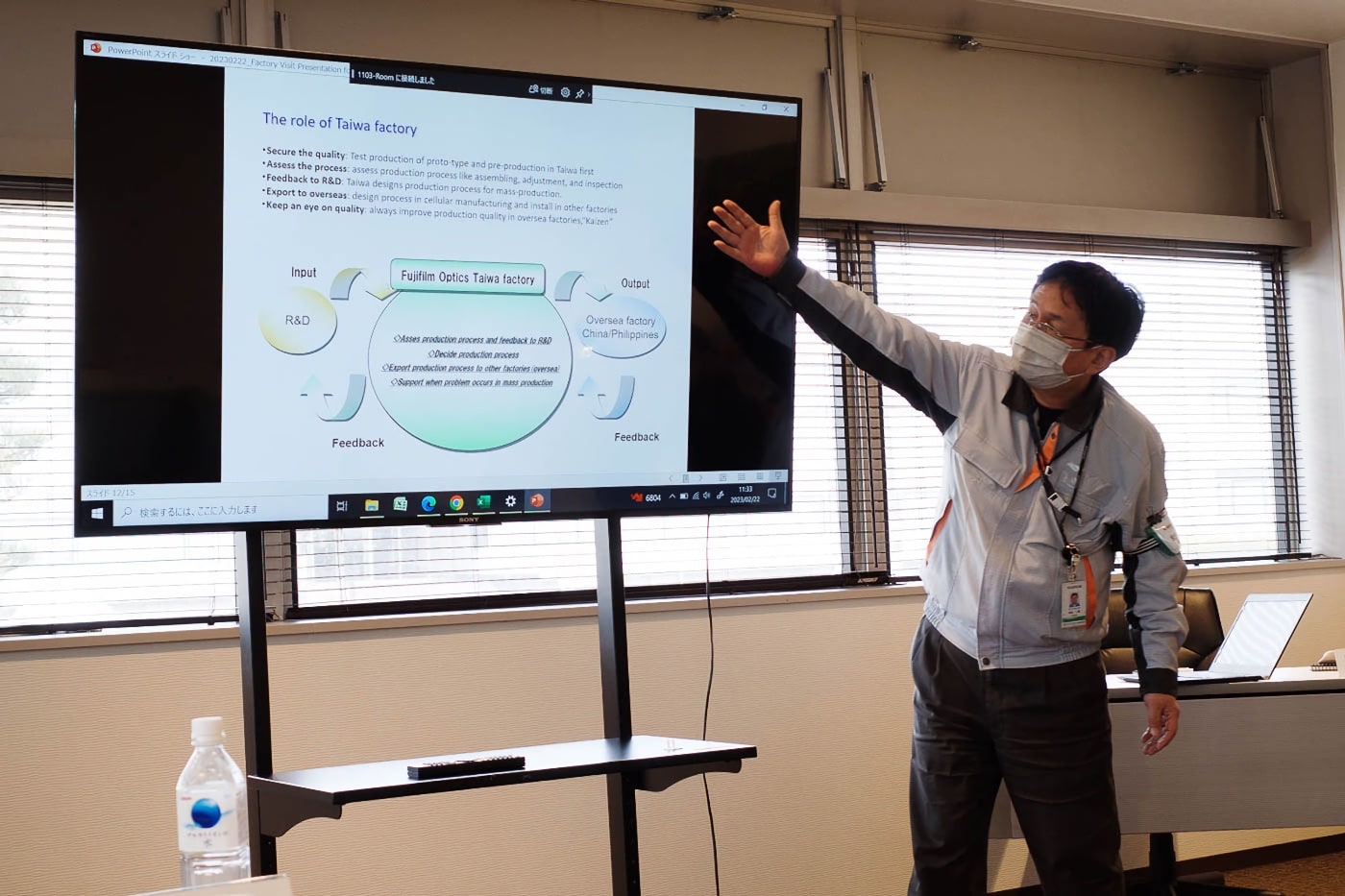
Ensuite, l’usine met en place l’ensemble des procédés de production (assemblage, ajustement et inspection) afin de pouvoir être prêt pour la production de masse, tout en faisant ses retours à la R&D afin d’améliorer les processus.
Ainsi, l’usine de Taiwa est capable d’exporter le processus de fabrication vers d’autres usines, tout en apportant son support et en gardant un œil sur le contrôle qualité grâce à la méthode Kaizen d’amélioration continue. Ainsi, les managers de l’usine sont fiers d’expliquer que si certains produits sont Made in China, la qualité est Made in Japan.
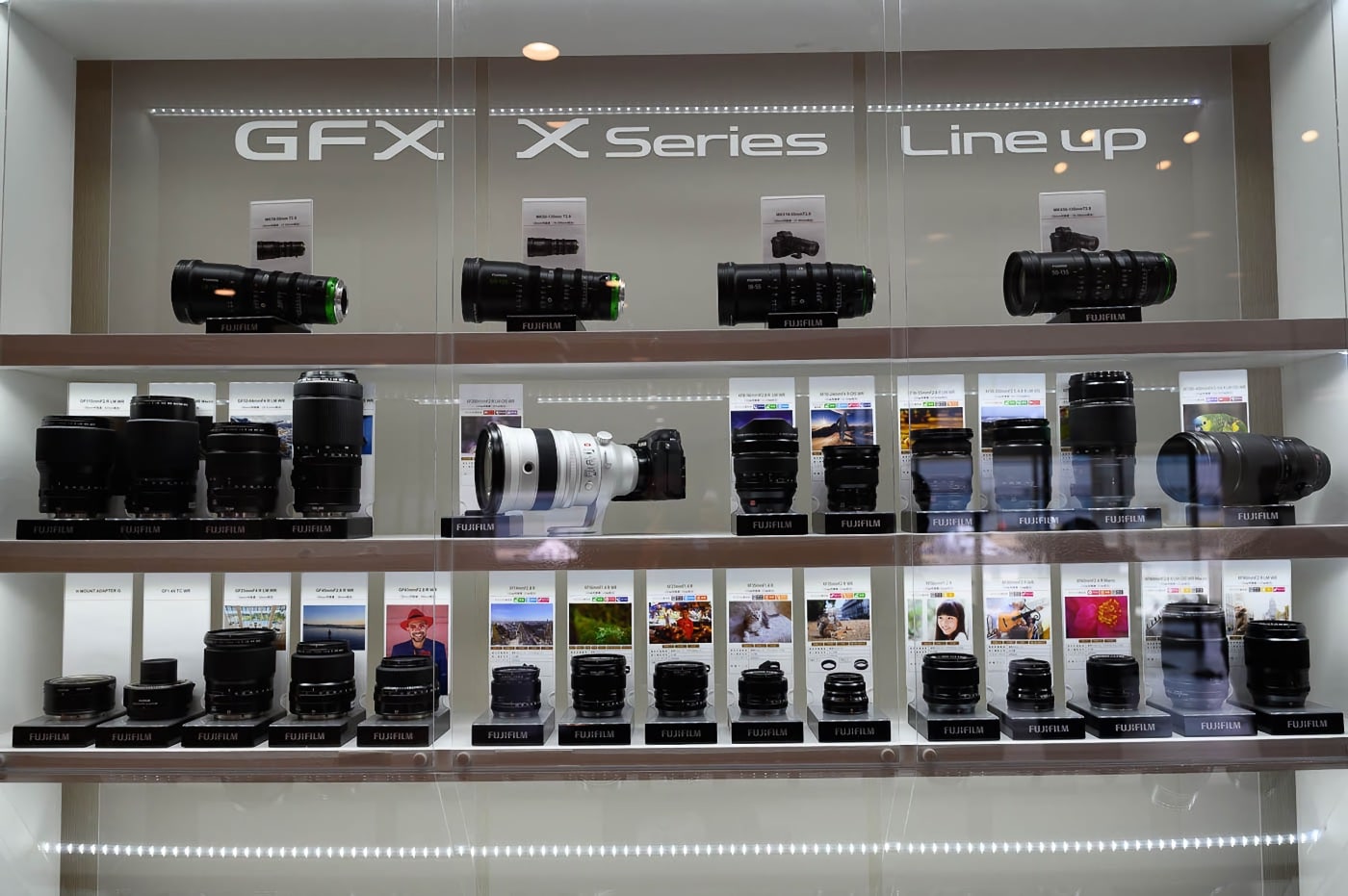
Sur place, l’usine est composée de plusieurs bâtiments. Le bâtiment principal est dédié à la production et au développement de techniques pour les appareils photo numériques, objectifs et traitement de l’image. Un second bâtiment est quant à lui lié au développement des technologies liées à la qualité d’image.
Maintenant que le décor est posé, place à la visite.
Petite dédicace sur nos chaussons, que nous ne quitterons plus jusqu’à notre départ.
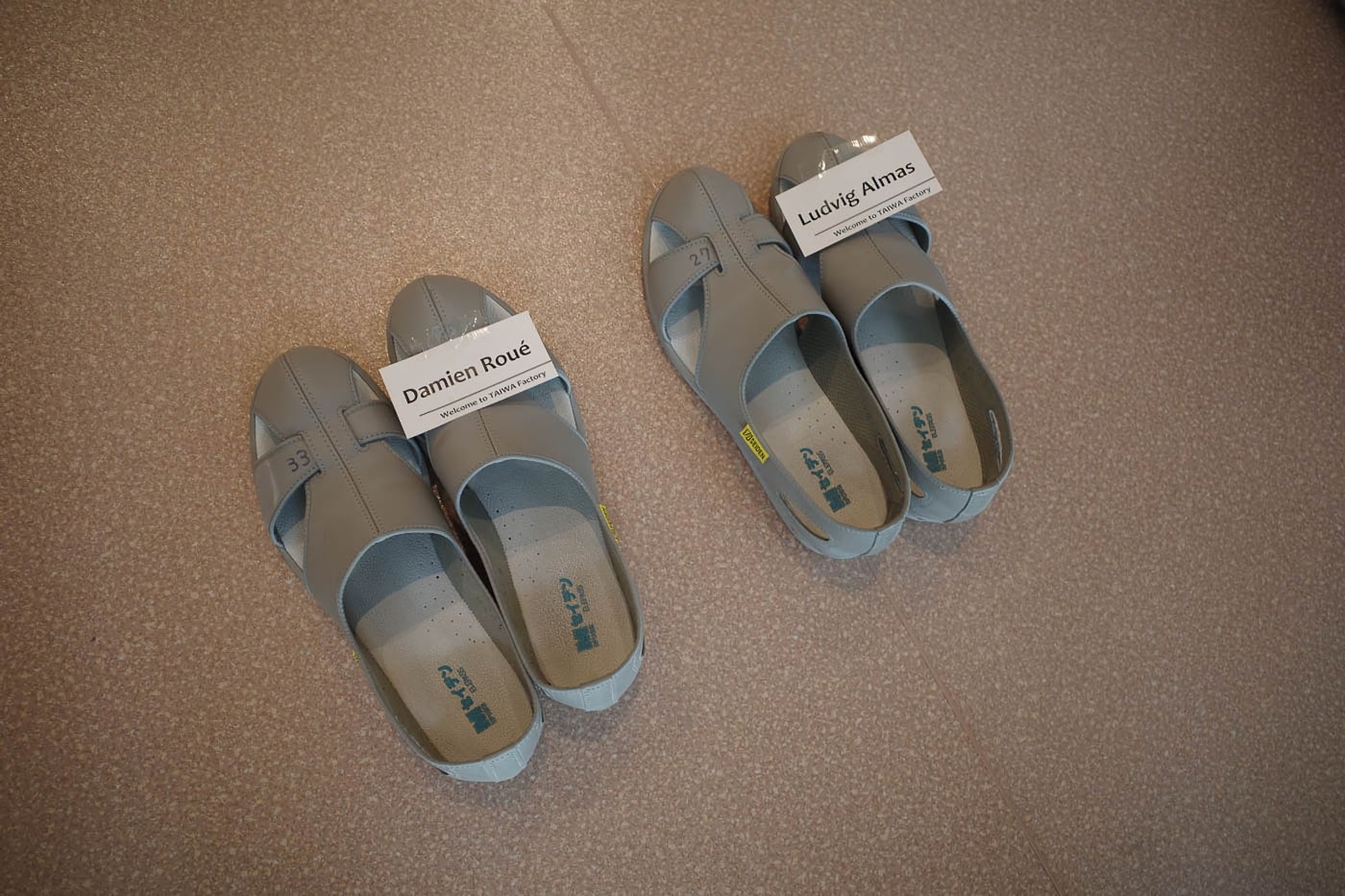
GFX100s : l’assemblage de A à Z
La première étape de notre visite se passe dans le bâtiment où les différentes parties des appareils grand format GFX sont assemblés. En effet, lors de notre visite, nous avons pu suivre la ligne de production du GFX100s.
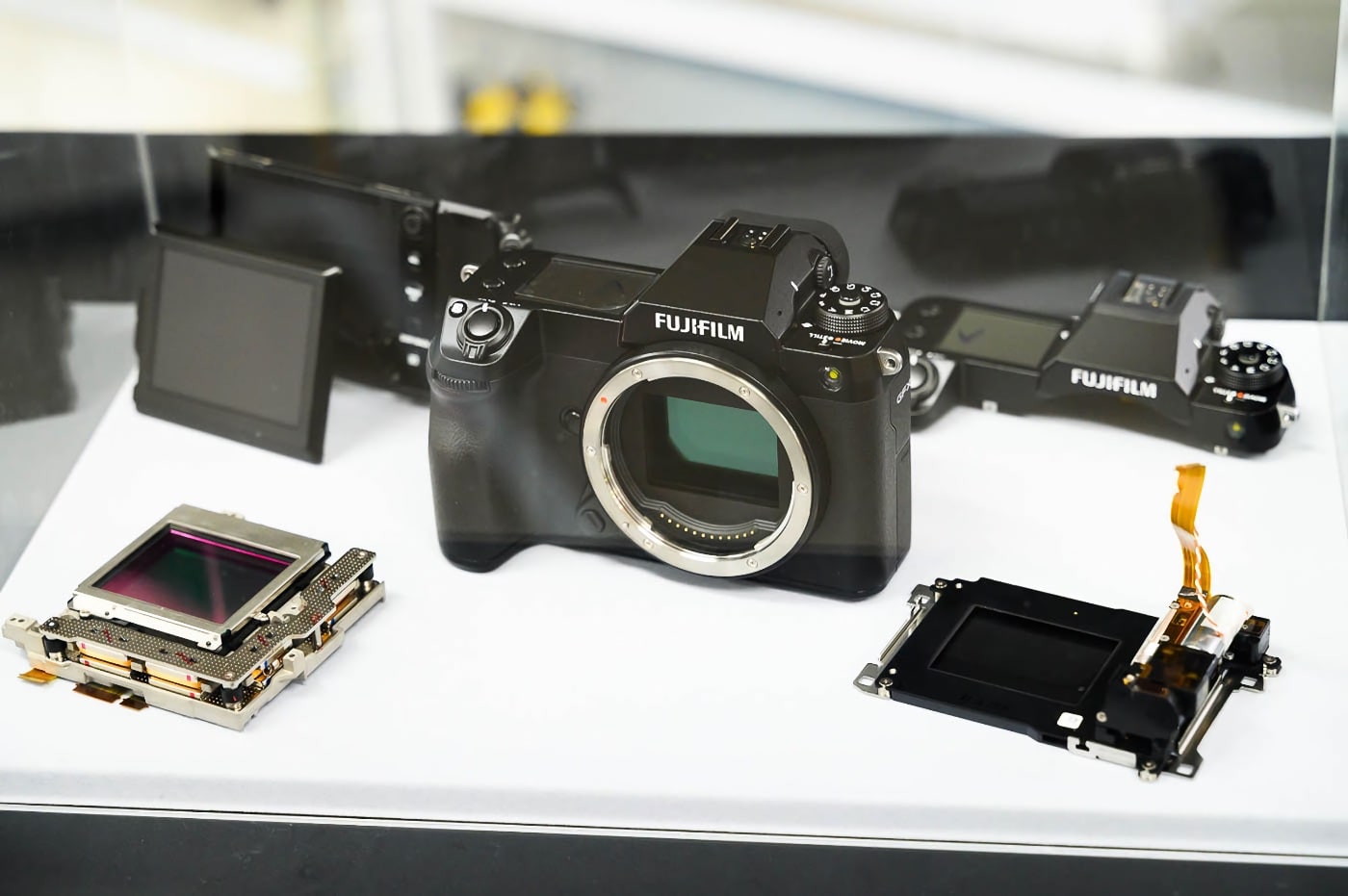
L’un des éléments les plus important sur ce boîtier est la cage de stabilisation du capteur moyen format de 100 Mpx. Si le capteur est assemblé dans une salle blanche, de nombreuses étapes de vérification sont effectuées sur le mécanisme de stabilisation, afin de s’assurer de l’alignement du capteur et du système IBIS.


Ces vérifications sont souvent automatisées, grâce à des machines et robots conçus en interne par Fujifilm. Ces différentes étapes d’inspection permettent au constructeur de s’assurer d’une qualité optimale de fabrication.
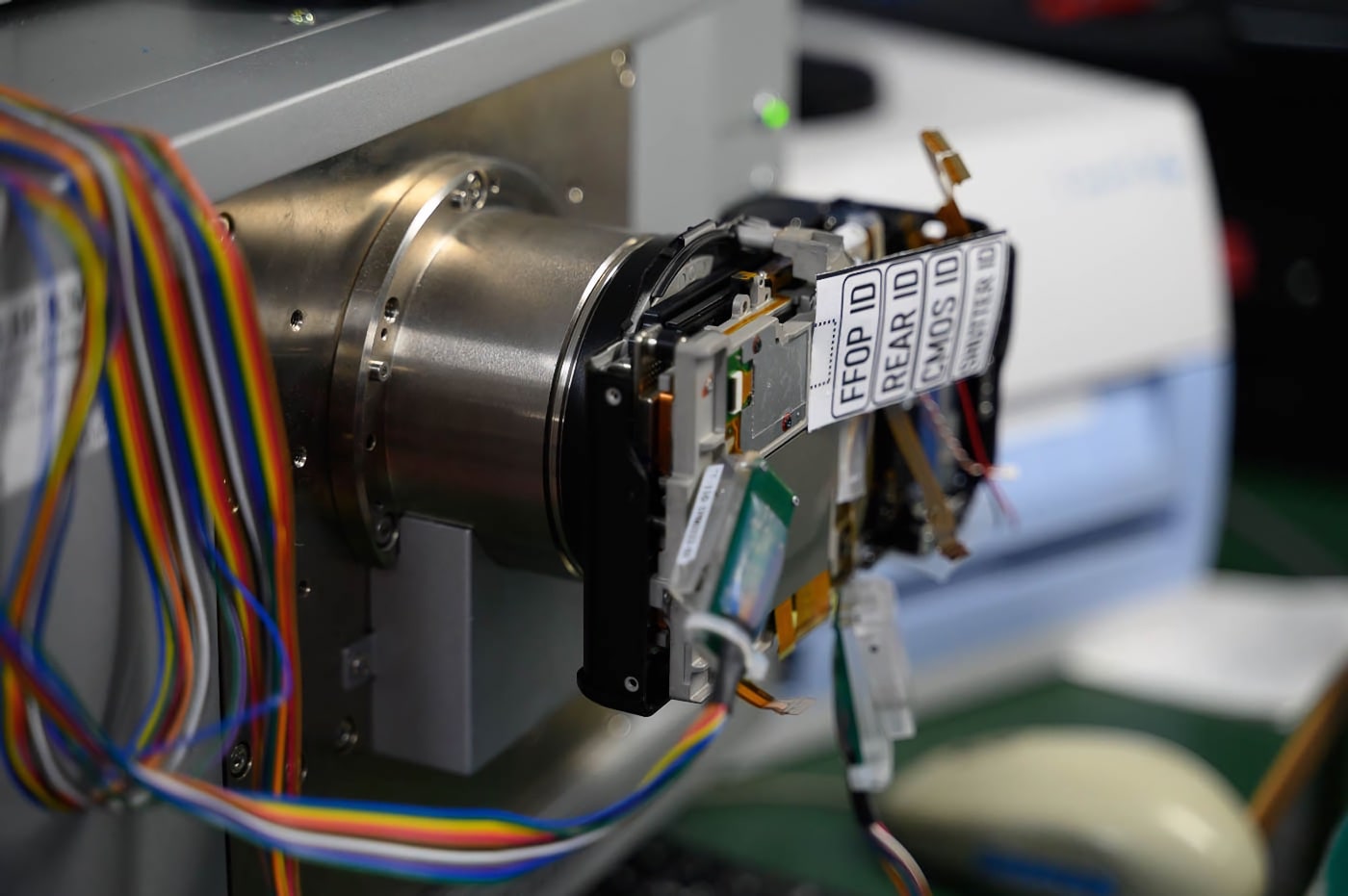
Et on aborde ici un point essentiel lié à cette usine : l’unité entre l’homme et la machine. Lors de notre visite, nous avons noté la présence de nombreux systèmes robotiques permettant d’automatiser ou de perfectionner l’assemblage et le contrôle qualité, en assistant les opérateurs sur la chaîne d’assemblage. Pour autant, les étapes d’assemblage des GFX sont souvent manuelles.


Ici par exemple, les différents boutons et vis sont placés à la main sur la facade du boîtier.
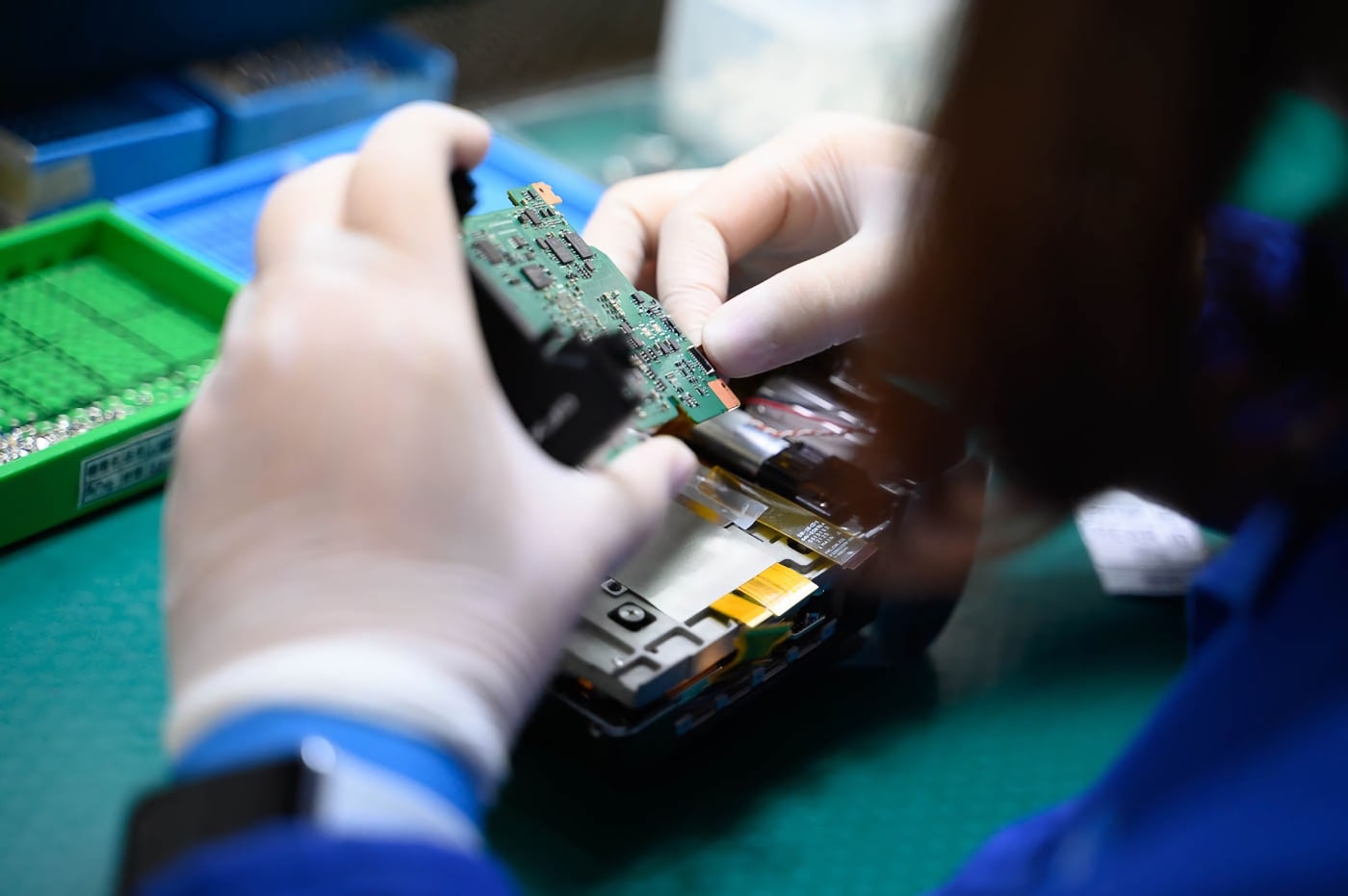
Les différents éléments électroniques, ainsi que la cage capteur, sont ensuite assemblés et connectés, tout comme la carte mère de l’appareil.
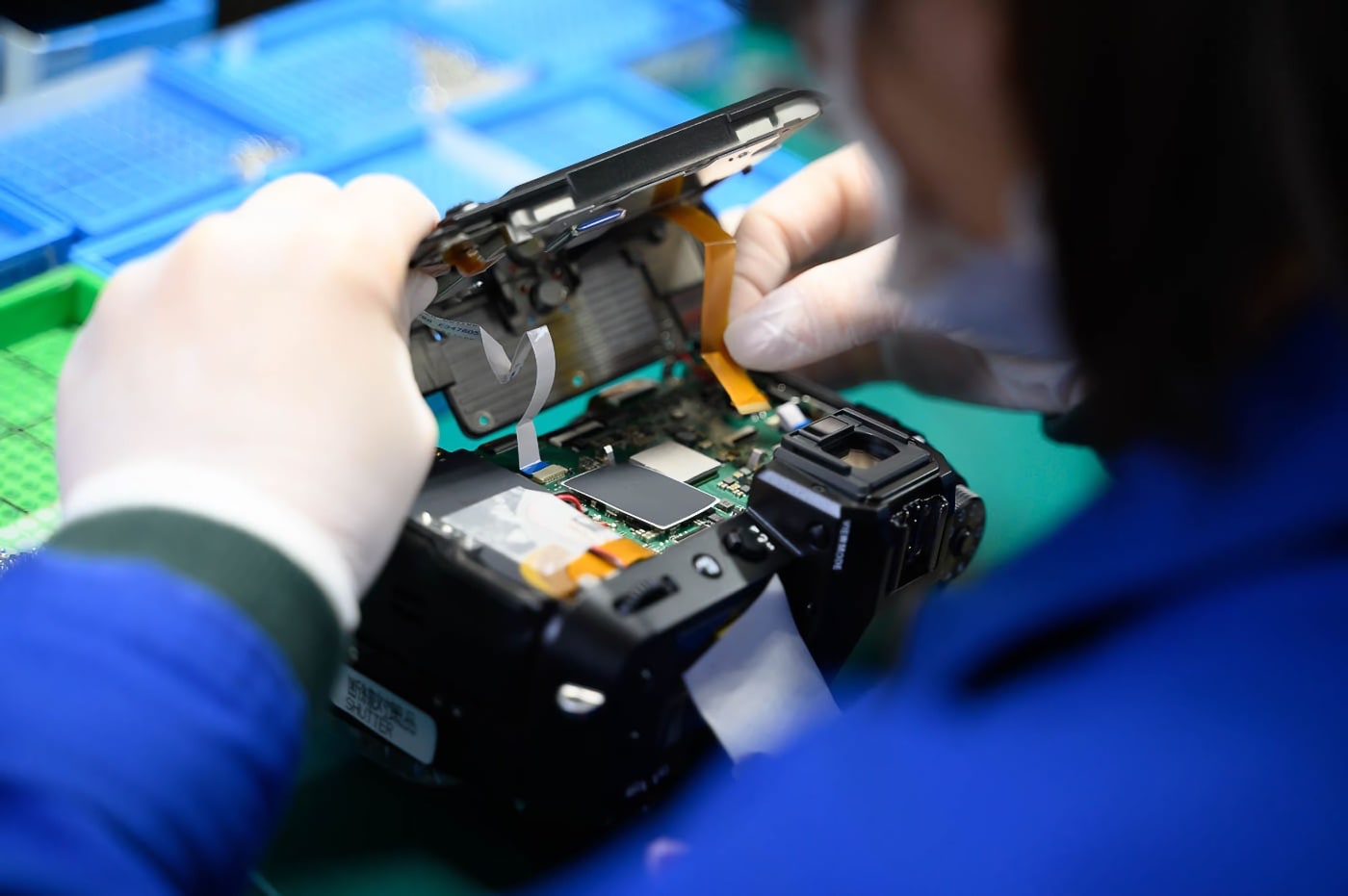
Une fois tous les composants intégrés, le dos du boîtier, avec l’écran inclinable, est assemblé. Ces différentes étapes passées, une machine permet d’appliquer une pression pour que l’ensemble soit bien solidaire.
Une fois les organes du GFX 100s assemblés, le boîtier est soumis à une batterie de test, notamment pour vérifier le bon alignement du capteur sur le plan focal, ainsi que le bon calibrage de la stabilisation. Ici, tout est automatisé, l’appareil réalisant une série de photos analysées ensuite par ordinateur. Si nécessaires, les micro-réglages sont appliquées automatiquement.


Ah, nous oublions une étape : l’application des différents revêtements du boîtier, tous effectués une fois encore à la main, grâce à quelques ustensiles et une bonne dose de dextérité. Fait intéressant, sous le caoutchouc, le plastique de la poignée sur la partie avant n’est pas opaque mais transparent. Une presse permet de vérifier que tous les caoutchoucs soient bien fixés.


Une fois ces étapes terminées, dernière inspection sous toutes les coutures pour être certain que le boîtier est prêt à aller à l’étape du packaging, avant de quitter l’usine pour être acheminé aux quatre coins du monde.
XF 150-600 mm f/5.6-8 R LM OIS WR : assemblage de l’objectif le plus complexe de Fujifilm
Mais notre visite de l’usine ne s’arrête pas là. Après avoir traversé les 100 mètres qui séparent les deux bâtiments, nous nous retrouvons dans la partie de l’usine dédiée à l’assemblage des objectifs. Et ici, nous aurons la chance de découvrir les étapes de fabrication du XF 150-600 mm f/5.6-8 R LM OIS WR, dévoilé en juin dernier avec le X-H2S.
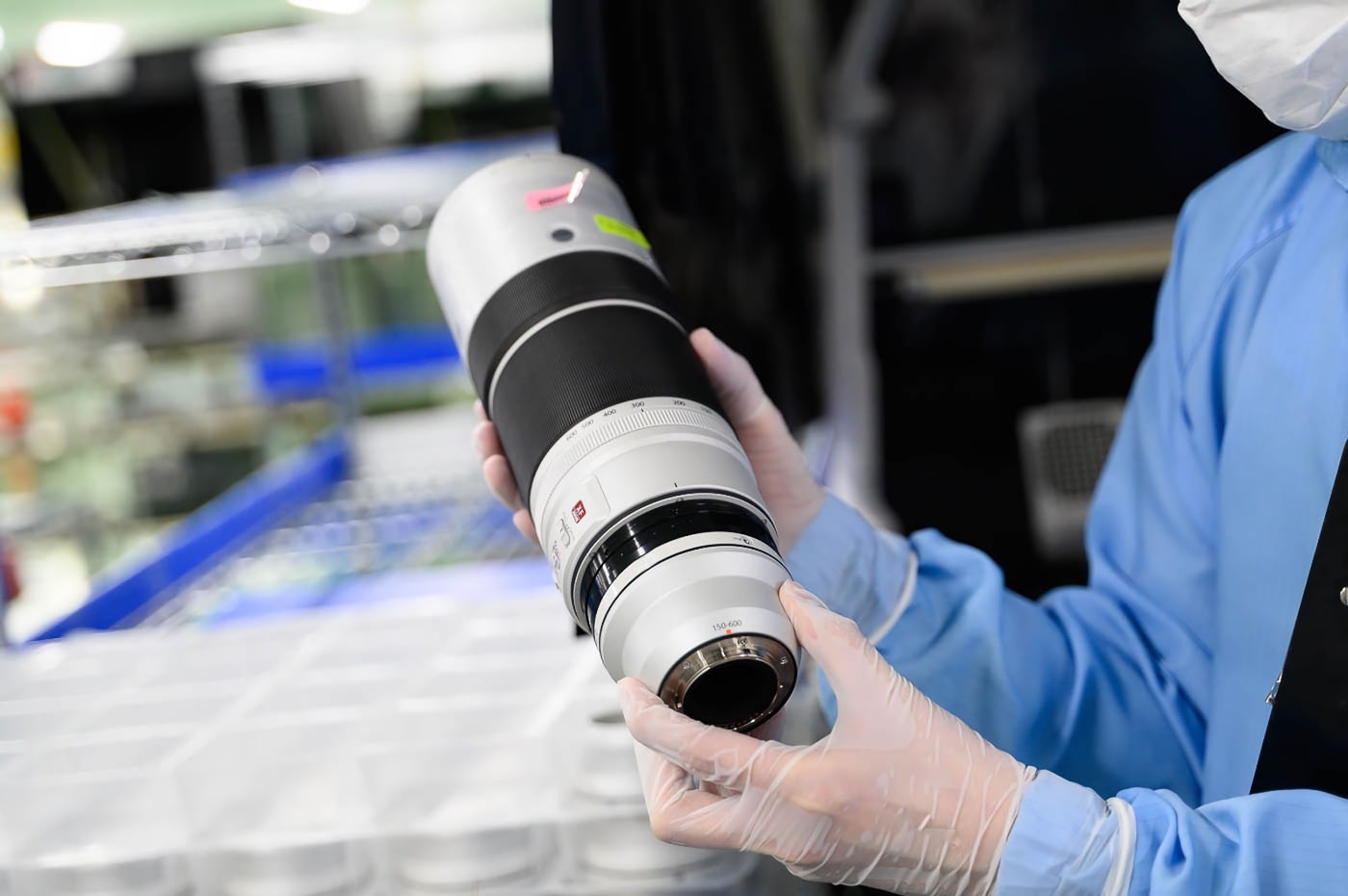
Dans un couloir, nous passons devant un objectif XF 100-400 mm f/4,5-5,6 R LM OIS WR dont tous les composants sont présentés de manière éclatée. Cela permet d’apprécier le nombre d’éléments à assembler pour ce genre de télézoom. Jusqu’ici, il s’agissait de l’objectif Fujifilm comprenant le plus de composants. Mais c’est désormais le 150-600 mm à qui revient la palme, avec plus de 1000 pièces (des lentilles à la plus petite vis).
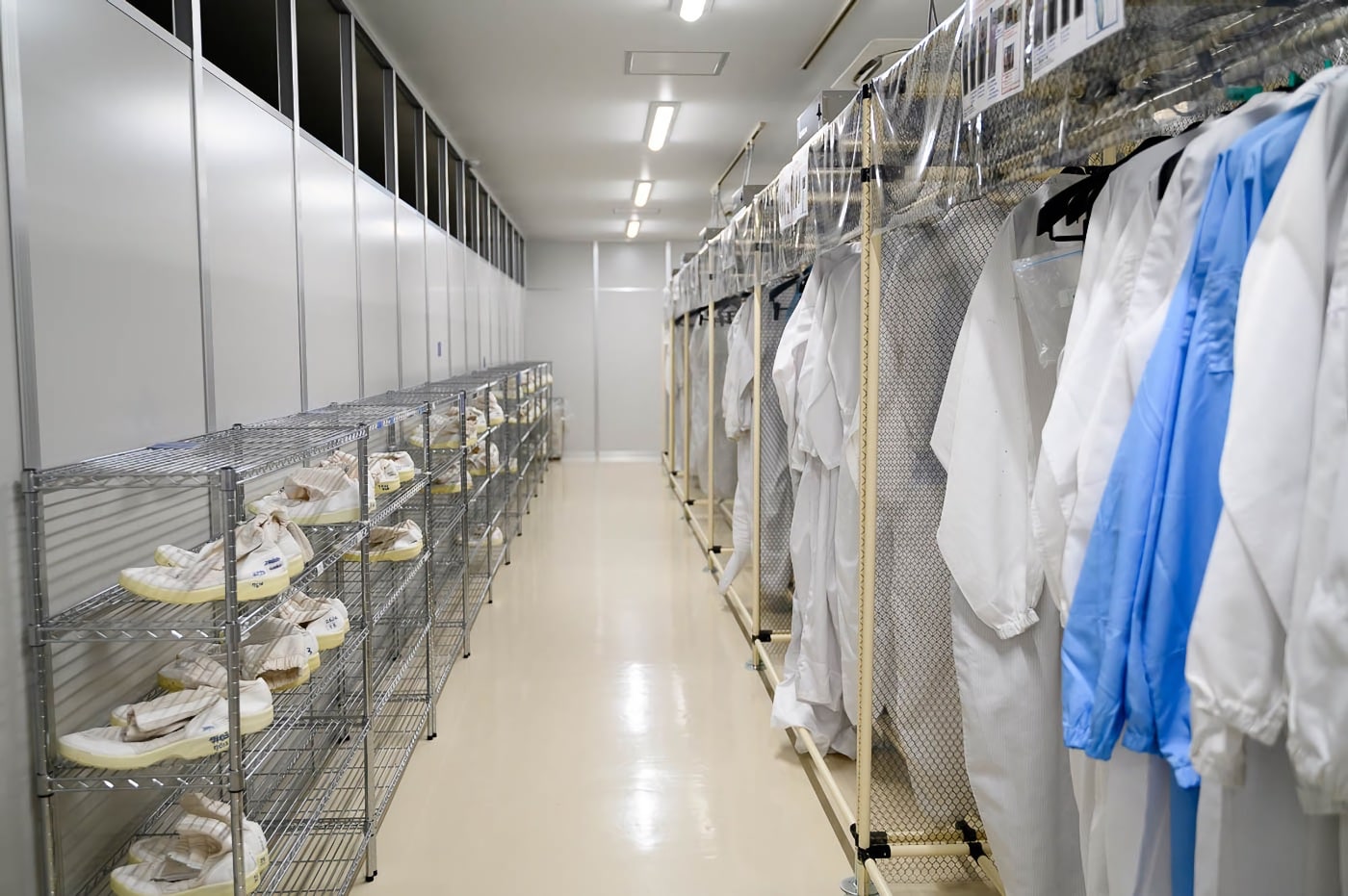
Avant de pouvoir entrer dans la zone d’assemblage, il faut passer par le vestiaire. En effet, l’assemblage des objectifs chez Fujifilm se fait en salle blanche, afin de minimiser le nombre de particules dans l’air et réduire au maximum les risques de poussière. De grands ventilateurs et un système d’aspiration d’air sont mis en place. Une lampe à lumière verte permet même de mettre en évidence la moindre poussière.
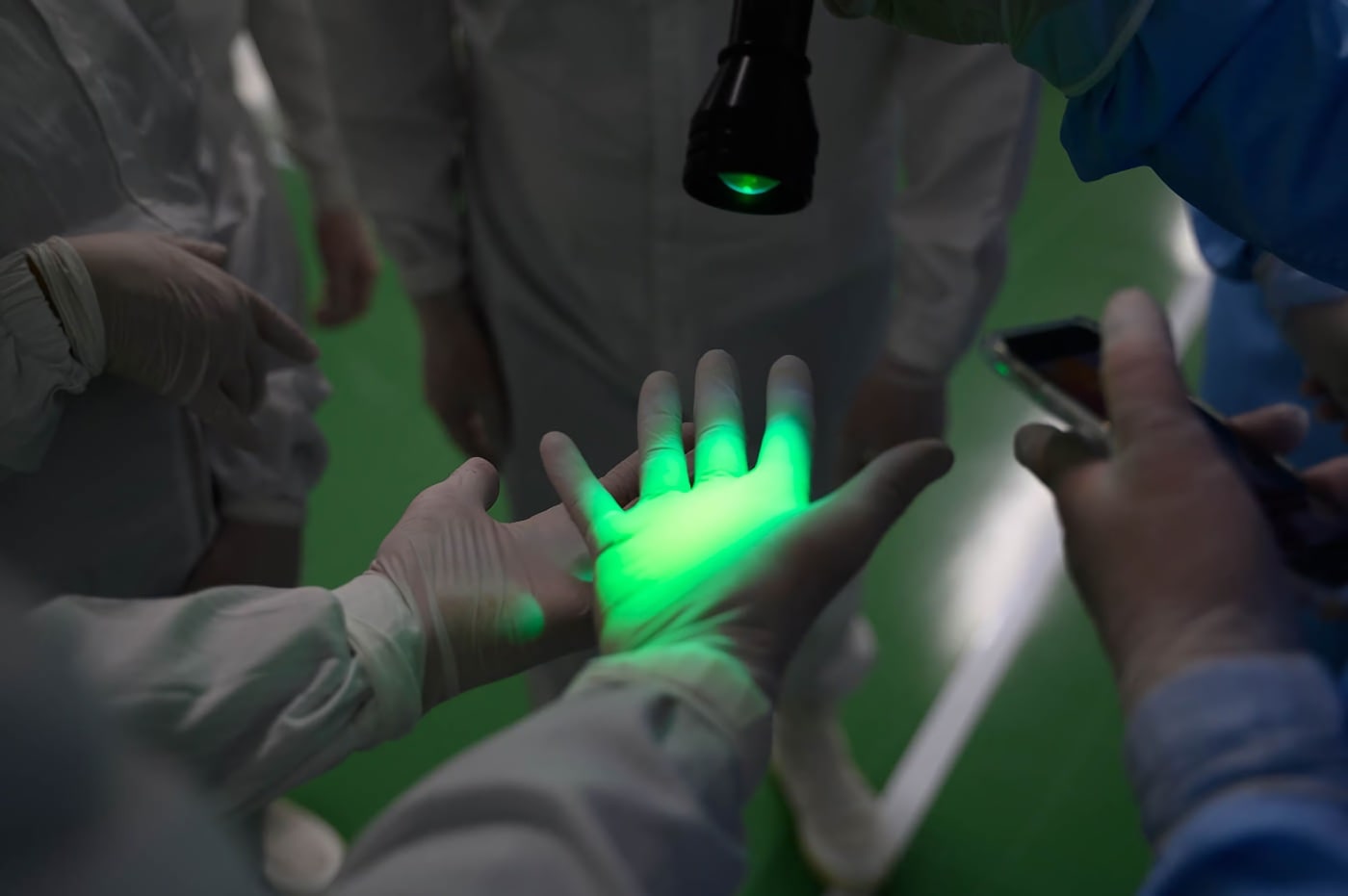
Même traitement pour les différentes pièces qui arrivent depuis l’entrepôt : celles-ci passent par un sas et disposent de deux couches d’emballage, le premier emballage étant retiré avant le stockage dans la chambre blanche pour éviter les poussières venues de l’extérieur.
La température et le niveau d’humidité sont également régulés toute l’année, afin de réduire la quantité de poussière. Ainsi, chaque employé – et visiteur – doit se préparer avec blouse, chaussures, charlotte et masque avant d’accéder à cette partie de l’usine. Un passage par un sas ventilé est aussi obligatoire.


Dès qu’une poussière est trouvée, elle est directement envoyée au laboratoire afin d’en trouver la source et changer les process pour l’éviter. Autant dire que lorsque des gens externes au service visitent l’usine, les conditions sont strictes, avec notamment l’obligation de retirer toute sangle de son appareil photo, et d’utiliser une feuille de papier spécifique plutôt que son carnet de notes habituel.
Dans la salle blanche, l’objectif prend forme progressivement. Le XF 150-600 mm dispose de 8 groupes de lentilles, soit autant d’étapes, chaque groupe optique étant assemblé séparément.



Une machine vient assister l’opérateur pour assembler les lentilles au sein d’un barillet. Si cette étape était effectuée à la main, on observerait des variations en termes d’alignement. C’est pour cette raison que des machines de précision sont utilisées – 1 degré de décalage a beaucoup d’influence, surtout lorsqu’il est multiplié par le nombre de lentilles.
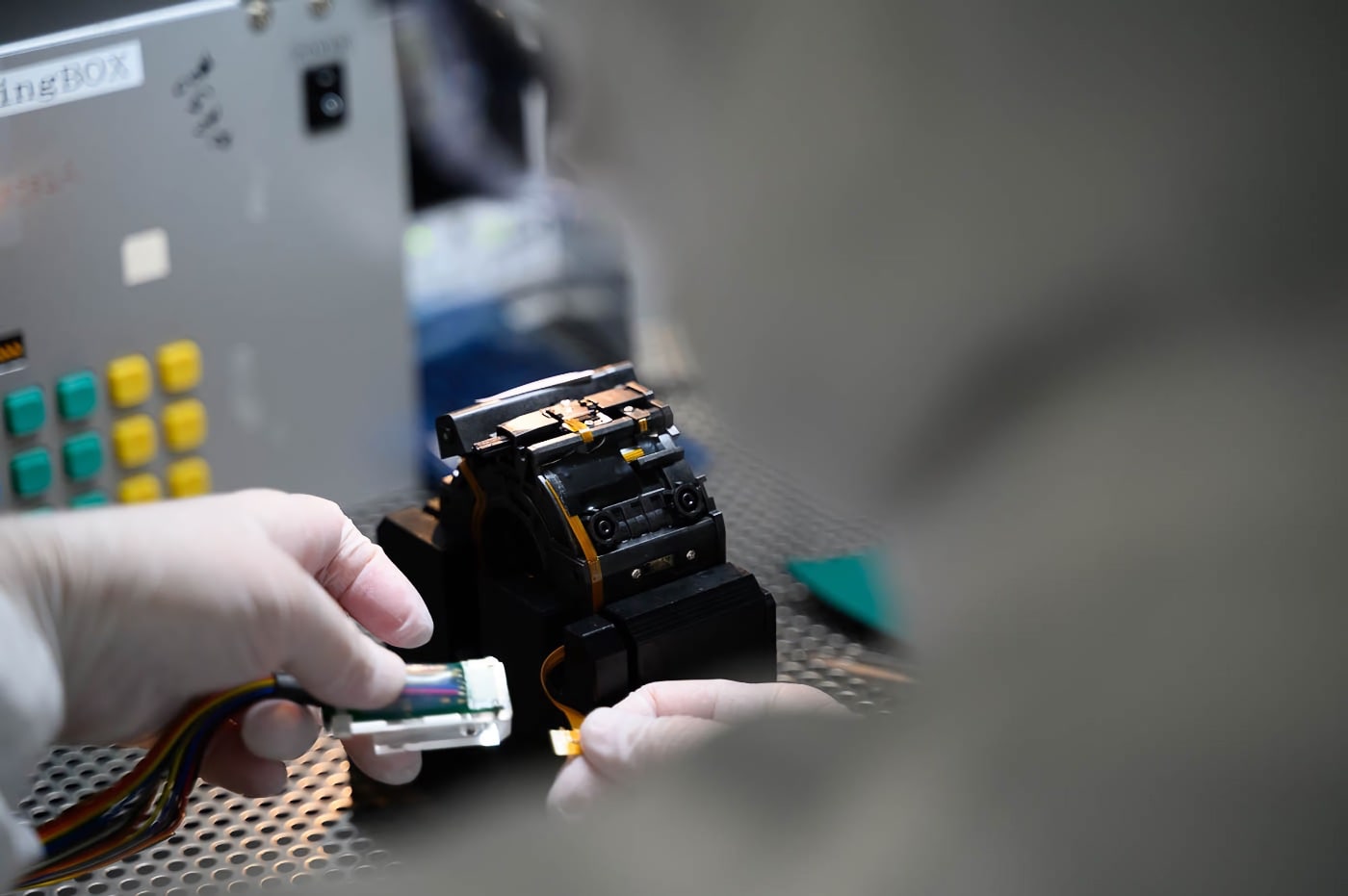
Pour certaines étapes, des sous-étapes sont nécessaires, par exemple pour regrouper ou coller plusieurs lentilles ensemble.
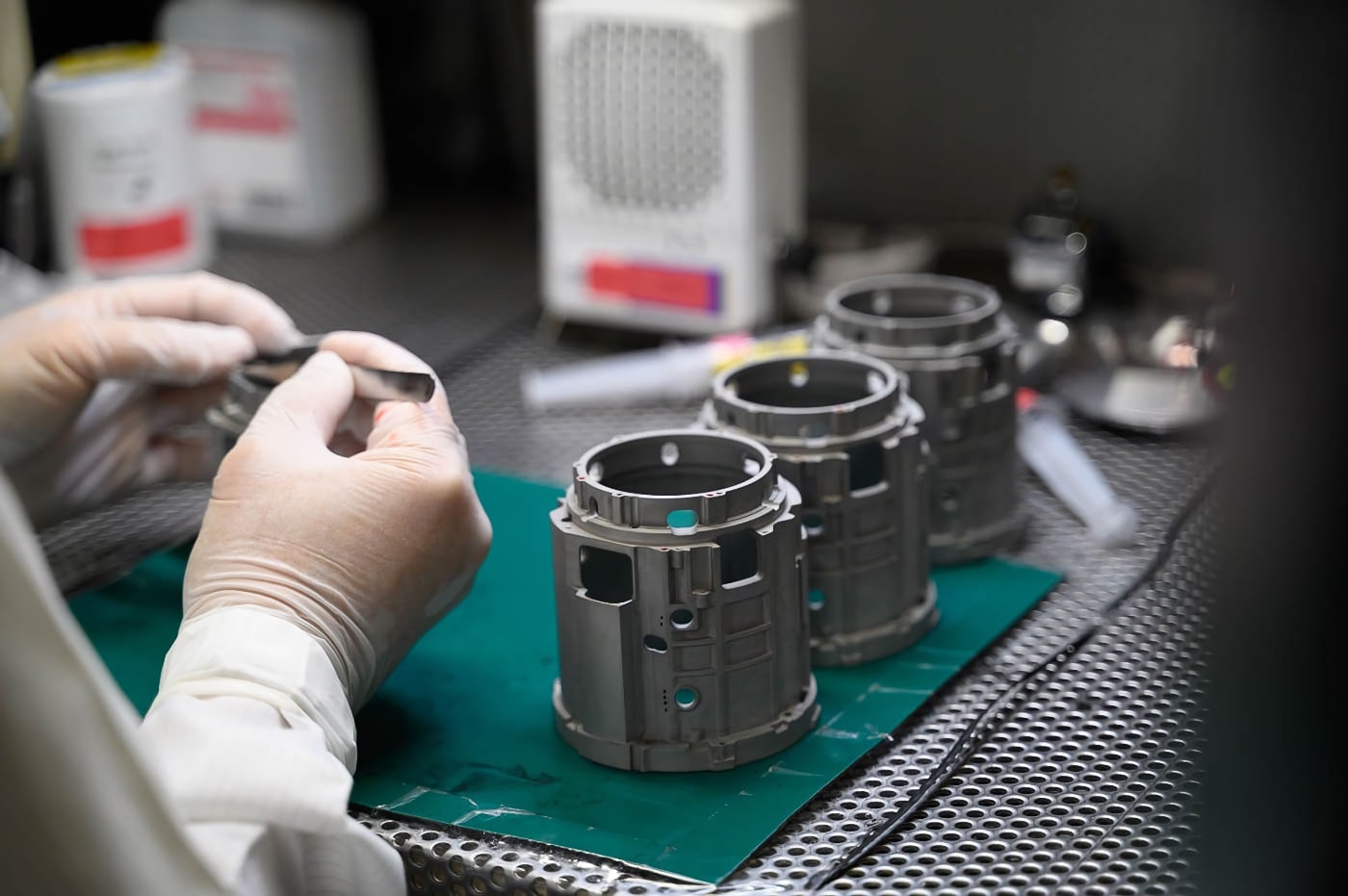
À chaque étape, une vérification manuelle des lentilles s’impose. Les employés disposent de « chambres noires » avec un éclairage précis pour mieux voir les poussières ou imperfections.

Lors de notre visite, nous avons pu noter la dextérité dans le nettoyage des optiques. Cela peut sembler simple, mais le geste est en réalité très difficile.


L’objectif nu – dépourvu de son fût complet – est ensuite placé sur des machines dans de petits box individuels pour un ajustement précis sur charte MTF. Ici, tout est automatisé, mais cette étape peux prendre jusqu’à 1h par objectif, selon les besoins.


Une fois validée, les pièces extérieures sont ajoutées, comme le collier de pied ou le fût blanc caractéristique de cet objectif. Pour rappel, la couleur blanche argentée permet de limiter la hausse de température au sein de l’objectif en plein soleil.




Enfin, avant d’être placés dans leur boîte, une machine vient graver le numéro de série sur le fût. Ensuite, l’objectif est placé dans une autre machine pour une dernière vérification automatisée, en plus d’un contrôle visuel. Si tout est bon, l’objectif est emballé et pesé, afin d’être certain qu’aucun élément n’a été oublié.


Les cartons sont ensuite stockés dans l’entrepôt, juste à côté où les différents composants ont été livrés par les autres usines Fujifilm : la boucle est bouclée, les colis sont prêt à partir avec un envoi par avion depuis l’aéroport de Narita.


Questions / réponses
Avant de repartir pour la gare de Sendai et attraper notre Shinkanzen pour Tokyo, nous avons pu poser quelques questions aux dirigeants de l’usine Fujifilm Taiwa dont M. Kazuhiro Anzai, General Manager de l’usine Fujifilm de Taiwa. Place à l’interview.
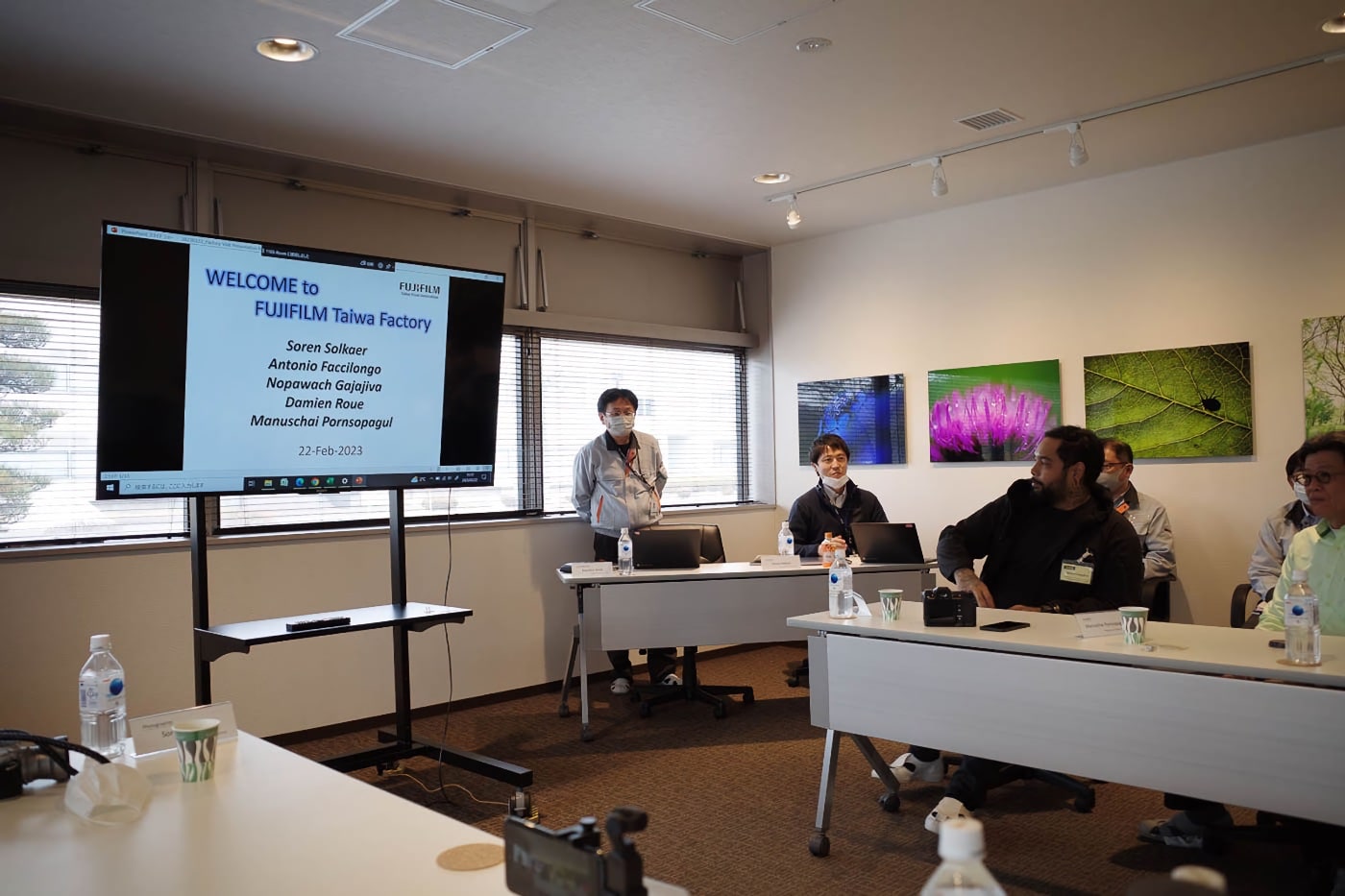
Quel est le produit le plus complexe à assembler ?
Je pense qu’il s’agit de l’objectif XF 150-600 mm f/5.6-8 R LM OIS WR que vous avez vu aujourd’hui, car sa conception technique est très avancée, ce qui rend l’assemblage et le contrôle qualité plus difficile.
Cet objectif a plus de 20 éléments optiques qui doivent rentrer dans un fût le plus compact possible, ce qui fait que la moindre variation n’est pas acceptable en termes de qualité. La fabrication d’objectifs devient donc de plus en plus difficile.
De manière plus générale, la fabrication d’objectifs pour boîtiers GFX est plus complexe que celle d’optiques XF car la qualité d’image attendue est supérieure en termes de résolution. L’étape de réglage sera ainsi plus longue et importante. Fujifilm utilise des chartes de test très spécifiques pour vérifier la qualité d’image et le réglage des objectifs.
Combien de temps faut-il pour produire un objectif comme ce XF 150-600 mm f/5.6-8 R LM OIS WR ?
La durée ne peut pas être dévoilée car les éléments sont fabriqués dans 4 usines puis assemblés ici à Taiwa. Mais fabriquer une seule optique prend donc beaucoup de temps si l’on compte toutes ces étapes. Le XF 150-600 mm est d’ailleurs composé de plus de 1000 pièces.
Quelles sont les étapes pour devenir employé dans l’usine de Taiwa ?
Comme vous vous en doutez, les travailleurs ne peuvent pas directement commencer à travailler sur la ligne de production. Chaque processus dans la ligne d’assemblage doit être enseigné, ce qui prend du temps. Nous formons donc les salariés. La production d’objectifs est encore plus difficile, notamment la partie réglage. Par exemple, la formation dure environ 1 mois pour le réglage optique.
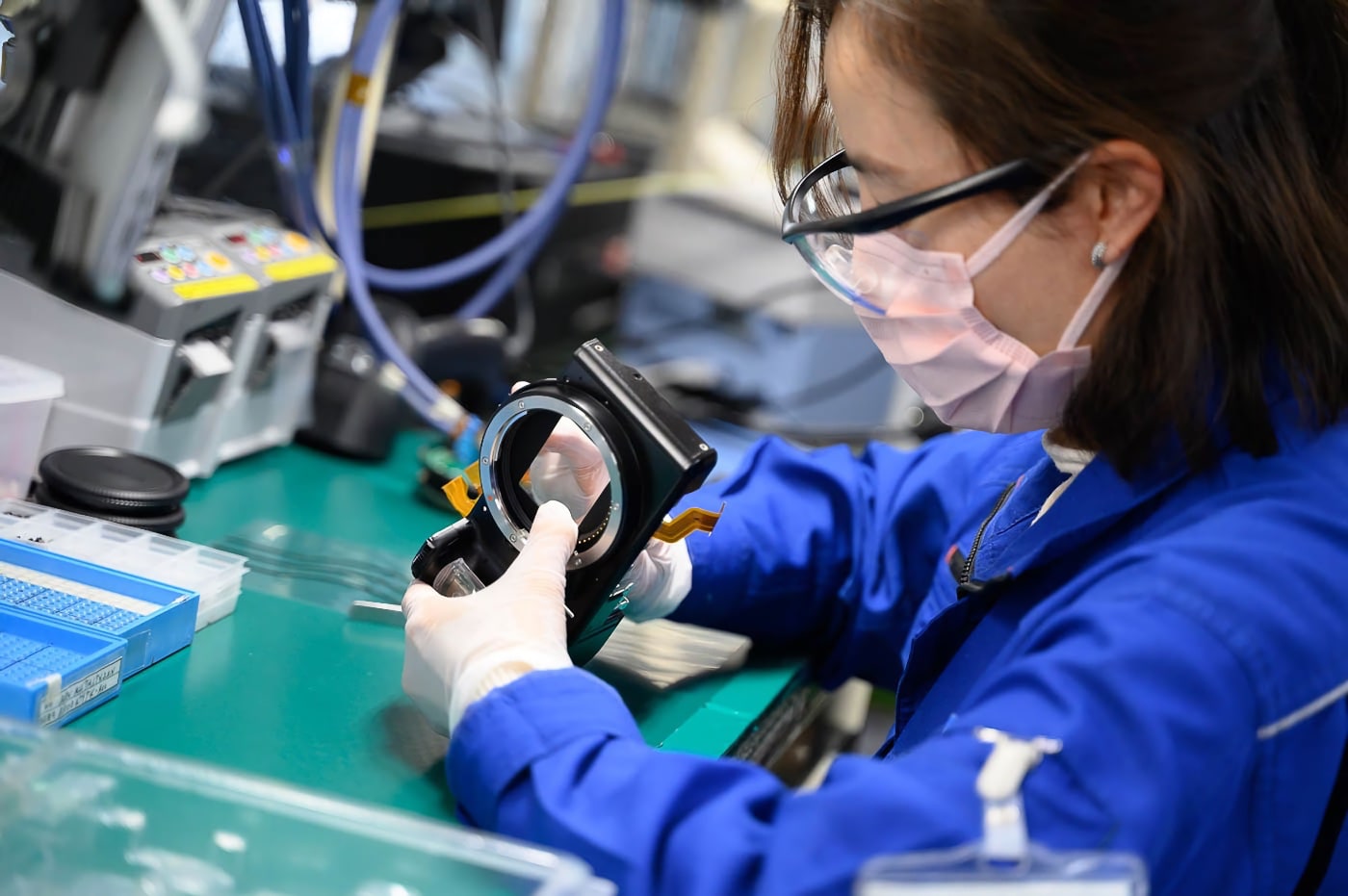
Il est également possible de changer de poste, cela dépend du produit. Au début, un travailleur débute sur un poste bien particulier. Avec le temps, si le travailleur gagne de l’expérience et a suffisamment de connaissances, il peut s’occuper d’autres chose.
Cela dépend également de la quantité de produits à fabriquer : si le volume est réduit, il est possible de faire plusieurs tâches à la fois.
Comment décidez-vous quels produits sont fabriqués au Japon ?
Bien sur, les boîtiers GFX et les objectifs les plus complexes comme le 150-600 mm sont fabriqués au Japon. L’usine de Taiwa conçoit ensuite tous les procédés afin de s’assurer que la qualité de production soit maintenue, y compris au sein de nos autres usines. Le critère est dont principalement lié à la difficulté et à la nécessité d’un haut niveau de compétence et d’inspection.
La pénurie de semi-conducteurs est-elle toujours un sujet d’actualité pour la production chez Fujifilm ?
Nous avons encore des pénuries en terme de semi-conducteurs, ce qui affecte notre production, à la fois d’appareils photo et d’objectifs. Ce n’est pas seulement à Taiwa. Notre division Approvisionnement au siège de Fujifilm à Omiya essaie de trouver une solution.
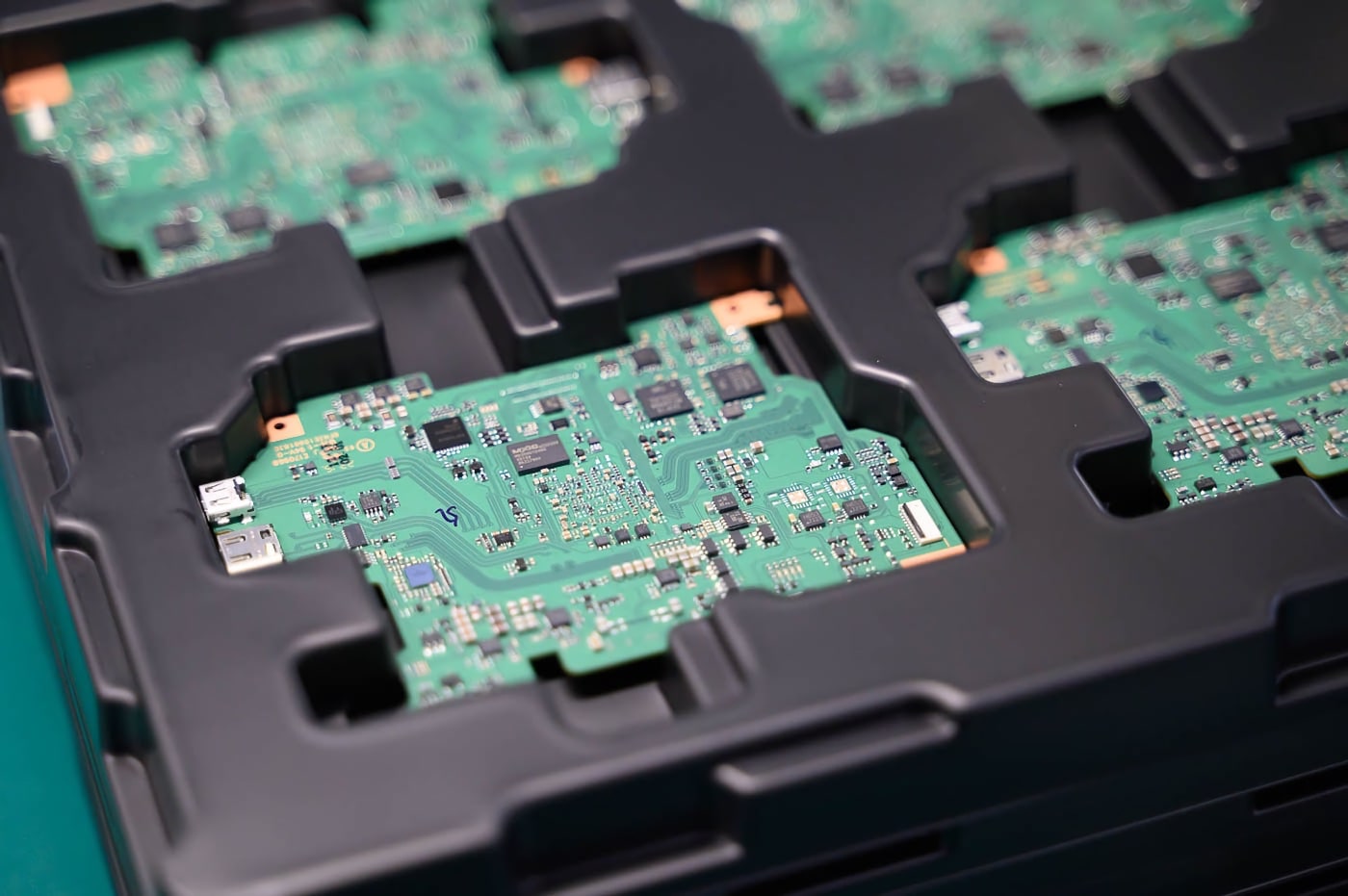
Le X100V, fabriqué au Japon à Taiwa, est victime d’un certain succès. Quand les composants arrivent, il faut fabriquer le boîtier le plus vite possible, donc nous cherchons également comment réduire le délai de livraison de l’usine au client final.
Dans tous les cas, nous faisons de notre mieux pour faire en sorte que cette pénurie affecte le moins possible nos clients.
Quelles sont les technologies les plus récentes qui pourraient être utilisées pour améliorer la fabrication des objectifs et des appareils photo ? IA, vision artificielle, etc. ?
[Réponse d’un ingénieur en charge de la conception des processus de production] : Nous mettons en place de nouvelles technologies; mais pas forcément liées à l’intelligence artificielle. Par exemple, les capteurs des boîtiers GFX sont très sensibles en terme d’alignement. Nous avons donc conçu, après le lancement du système GFX, un système automatisé pour le réglage.C’est la même chose pour les objectifs GF ou XF : le réglage est la clé de la qualité d’image. En plus de photos de charte pour s’assurer de la qualité, nous avons mis en place des systèmes automatisés basés sur des algorithmes pour réduire la durée de cette étape de réglage, qui est très importante pour nous. L’intelligence artificielle pourrait être le futur, y compris dans l’étape de production, mais ce n’est pas encore le cas.
A l’étape de l’emballage, des clichés sont réalisés afin de s’assurer de la qualité du packaging. Ce n’est pas vraiment un procédé de vision industrielle mais cela s’en rapproche.
Mais vous l’avez vu durant la visite de l’usine, la majorité des étapes d’assemblage sont réalisées à la main par des hommes et des femmes.
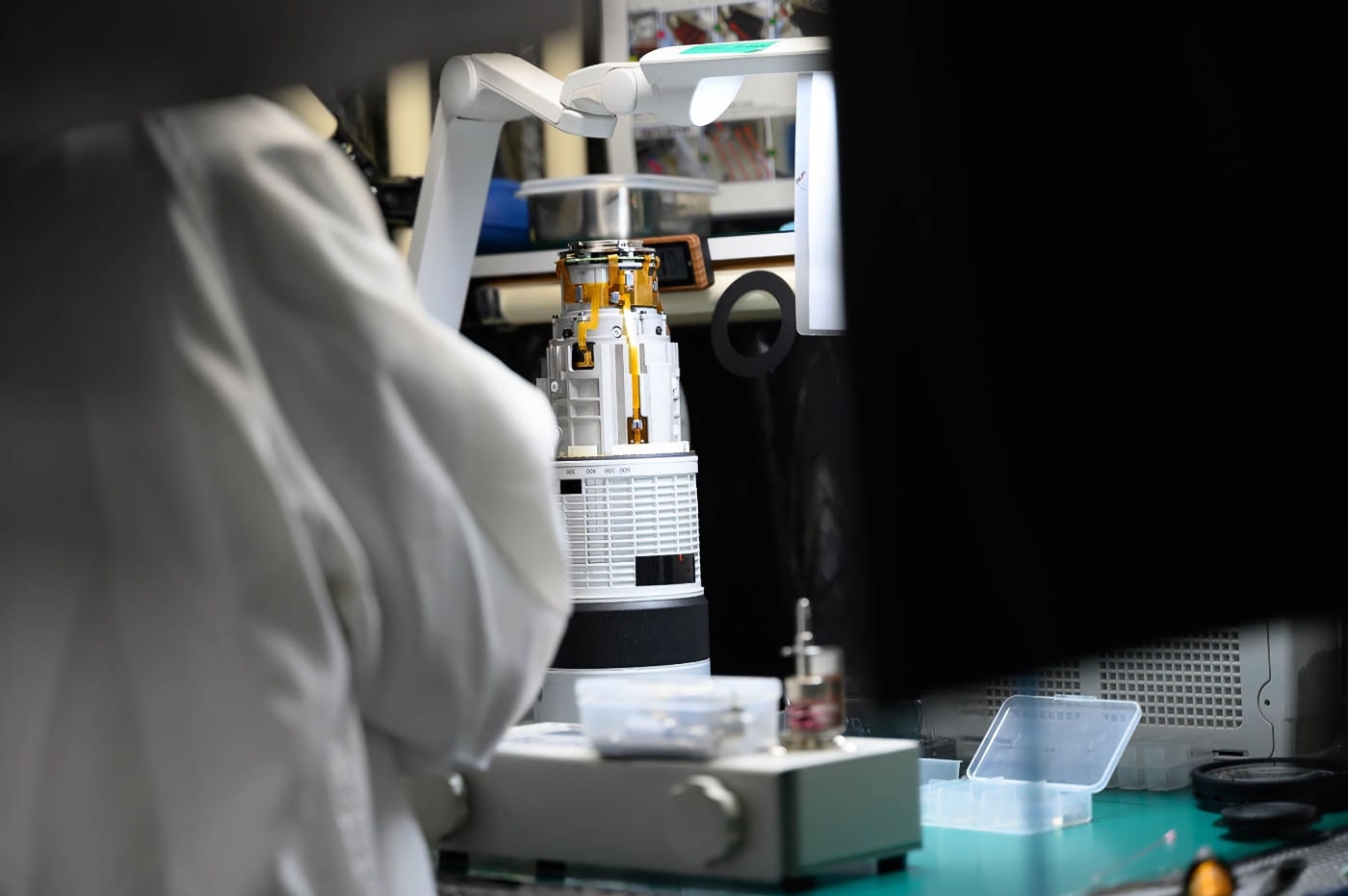
Conclusion
Visiter une usine de fabrication de matériel photographique est toujours aussi passionnant. Chez Fujifilm, l’usine de Taiwa est d’autant plus importante qu’elle ne rassemble pas que l’assemblage de certains produits haut de gamme, mais sert aussi de centre de recherche et de référent pour le contrôle qualité et les processus industriel des différentes usines Fujifilm dans le monde. Au sortir de notre visite, nous ne pouvons que noter le savant mélange entre le travail humain et la technologie employée par le constructeur pour être certain que tout est parfait à chaque étape de l’assemblage et de réglage de l’optique ou du boîtier.
Merci à Fujifilm Corp et à Fujifilm France de nous avoir permis d’organiser cette visite d’usine en marge du CP+ 2023. Vous pouvez retrouver nos autres visites d’usine sur cette page.