Lors de notre visite au Japon pour couvrir le CP+ 2024, nous avons eu l’opportunité de découvrir une usine Nikon essentielle à la production d’objectifs : Nikon Hikari Glass. Située à Yuzawa, dans la préfecture d’Akita (à environ 500 km au nord de Tokyo), c’est ici que le verre optique prend vie grâce au processus de fusion.
Ce procédé, à la fois fascinant et exigeant, constitue la première étape de la création du verre utilisé non seulement dans les objectifs Nikkor, mais aussi dans divers instruments de haute précision. Le verre ainsi fabriqué est ensuite façonné en galettes avant d’être expédié vers les usines d’assemblage, où il sera poli pour atteindre les propriétés optiques finales requises. Suivez-nous pour cette visite captivante.
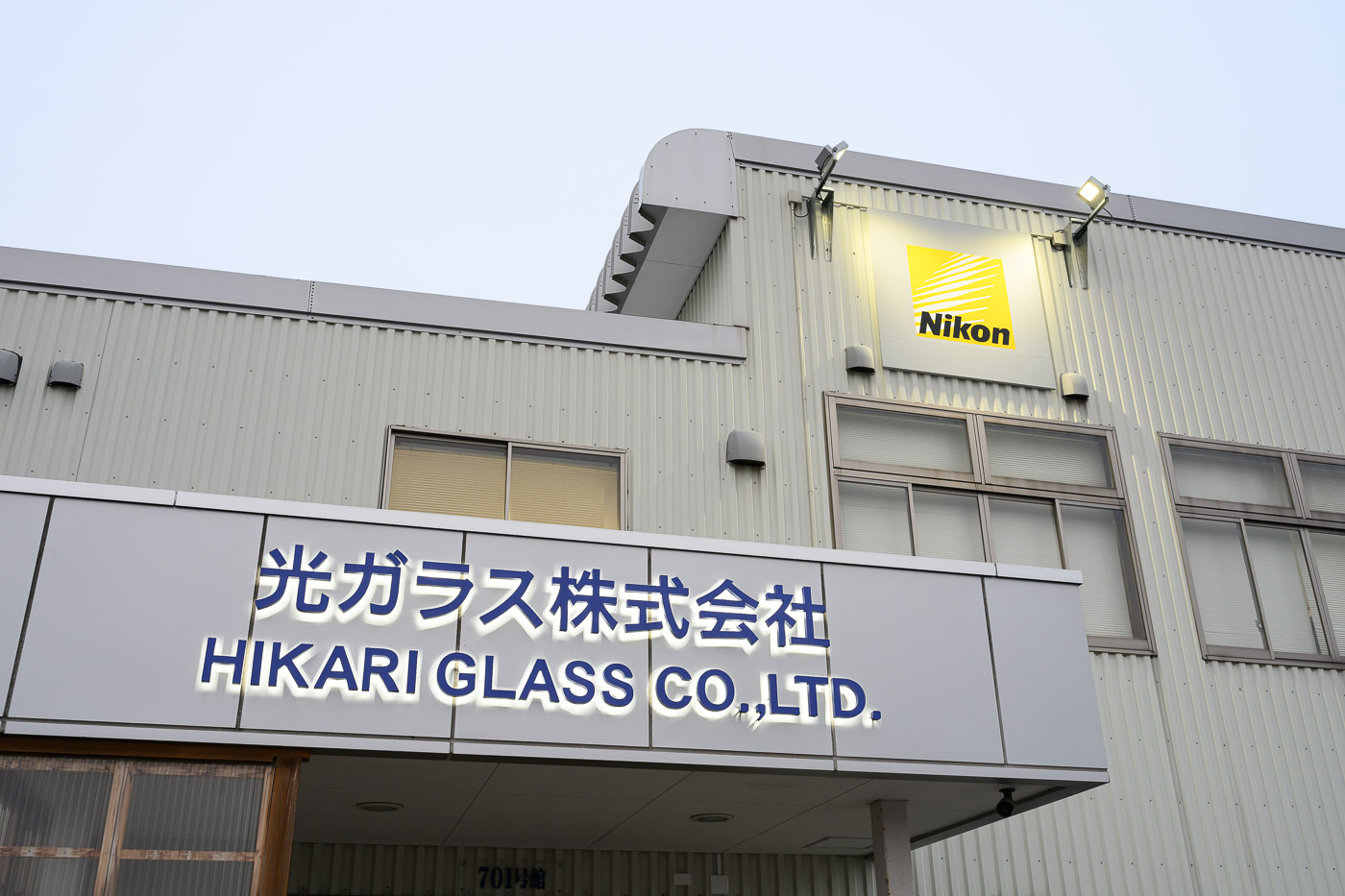
Sommaire
- Nikon et le verre optique : un peu d’histoire
- Qu’est-ce que le verre optique ?
- Hikari Glass, le pilier optique de Nikon
- Mélange et fusions : les premières étapes
- Fusion continue : du verre en barre
- Découpage et calibrage des morceaux de verre
- La presse, ultime étape de transformation pour les blocs de verre
- Bilan de la visite de Nikon Hikari Glass
Nikon et le verre optique : un peu d’histoire
Nikon, fondée en 1917 sous le nom de Nippon Kogaku K.K., est une entreprise japonaise réputée pour ses innovations dans le domaine des équipements optiques. Dès ses débuts, Nikon a mis l’accent sur le développement et la production de produits optiques de haute qualité, répondant aux besoins croissants du marché d’alors.
Un an seulement après sa création, Nikon commença à fabriquer du verre optique. Cette initiative visait à réduire la dépendance du Japon vis-à-vis des importations et à promouvoir une production nationale.
La fabrication de verre optique est un processus complexe nécessitant une maîtrise parfaite des techniques de fusion et de traitement du verre. Au départ, Nikon a rencontré de nombreux défis techniques, notamment sur le contrôle précis des températures de fusion et la pureté des matières premières.
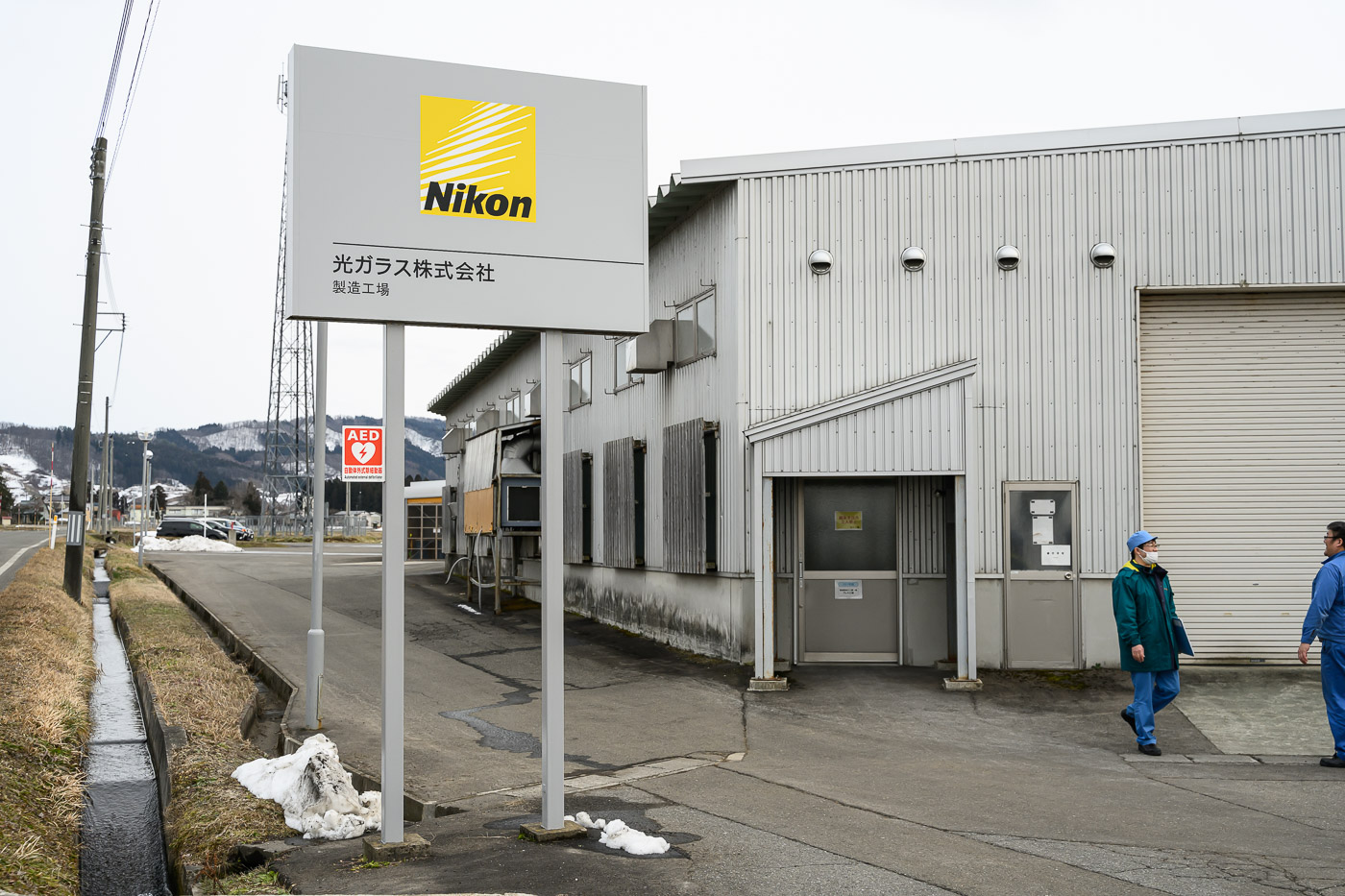
Malgré ces difficultés initiales, Nikon a réussi à surmonter les obstacles techniques et a établi sa propre technologie de fabrication de verre optique en 1932. À cette époque, le principal processus utilisé était la « fusion en creuset« . Ce procédé consistait à mélanger des matières premières telles que la silice (SiO2), le carbonate de sodium (Na2CO3), le lanthane (La) et la chaux (CaCO3) dans un creuset revêtu d’oxyde d’aluminium. Le mélange était ensuite chauffé à des températures comprises entre 800 et 1400 °C, puis le verre formé était extrait en brisant le creuset, avant d’être façonné et poli.
La mise au point de ce procédé a permis à Nikon de produire en masse du verre optique de haute qualité, marquant un tournant dans l’industrie optique japonaise et contribuant au développement technologique du pays.
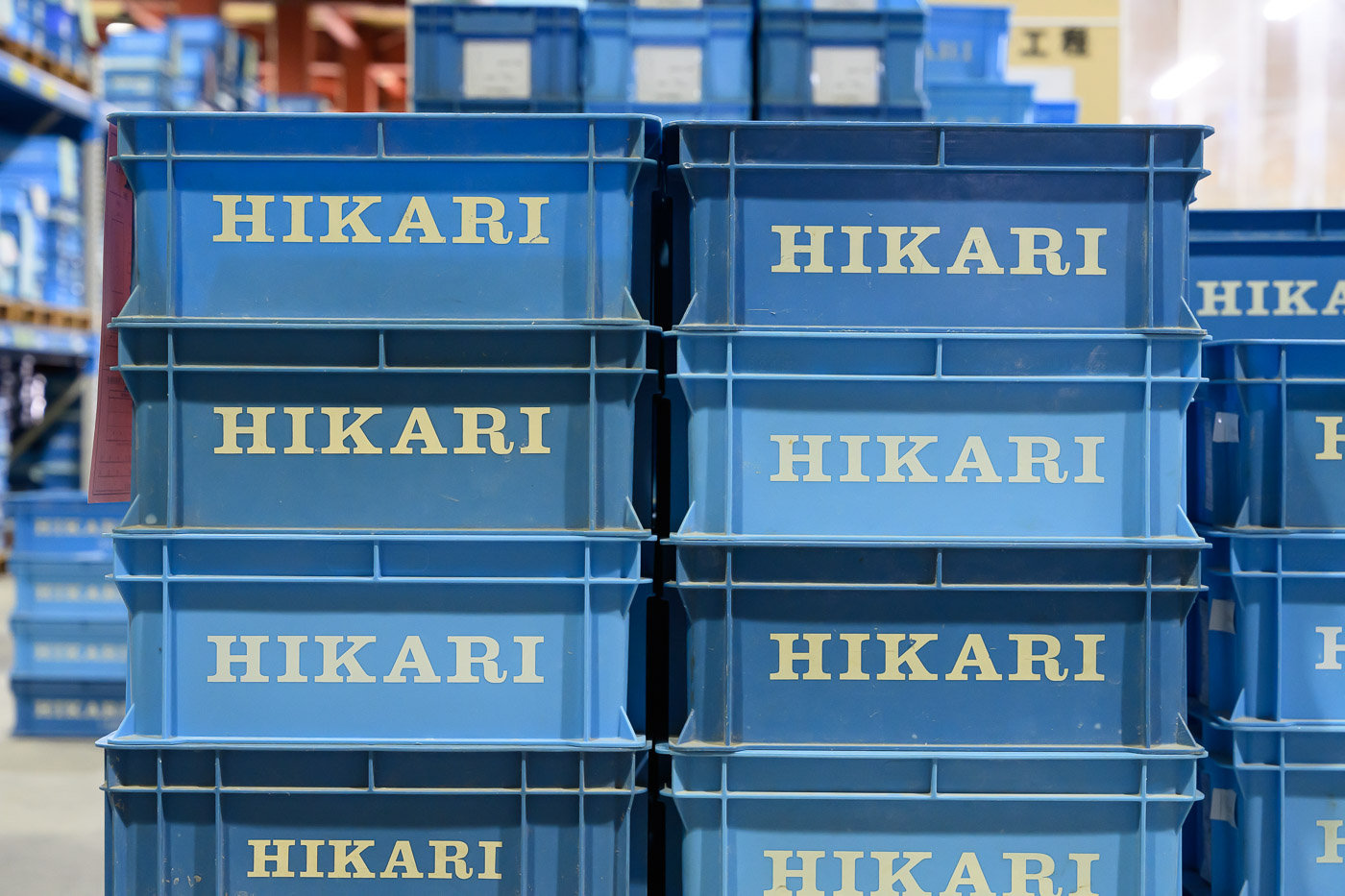
Cependant, la méthode de fusion en creuset présentait certaines limitations, notamment des rendements assez faibles et une qualité de verre variable. Ces contraintes ont incité Nikon à rechercher des méthodes plus efficaces et fiables pour améliorer autant la qualité que la quantité de verre produit.
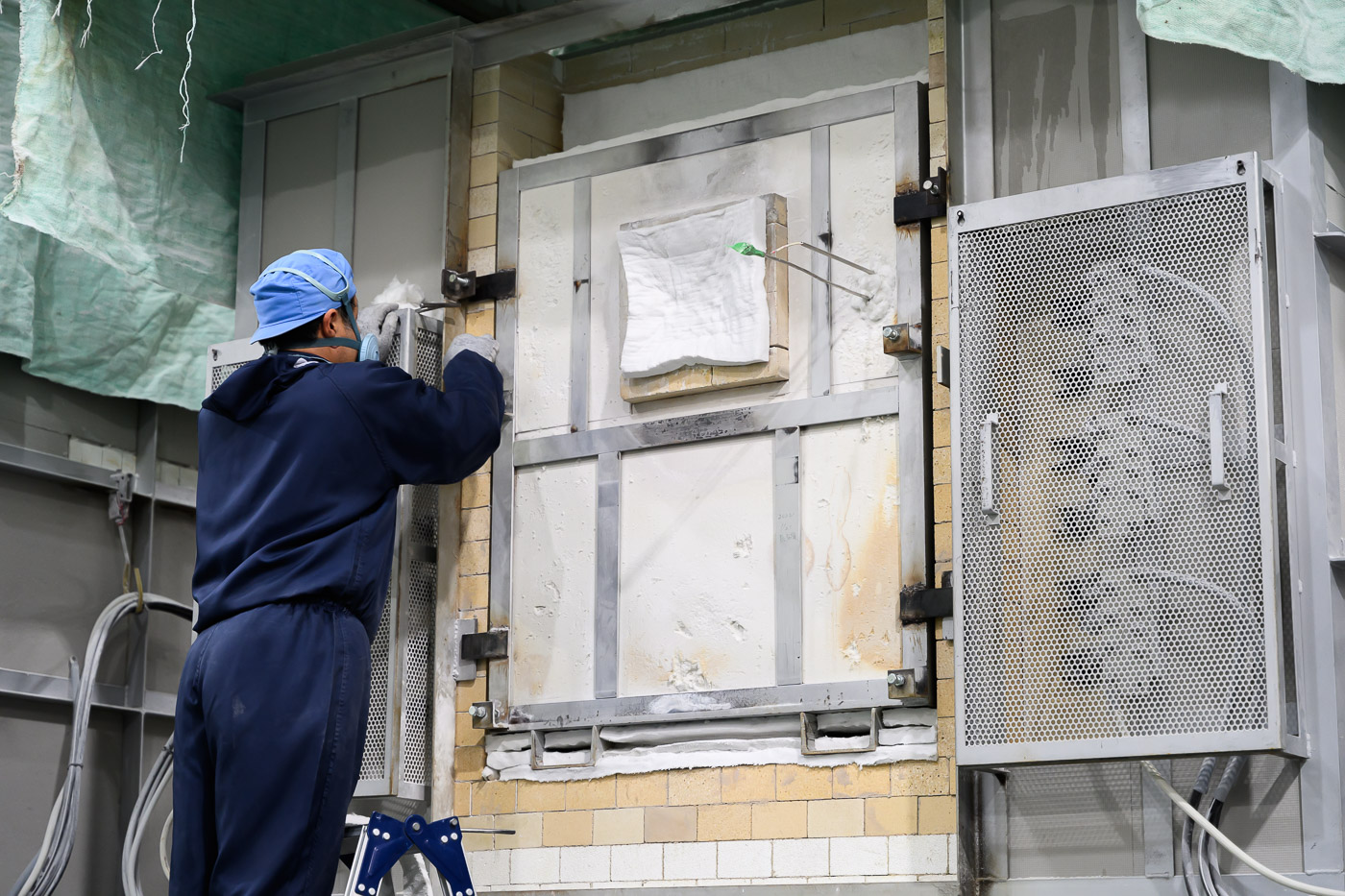
Pour surmonter ces défis, Nikon a adopté en 1983 une nouvelle méthode de fabrication appelée « fusion continue ». Ce processus moderne, encore utilisé dans l’usine Hikari Glass, est plus automatisé et permet une production plus uniforme et de meilleure qualité. La fusion continue permet également de produire du verre optique sous forme de plaques, simplifiant les étapes ultérieures de façonnage et de polissage.
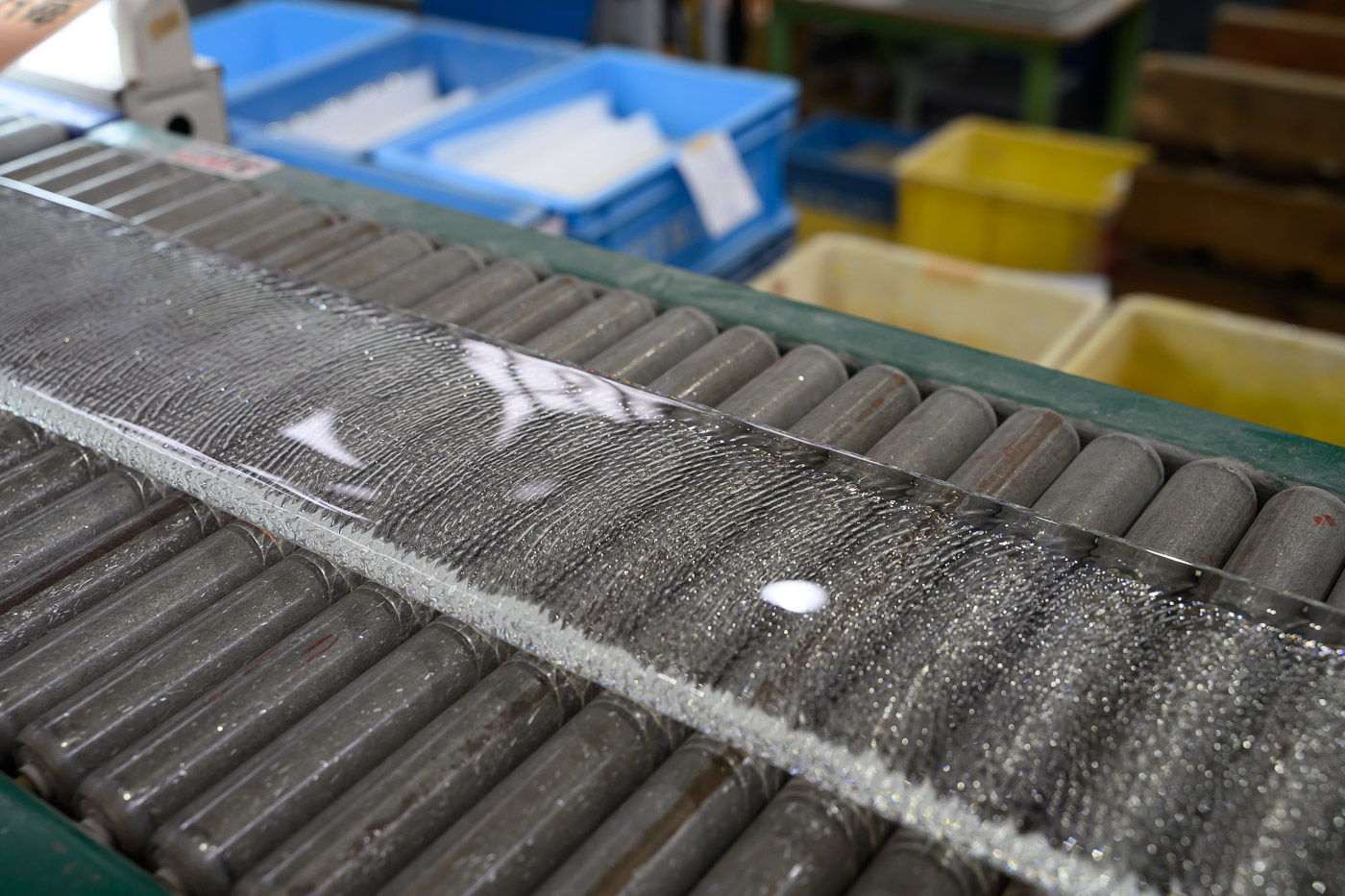
Qu’est-ce que le verre optique ?
En photographie, l’intérêt du verre optique par rapport au verre classique réside principalement dans ses propriétés spécifiques et ses performances accrues.
Ce type de verre est obtenu en faisant fondre des matières premières très pures, offrant ainsi un verre très transparent, avec une transmission de la lumière très élevée dans les longueurs d’onde visibles, comme on peut le voir sur ce dispositif :
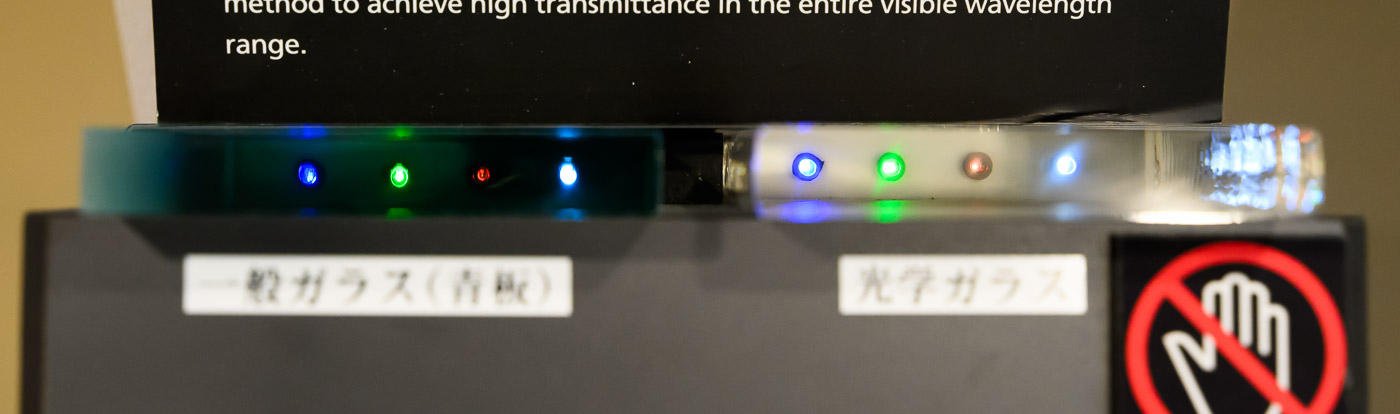
Le verre optique est également conçu pour minimiser les aberrations chromatiques et les distorsions, offrant ainsi une meilleure qualité d’image avec une netteté accrue et des couleurs plus fidèles.
Hikari Glass, le pilier optique de Nikon
La société de fabrication de verre optique, désormais filiale à 100% de Nikon Corporation, a été créée en 1962 sous le nom de Hikari Glass à Yotsukaidō, près de l’aéroport Narita, dans la préfecture de Chiba au Japon. En 1975, l’entreprise a commencé ses opérations à Yuzawa, où se trouve l’usine actuelle. En 2004, elle est devenue une filiale de Nikon, renforçant ainsi ses liens avec le géant de l’optique.
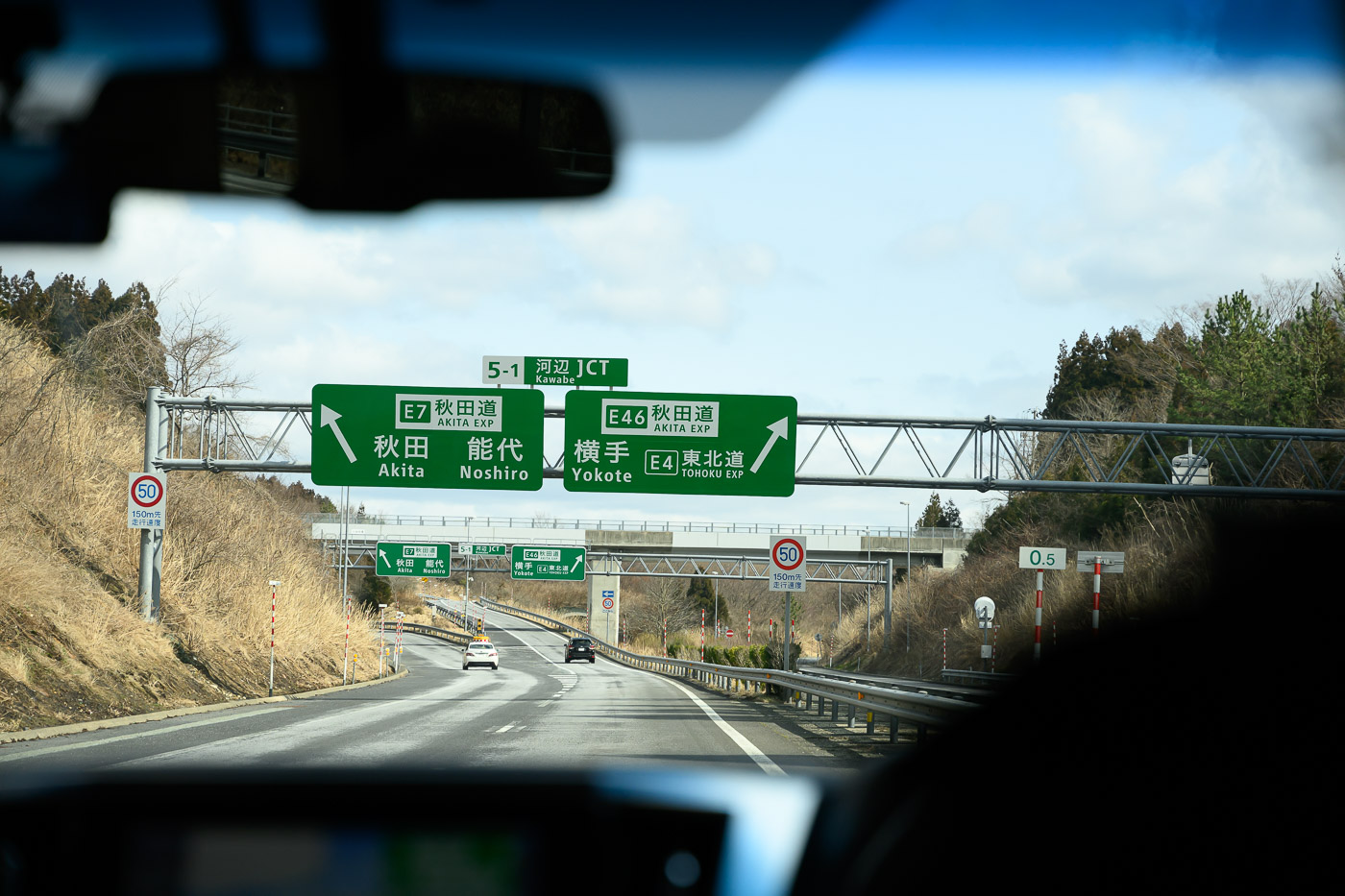
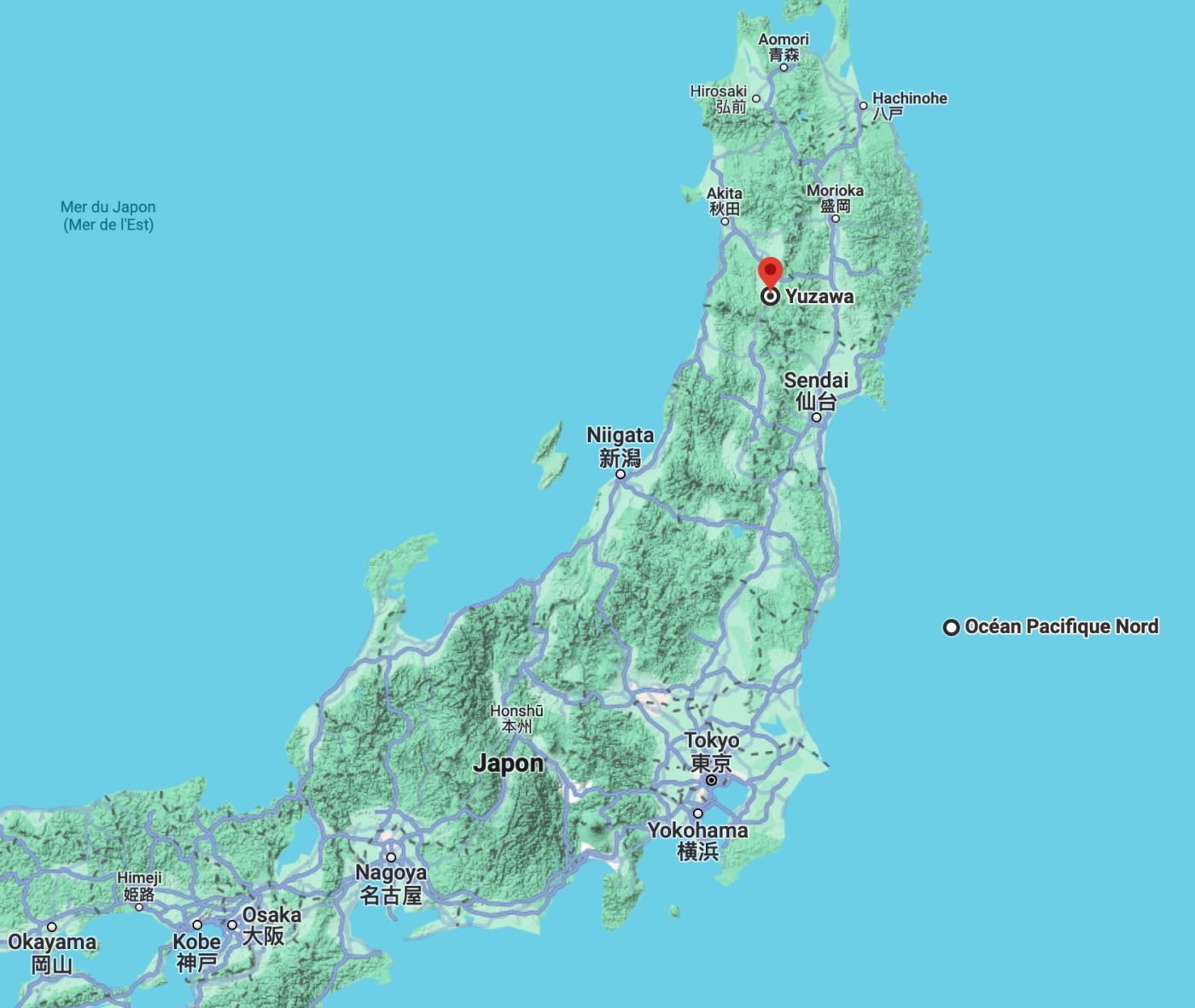
L’usine fabrique aujourd’hui 161 types de verres optiques différents (140 types de lentilles sphériques et 21 types de lentilles asphériques), avec des indices de réfraction variés.
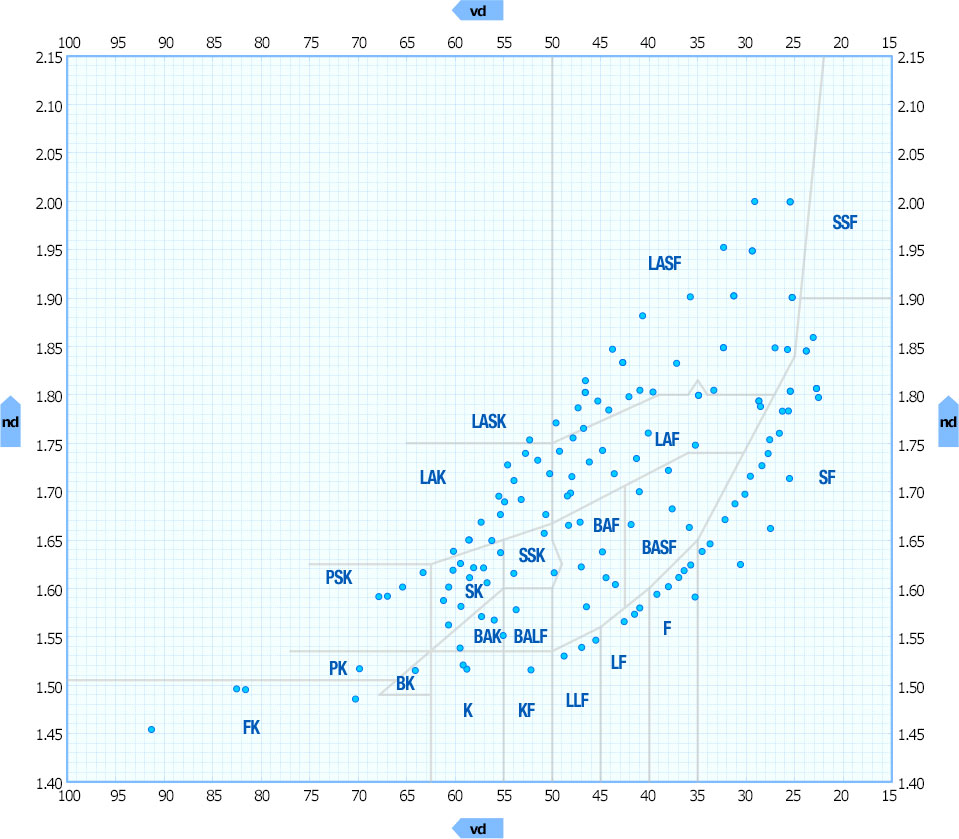
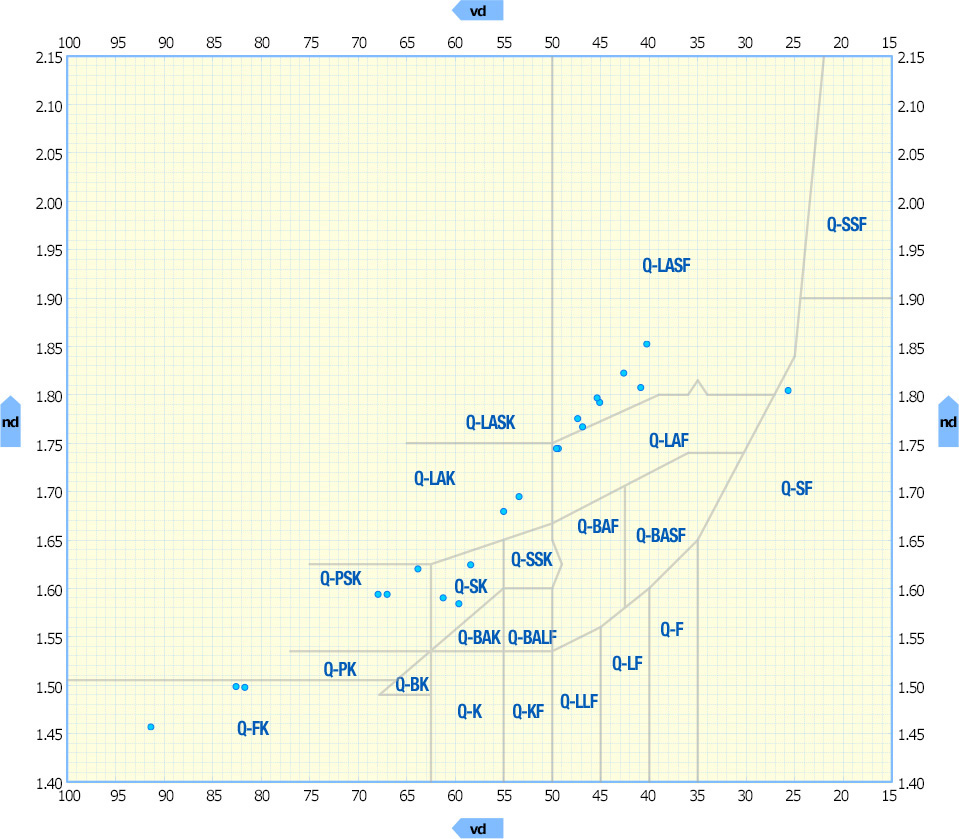
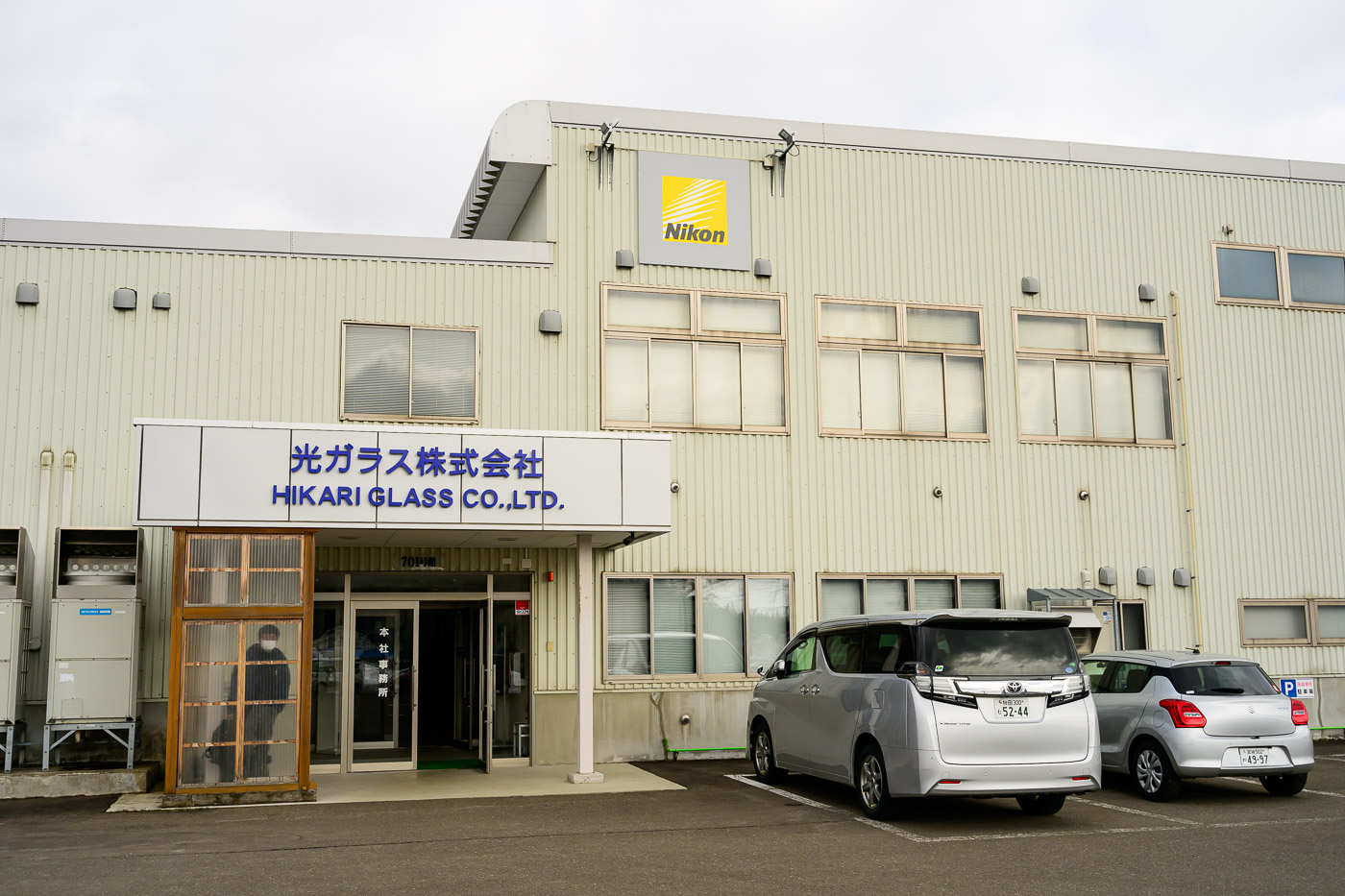
Le siège de Hikari Glass est situé à Minato-ku à Tokyo, et l’entreprise possède aussi une usine de transformation de verre optique à Changzhou, en Chine. La société emploie 350 personnes, dont 180 au Japon, réparties entre Akita et Tokyo.
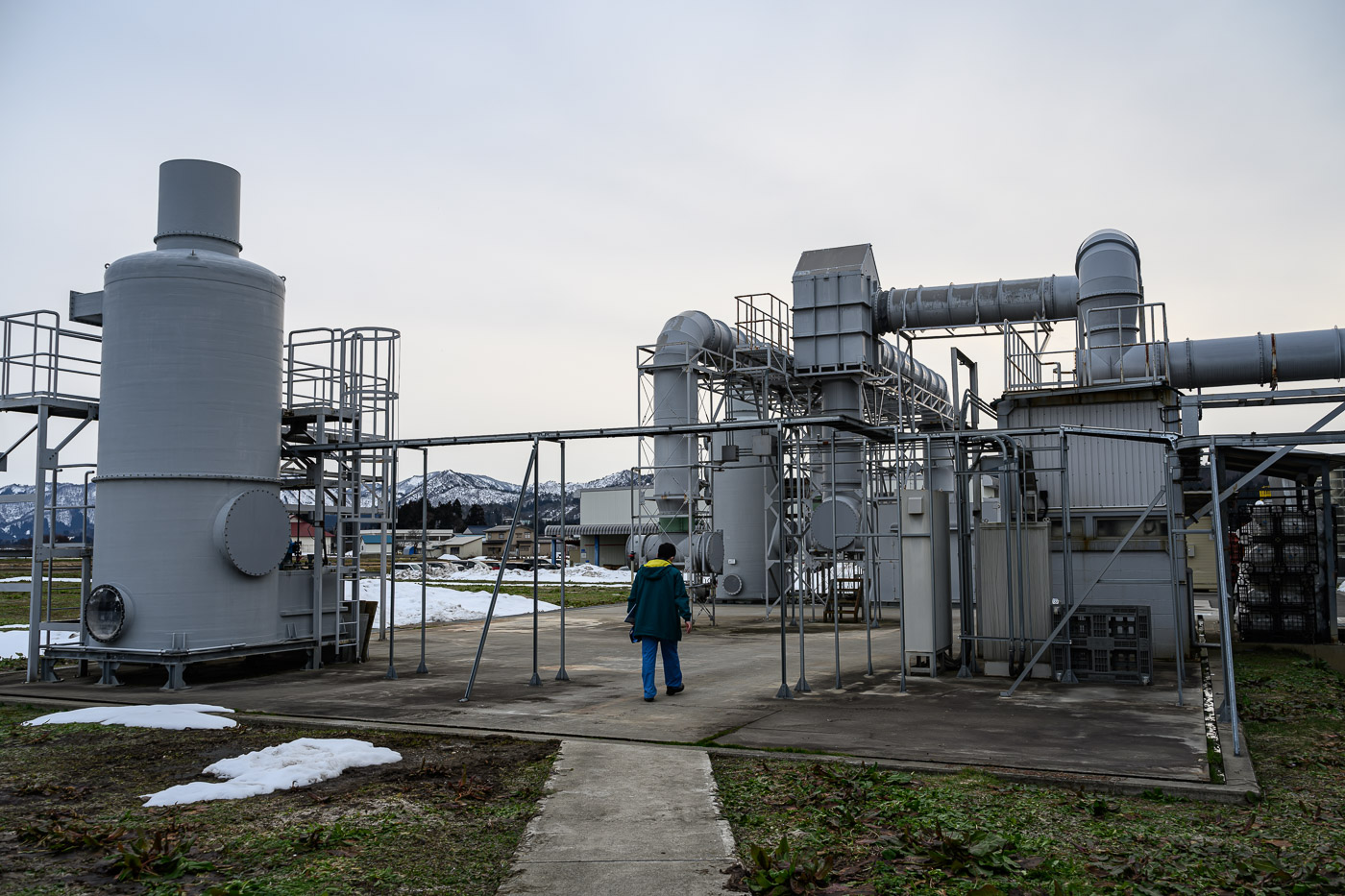
La capacité de production totale de l’usine est de 40 tonnes de verre optique par mois. Dix tonnes sont transformées au Japon, tandis que 30 tonnes sont envoyées à l’usine de Changzhou en Chine. À Hikari, 200 000 lentilles sont façonnées par mois, avant d’être expédiées en grande partie aux usines de Nikon Corporation qui fabriquent les objectifs et différents instruments optiques, comme à l’usine de Tochigi où sont fabriquées les optiques haut de gamme Nikkor Z.
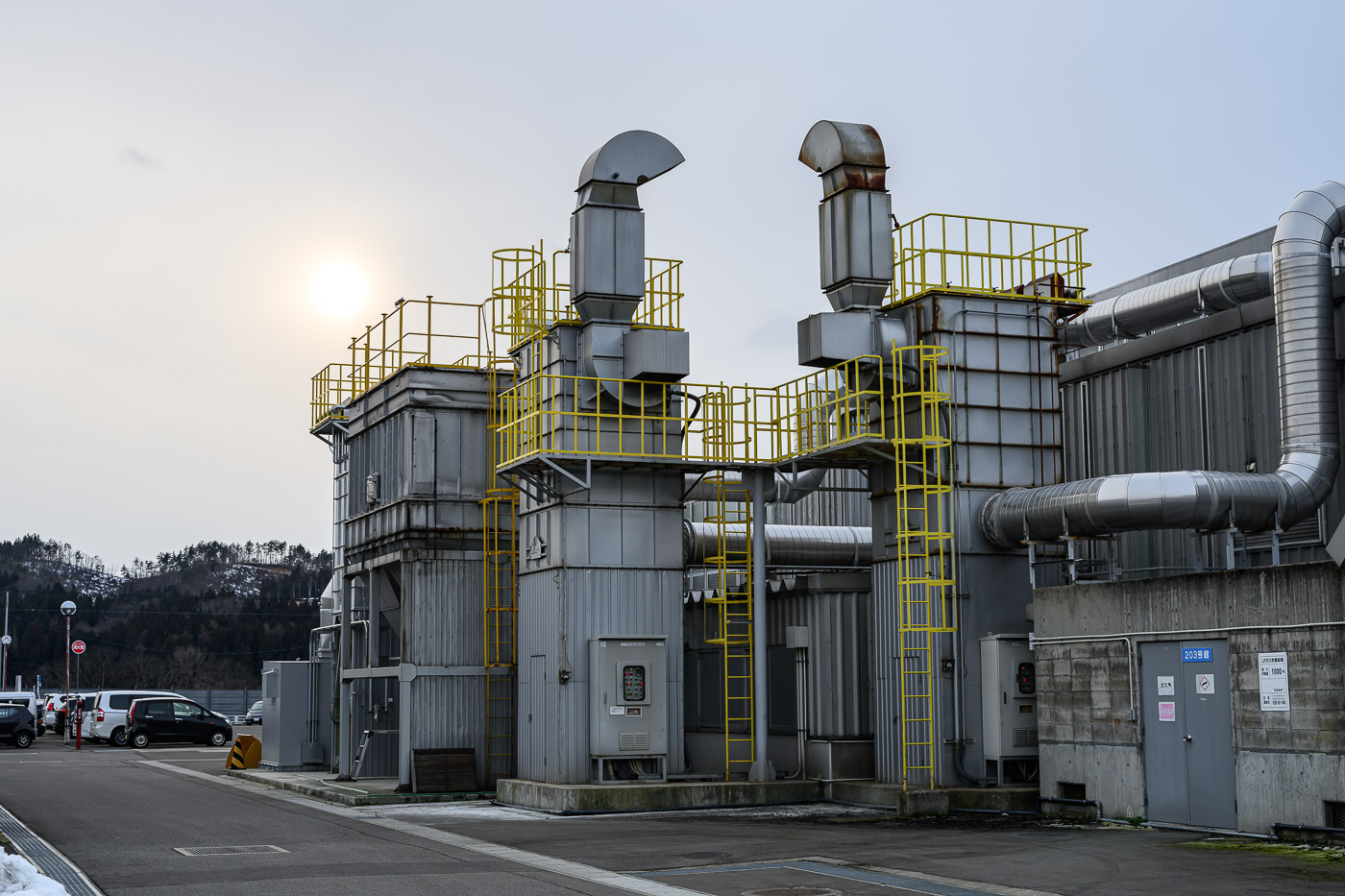
Ses principaux clients incluent des sociétés du groupe Nikon, ainsi qu’AGC Micro Glass, Fujifilm Optics, Konica Minolta et Ricoh Industrial Solutions. Peu d’entreprises sont encore capables aujourd’hui de fabriquer du verre optique de qualité. D’ailleurs, la majorité des outils de production sont conçus, fabriqués et réparés par Hikari Glass.
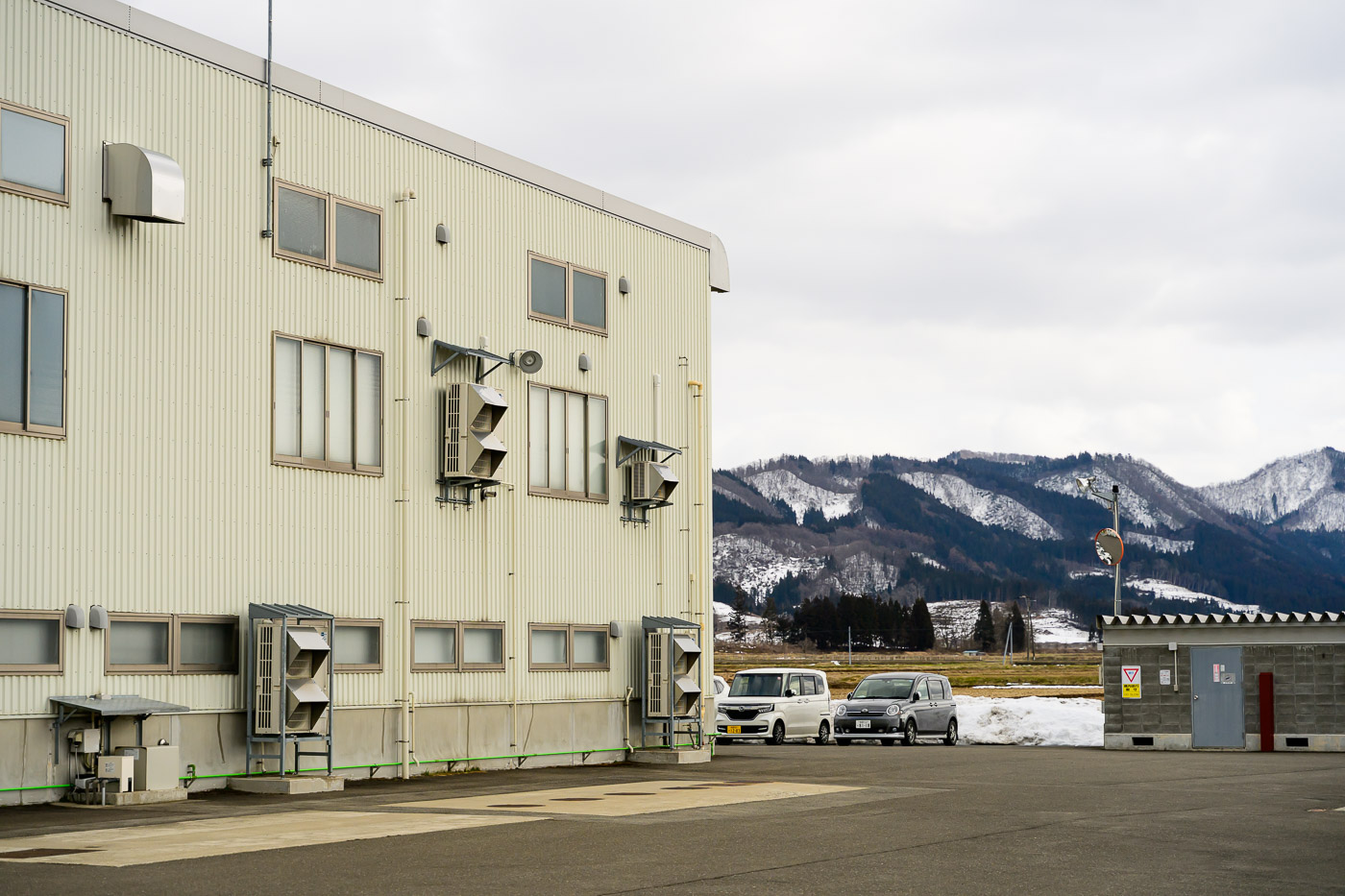
L’usine est située dans la région d’Akita, au cœur des rizières. Le choix du lieu s’est fait suite à des échanges entre un employé et le président, qui voulait contribuer à l’emploi pour les habitants de la région. Un espace était disponible à Yuzawa et l’implantation de l’usine permettait de fournir des emplois aux hommes pendant l’hiver, période durant laquelle l’activité agricole est réduite. Les habitants de la région sont également décrits comme très dévoués et calmes, une caractéristique clé pour la fabrication de verre. D’autres entreprises comme TDK et Epson sont également localisées dans la région.
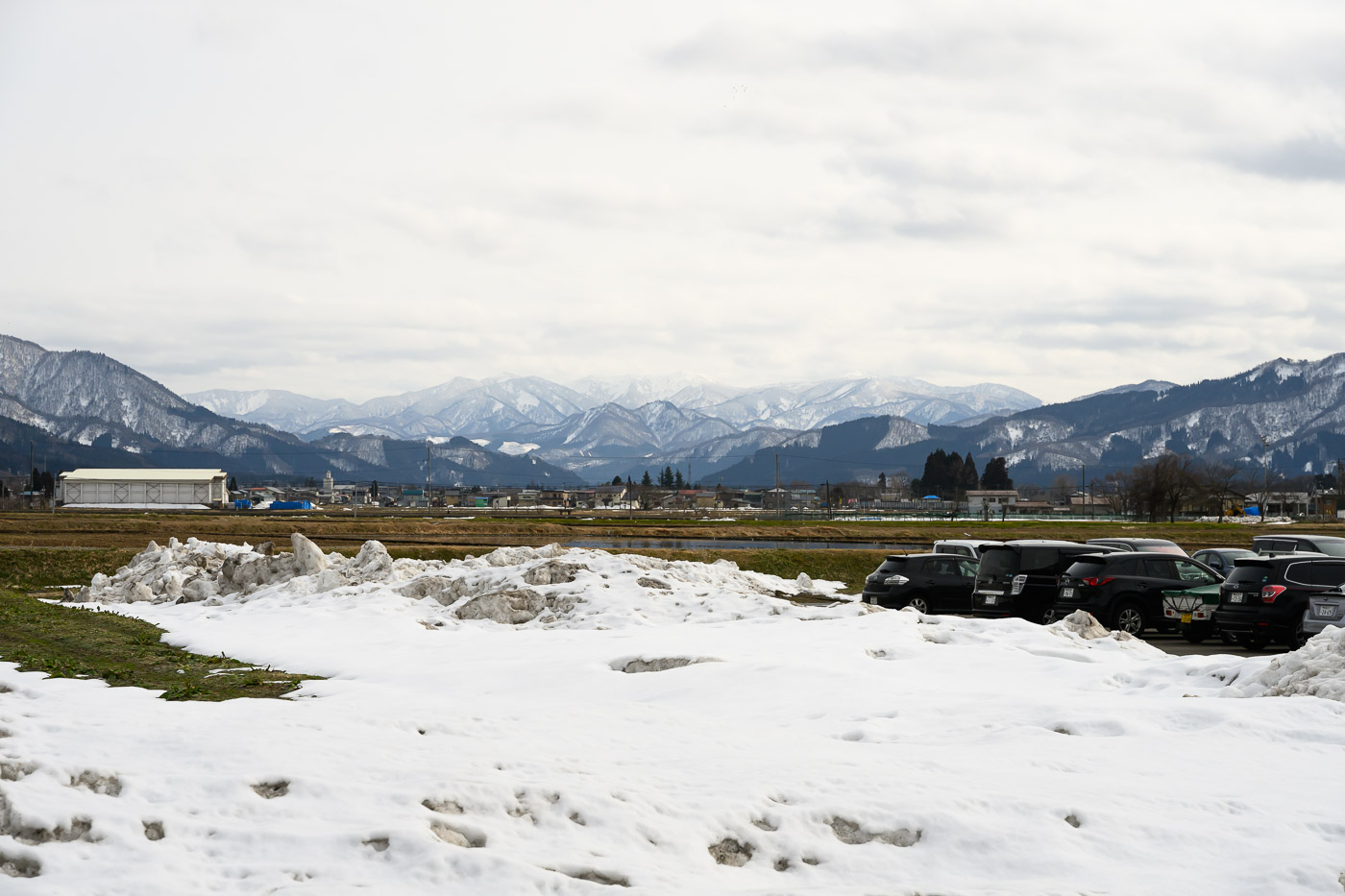
Avant d’obtenir une lentille de verre qui ressemble à peu près à la lentille finale qui sera polie, traitée puis ajustée dans un objectif, le verre passe par de nombreux états et étapes, que nous avons eu l’occasion de suivre lors de notre visite de l’usine Hikari Glass.
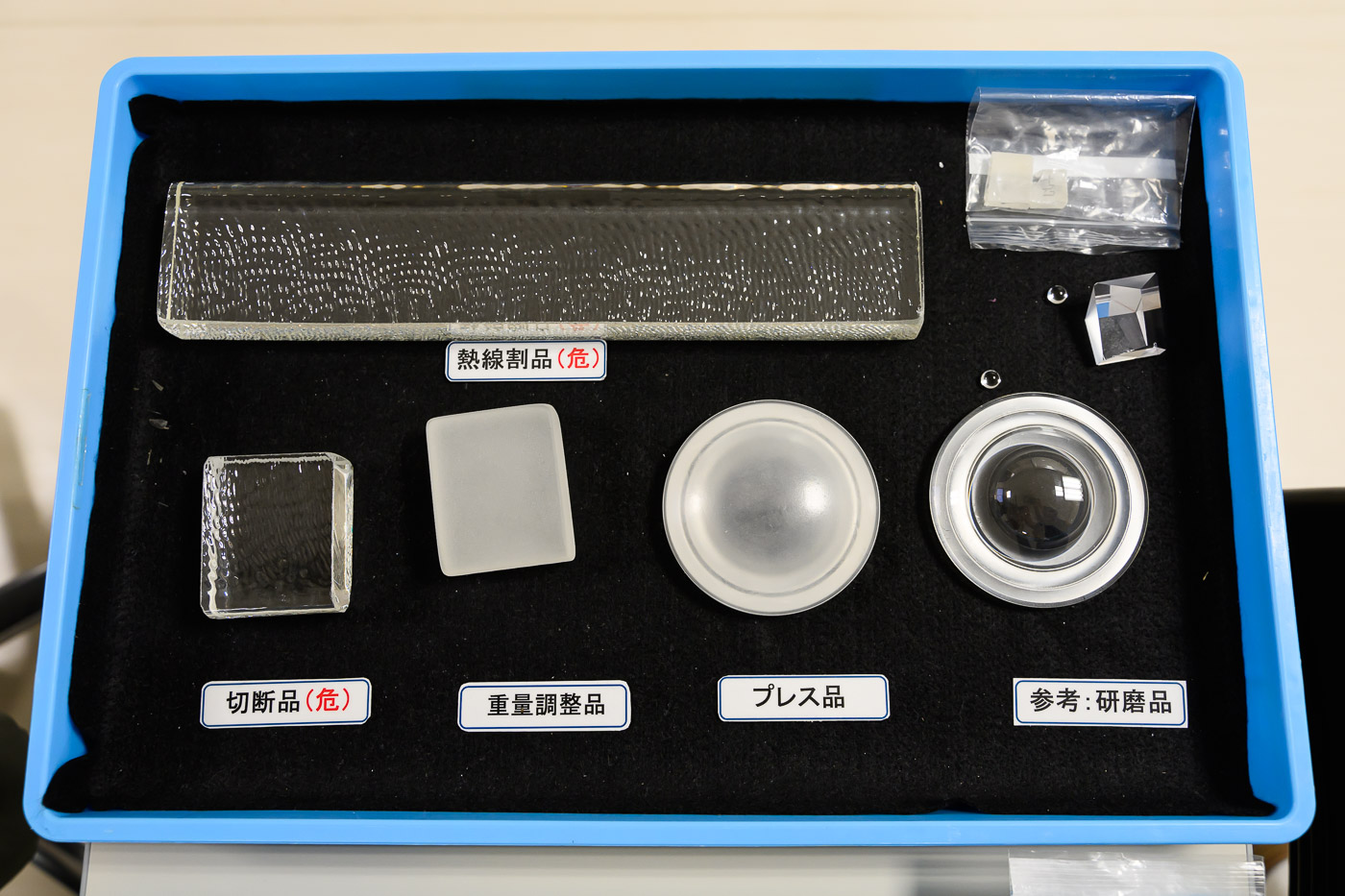
Mélange et fusions : les premières étapes
À l’origine, il y a… la poudre. Dans l’usine Hikari, Nikon dispose de 100 matières premières différentes, qui sont importées au Japon depuis un peu partout dans le monde.
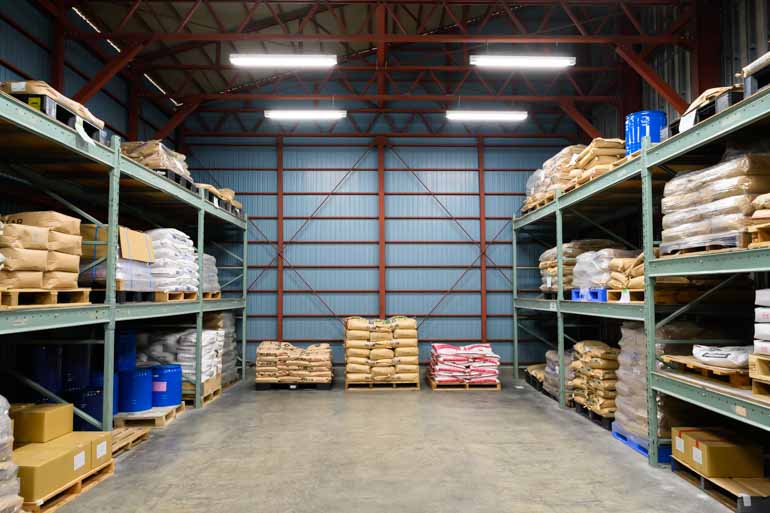
Selon le type de verre, on choisit entre 10 et 14 ingrédients, d’un très haut niveau de pureté, afin d’obtenir le verre le plus transparent possible.
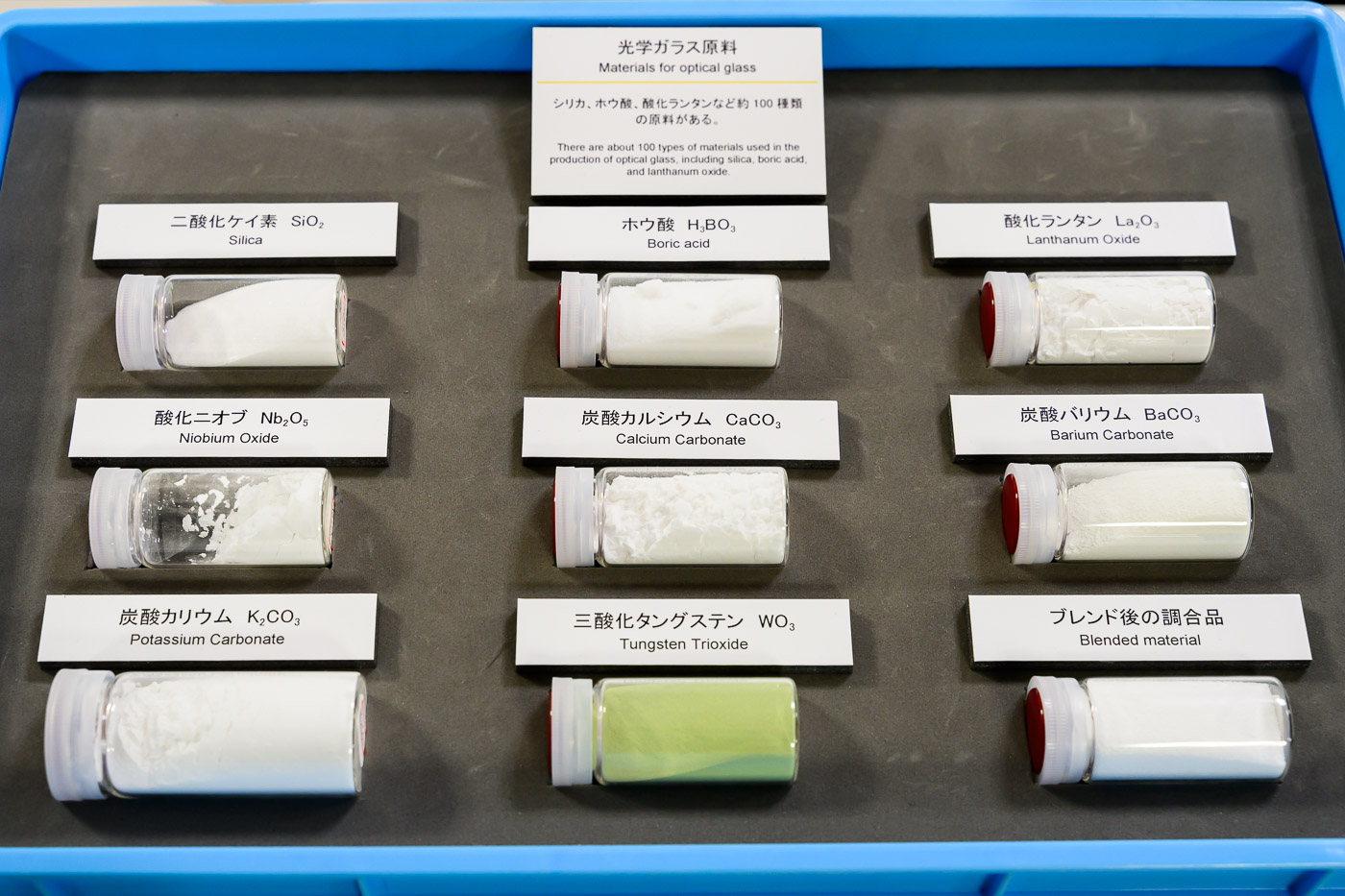
Ces éléments sont mélangés dans une sorte de grosse bétonnière, qui permet de traiter entre 500 et 800 kg de matière. À l’issue de ce premier mélange, on obtient une poudre blanche.
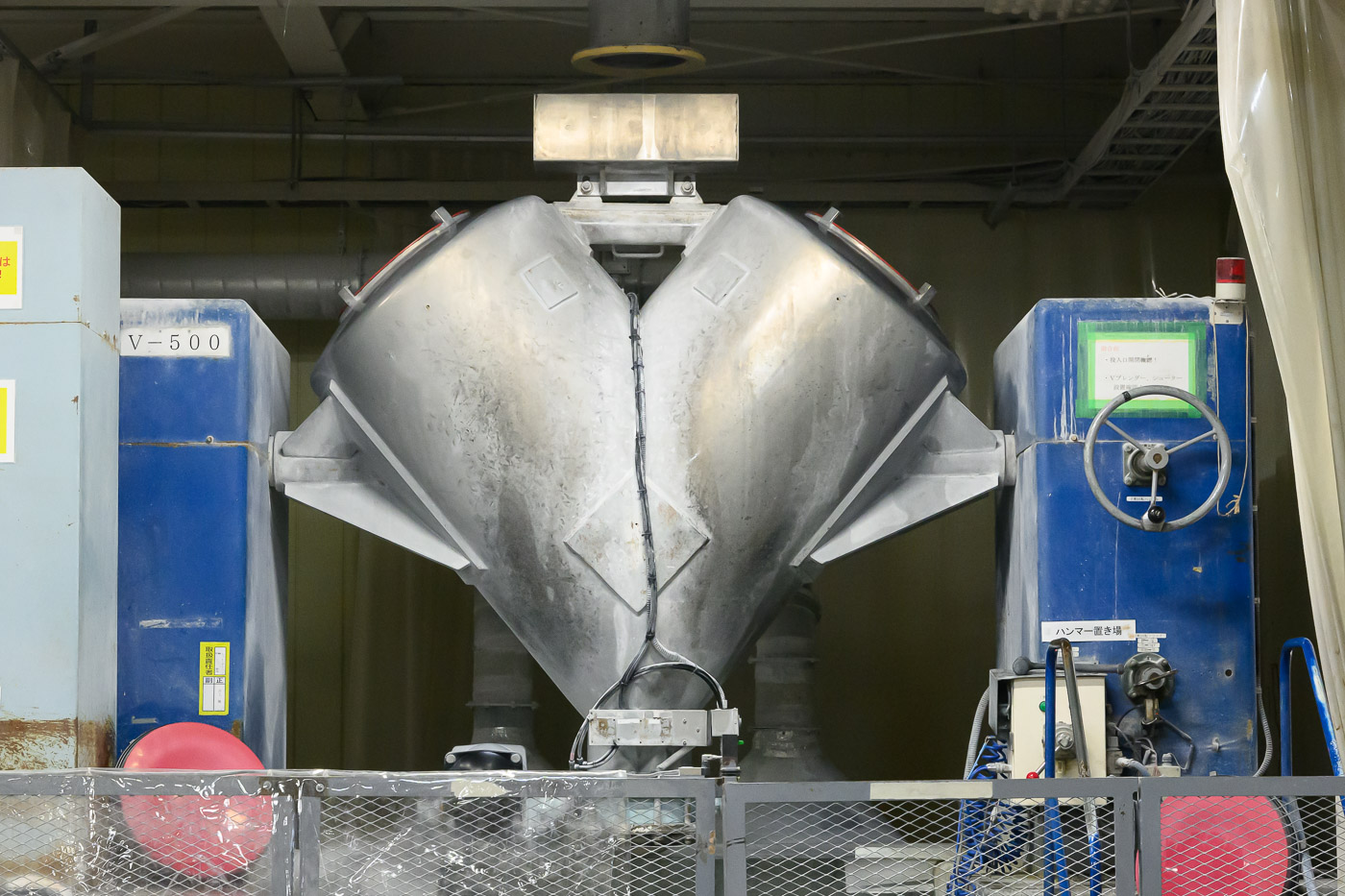

Cette poudre va passer ensuite par une étape de pré-fusion : de manière régulière, un bras mécanisé va verser de petites quantités de poudre dans un creuset placé au sein d’un four, afin de faire fondre le mélange.
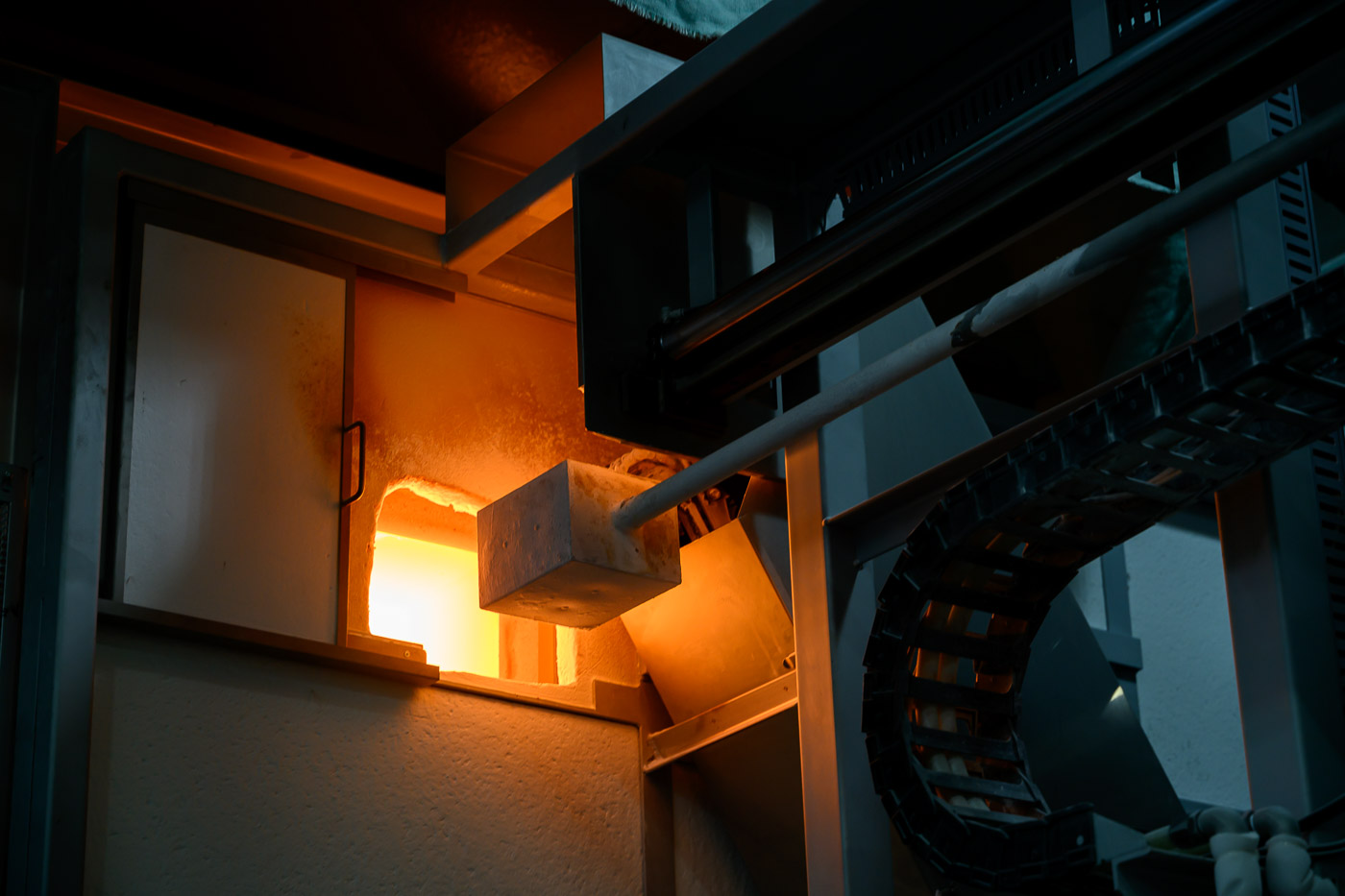
Une fois l’ensemble complètement fondu – comptez plusieurs heures – un réservoir d’eau est placé sous le creuset, puis une ouverture est formée à la base à l’aide d’un chalumeau, laissant s’écouler le verre en fusion.
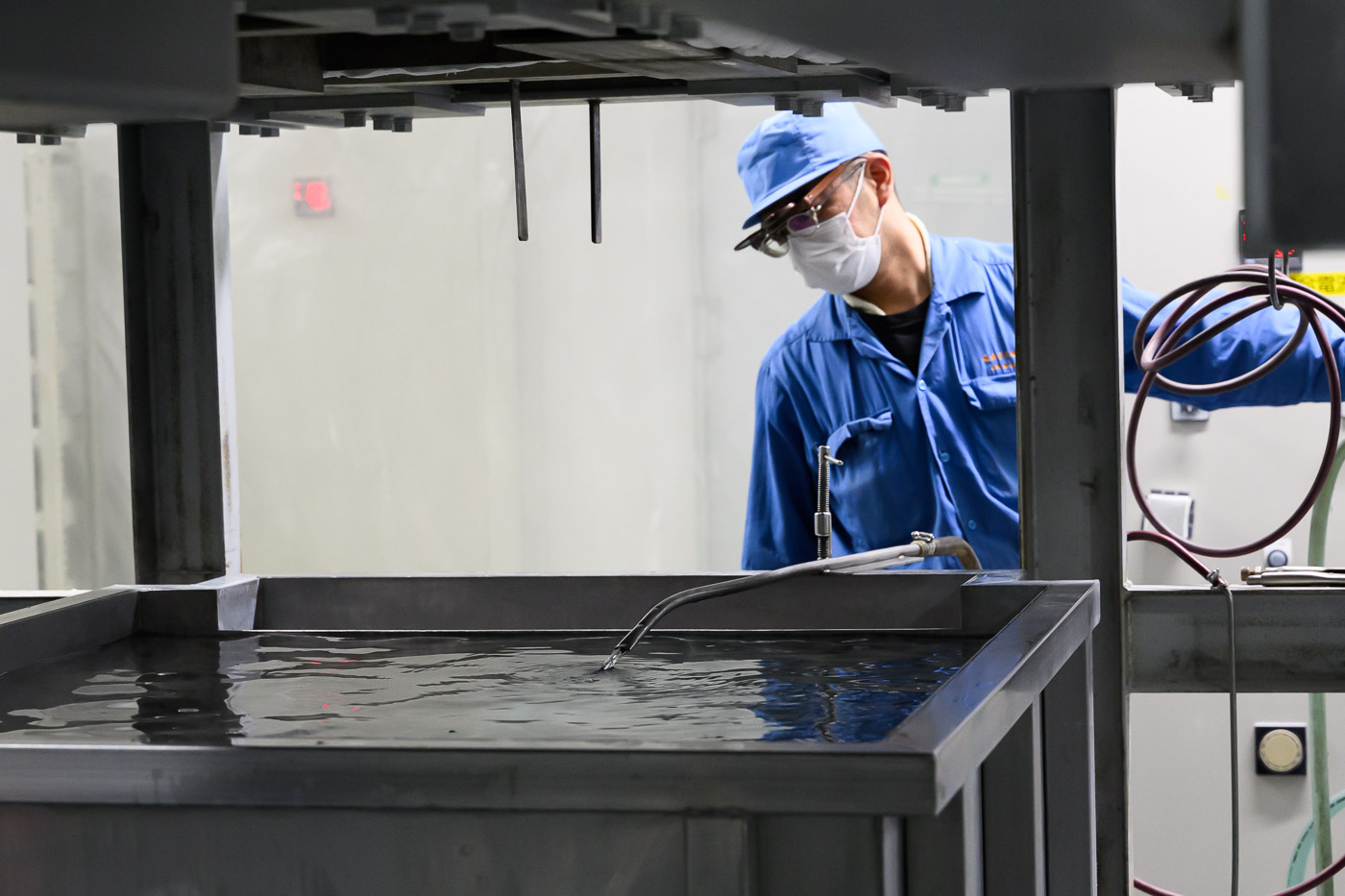
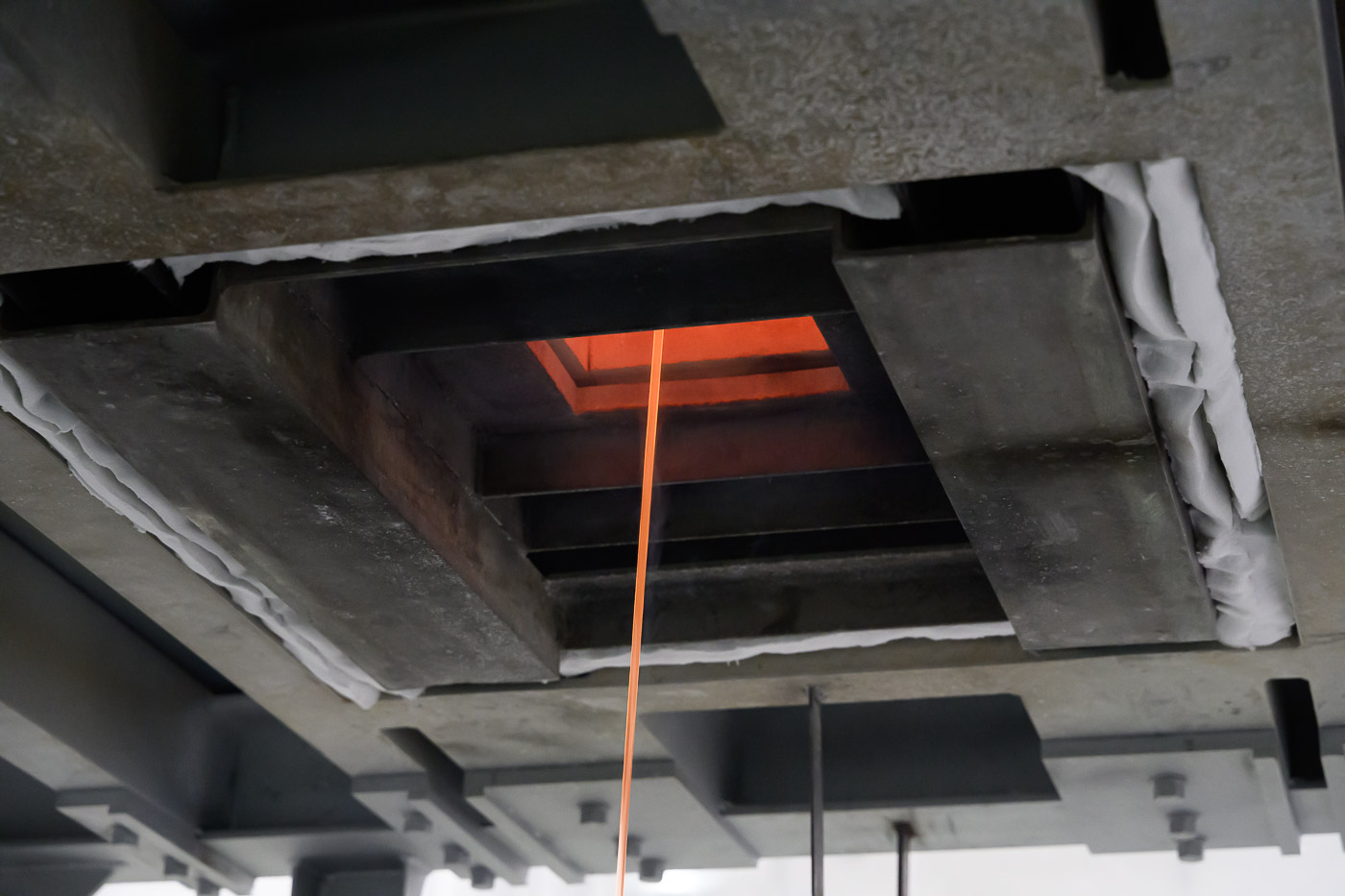
Lors de cette étape, le verre fondu, d’une couleur orangée, s’écoule comme un métal en fusion. La couleur est plus ou moins marquée selon la température du verre. Cette température est fixée par le type de verre fabriqué : plus le verre est fondu à haute température, plus le mélange est incandescent, avec un orange très vif.
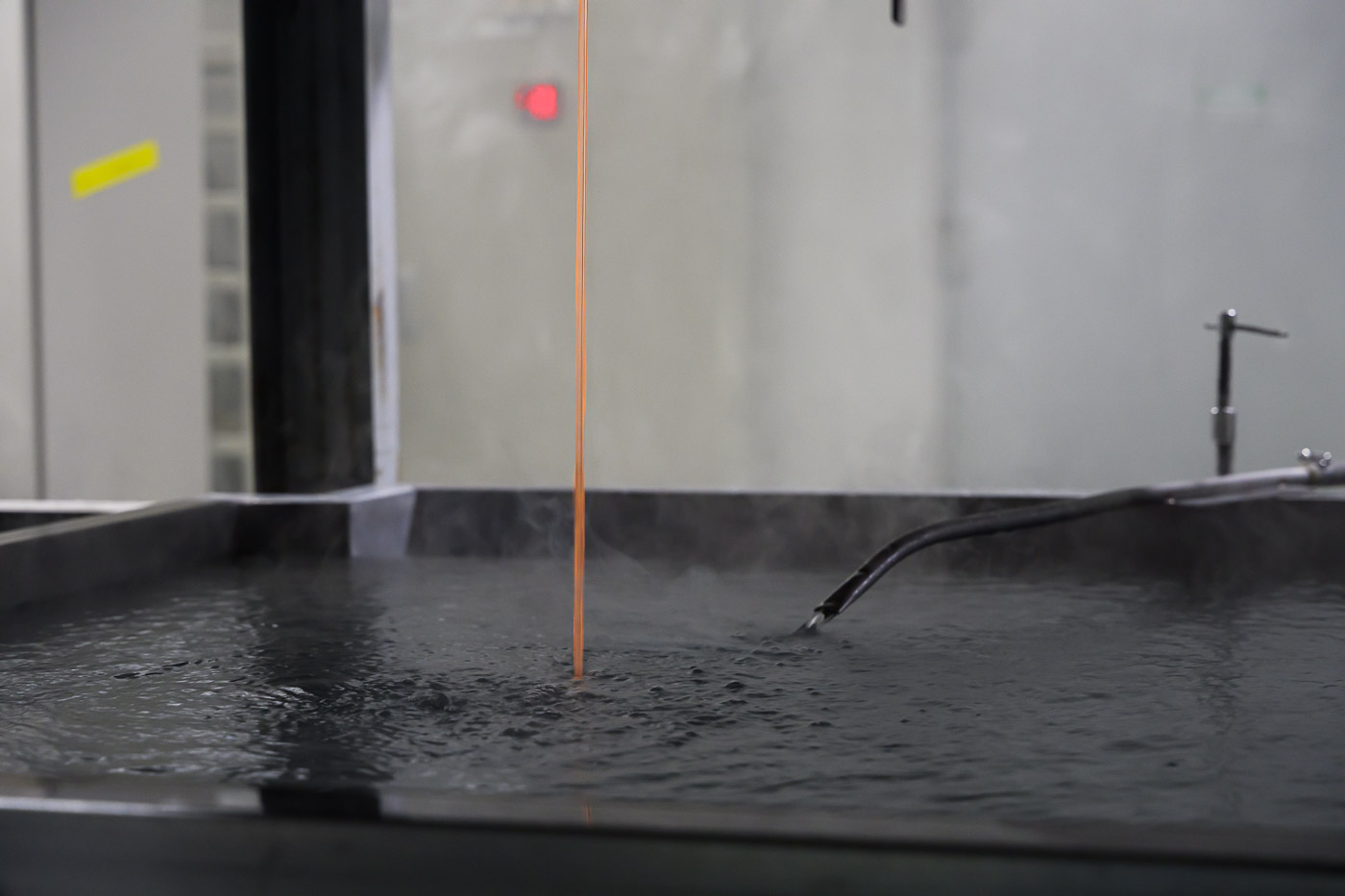
Grâce à un jet d’eau froide dirigé là où le verre en fusion entre en contact avec l’eau, le verre se solidifie et crée de petits cristaux appelés « frit », qui ressemblent à du verre pilé très abrasif.
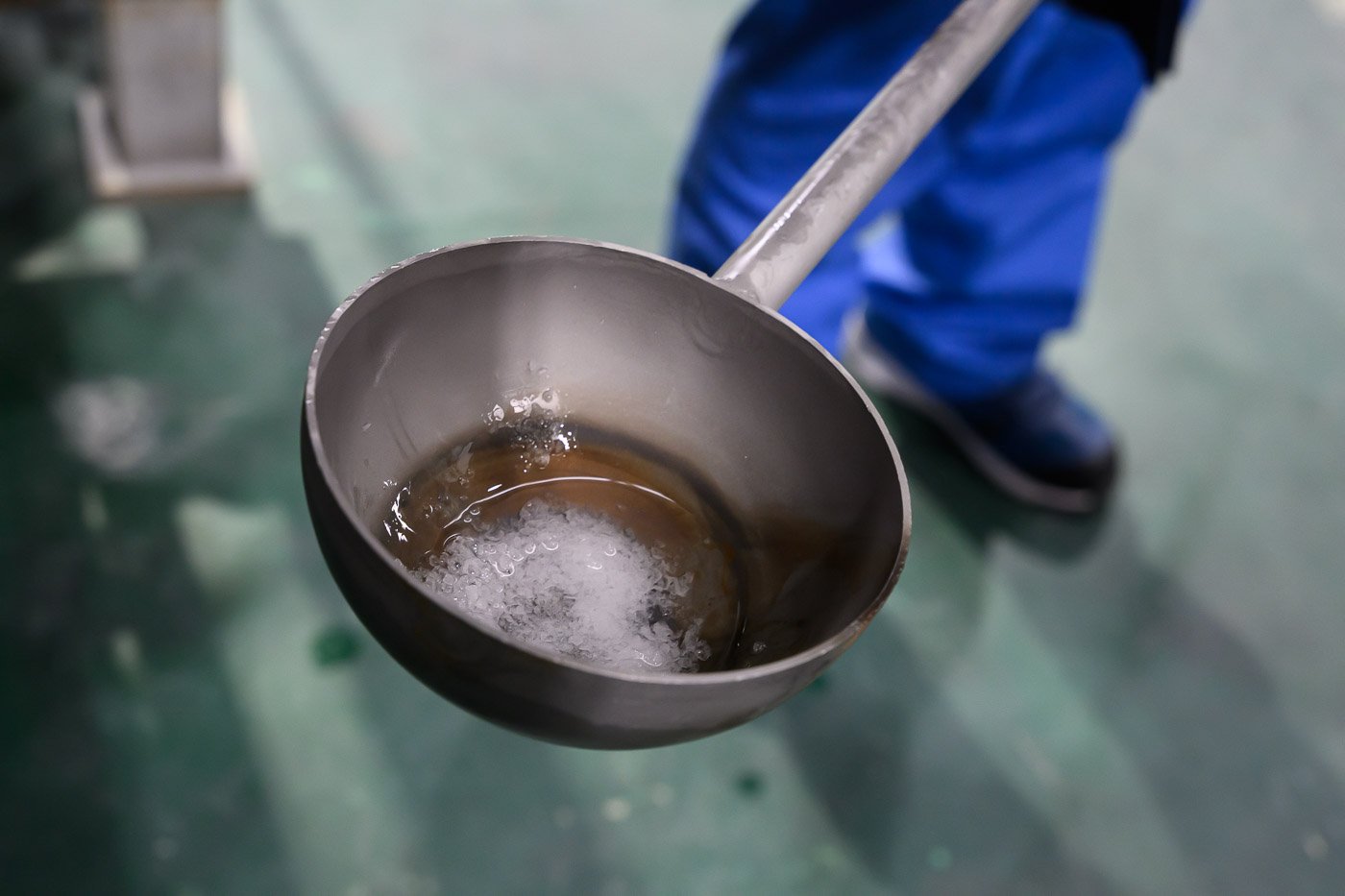
Fusion continue : du verre en barre
L’étape de fusion n’est pas terminée, puisque ce verre va subir une seconde fusion, dite « fusion continue ». Chaque lot de frit est inspecté, afin de mesurer son indice de réfraction. Différents lots sont ensuite mélangés afin d’obtenir le niveau voulu.
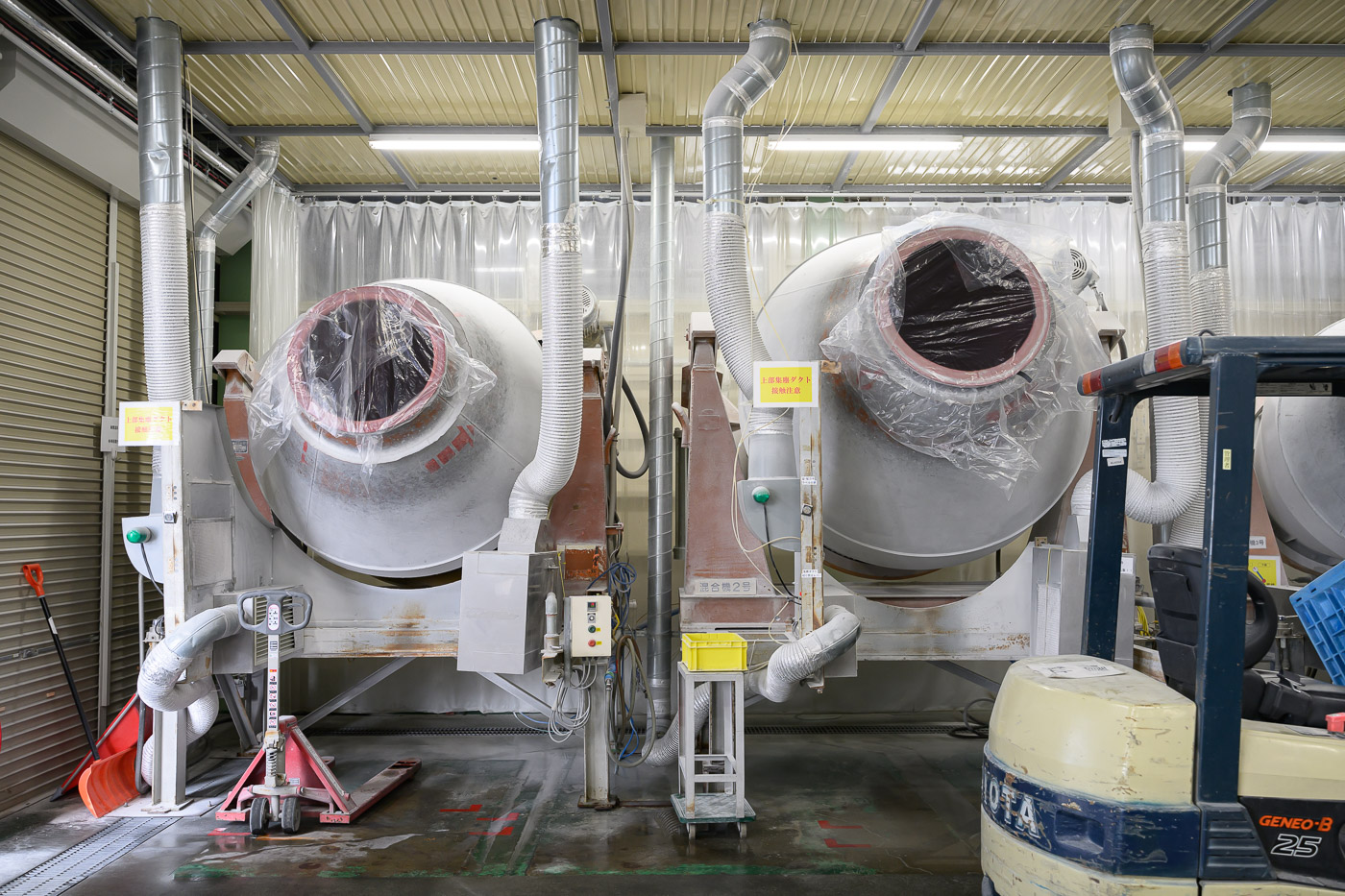
Ensuite, l’ensemble passe par une fusion continue constituée de plusieurs étapes : la chauffe pour faire fondre les particules de verre, l’évacuation des bulles d’air, l’agitation du mélange pour l’homogénéiser.
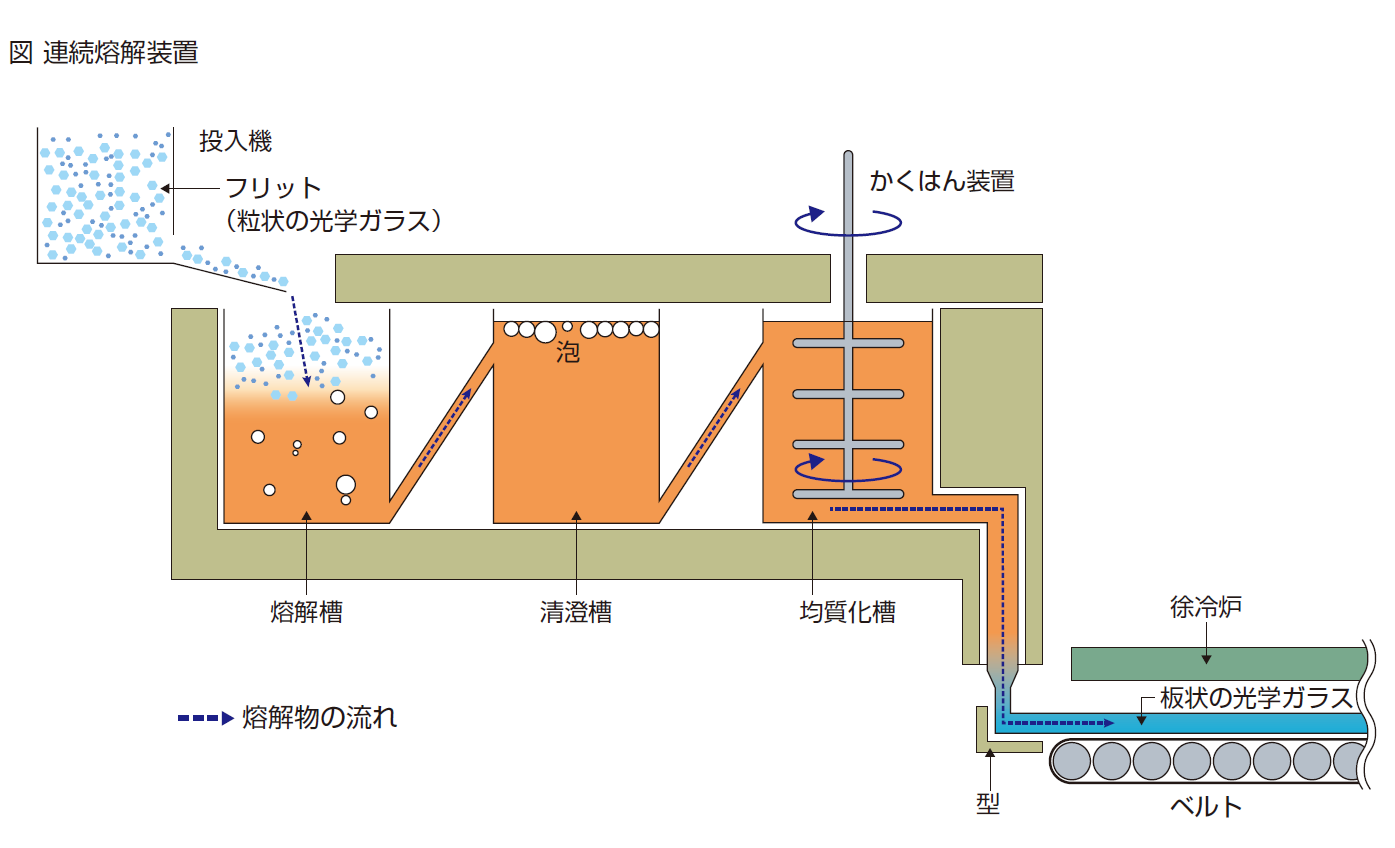
Une fois la température de fusion adéquate atteinte, la dernière étape consiste à pousser le verre en fusion à travers un moule et vers un convoyeur à bande très lent où le verre est refroidi jusqu’à température ambiante.
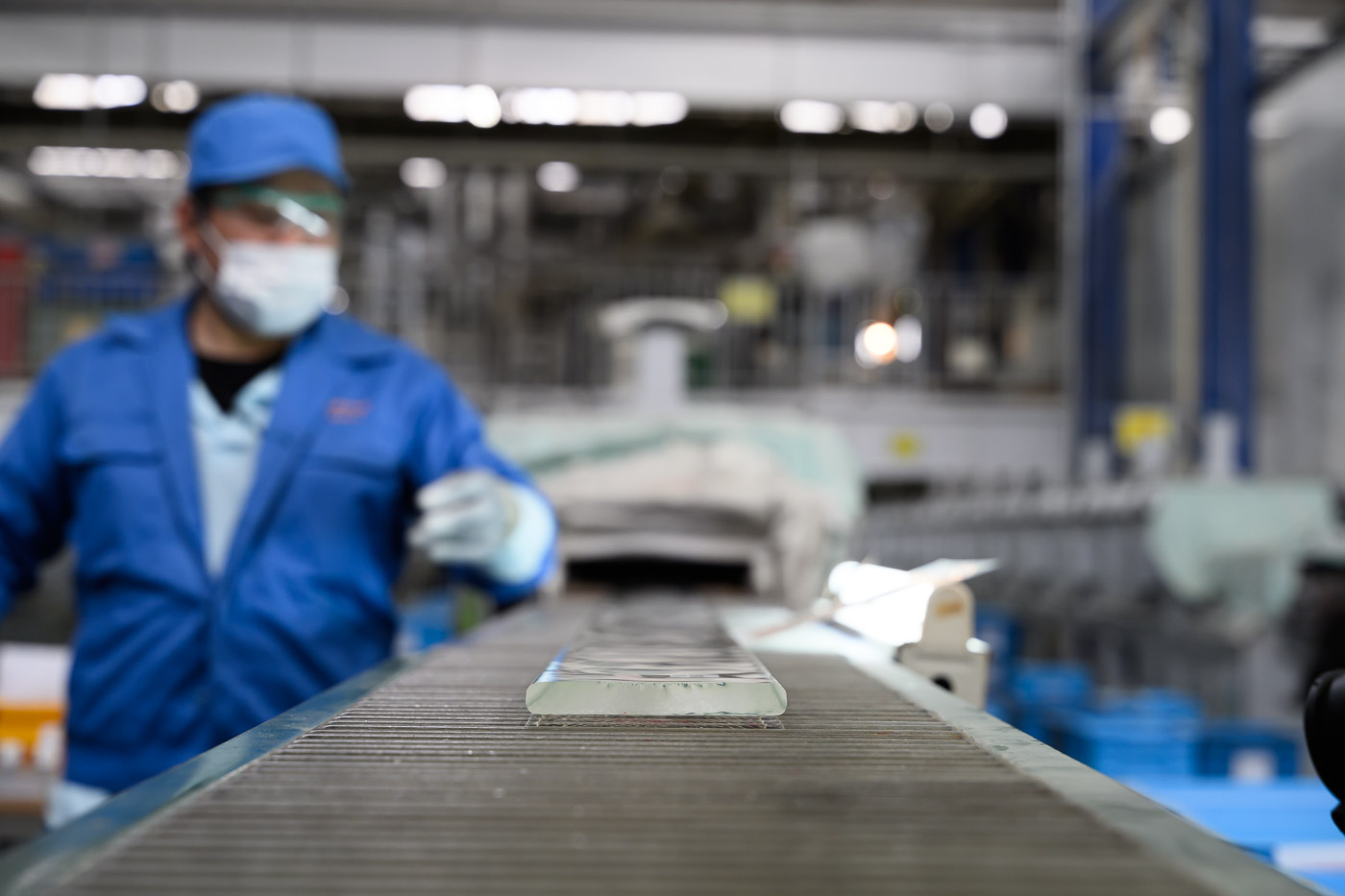
À ce moment-là, le verre se matérialise sous la forme d’une longue barre d’environ 15 cm de large et 3 cm d’épaisseur.
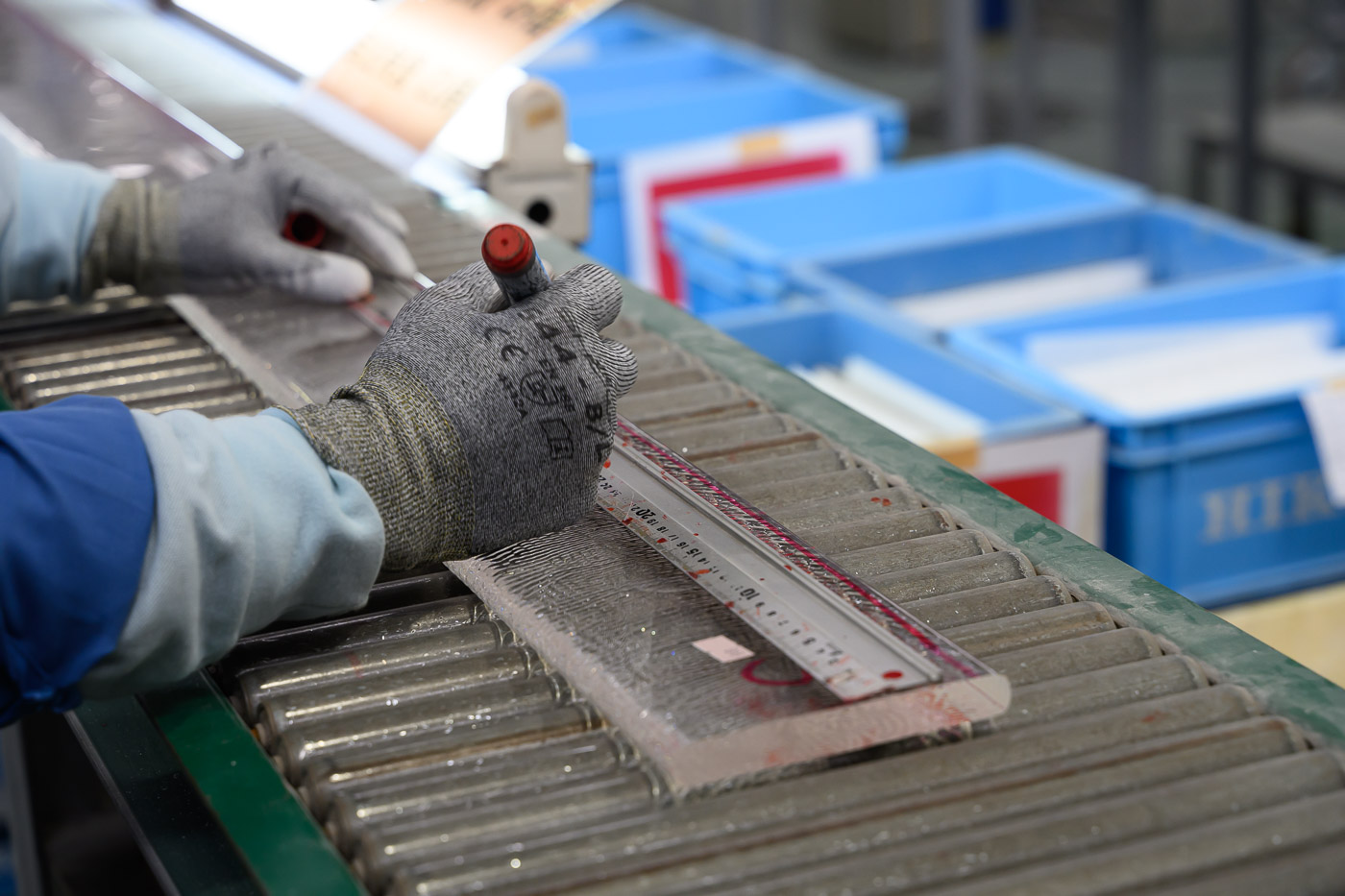
Découpage et calibrage des morceaux de verre
Ces barres de verre vont ensuite subir différentes étapes de découpe, afin de devenir des petits cubes. La première étape est effectuée sur le convoyeur par un employé, afin de découper des morceaux d’environ 50 cm de long, et surtout d’étiqueter le verre pour les prochaines étapes.
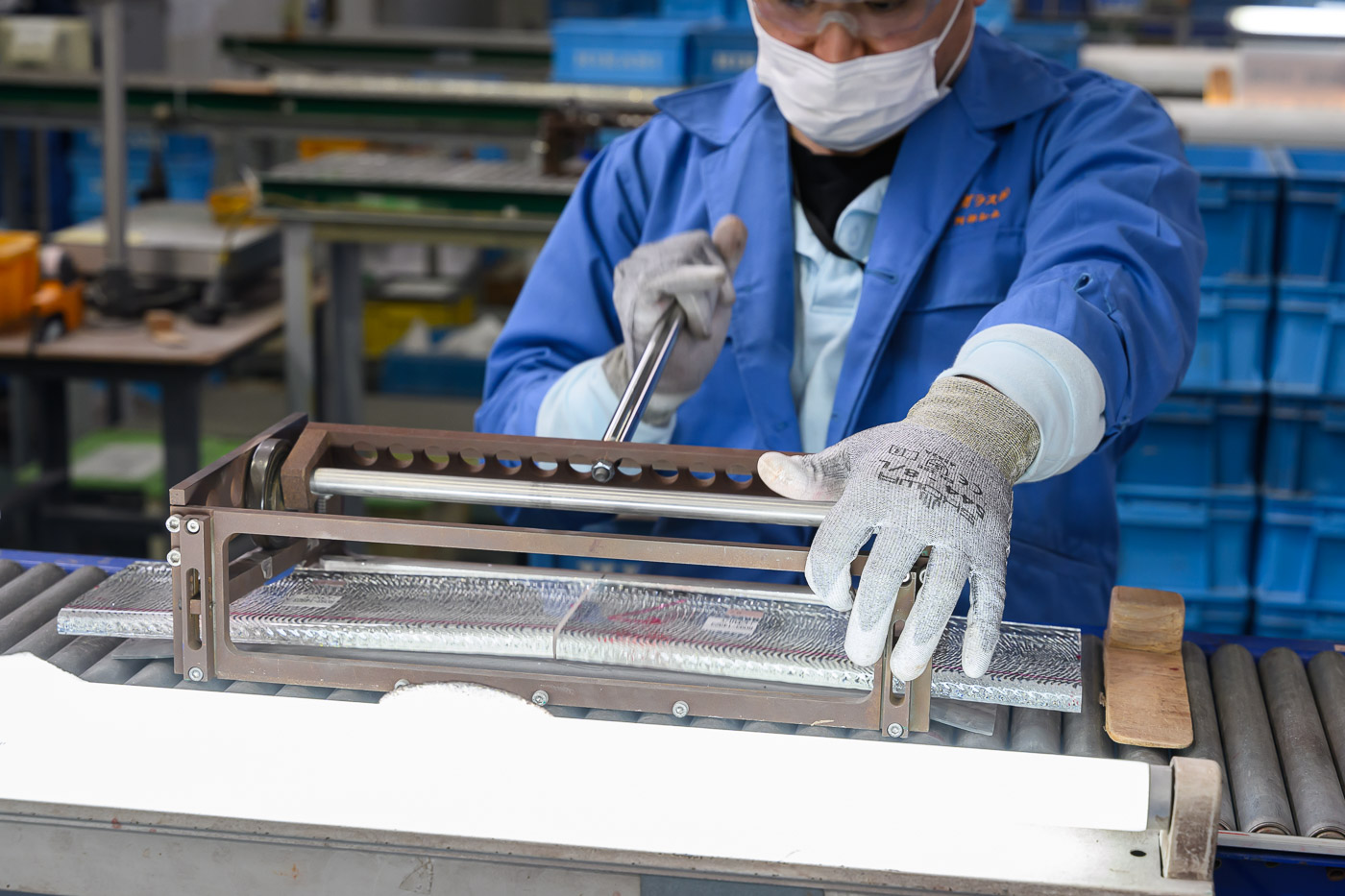

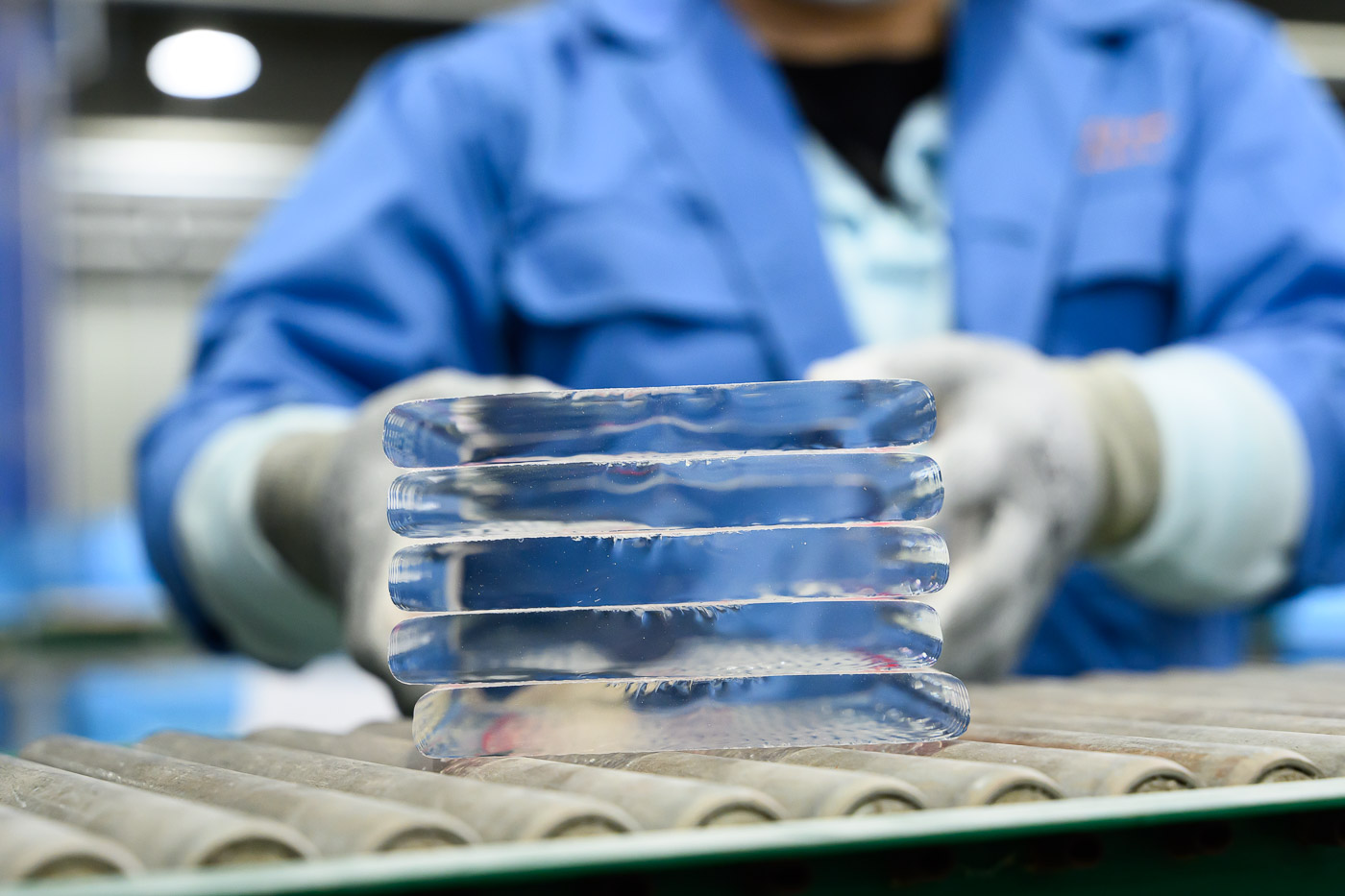
Ensuite, certains échantillons de verre sont inspectés par un employé grâce à une lampe qui permet de projeter une ombre sur un fond blanc. Cela permet de vérifier la transparence parfaite du verre et de détecter le moindre défaut (strie ou bulle) présent au sein du bloc de verre. Des contrôles plus poussés permettent également de s’assurer de l’indice de réfraction et de transmission.
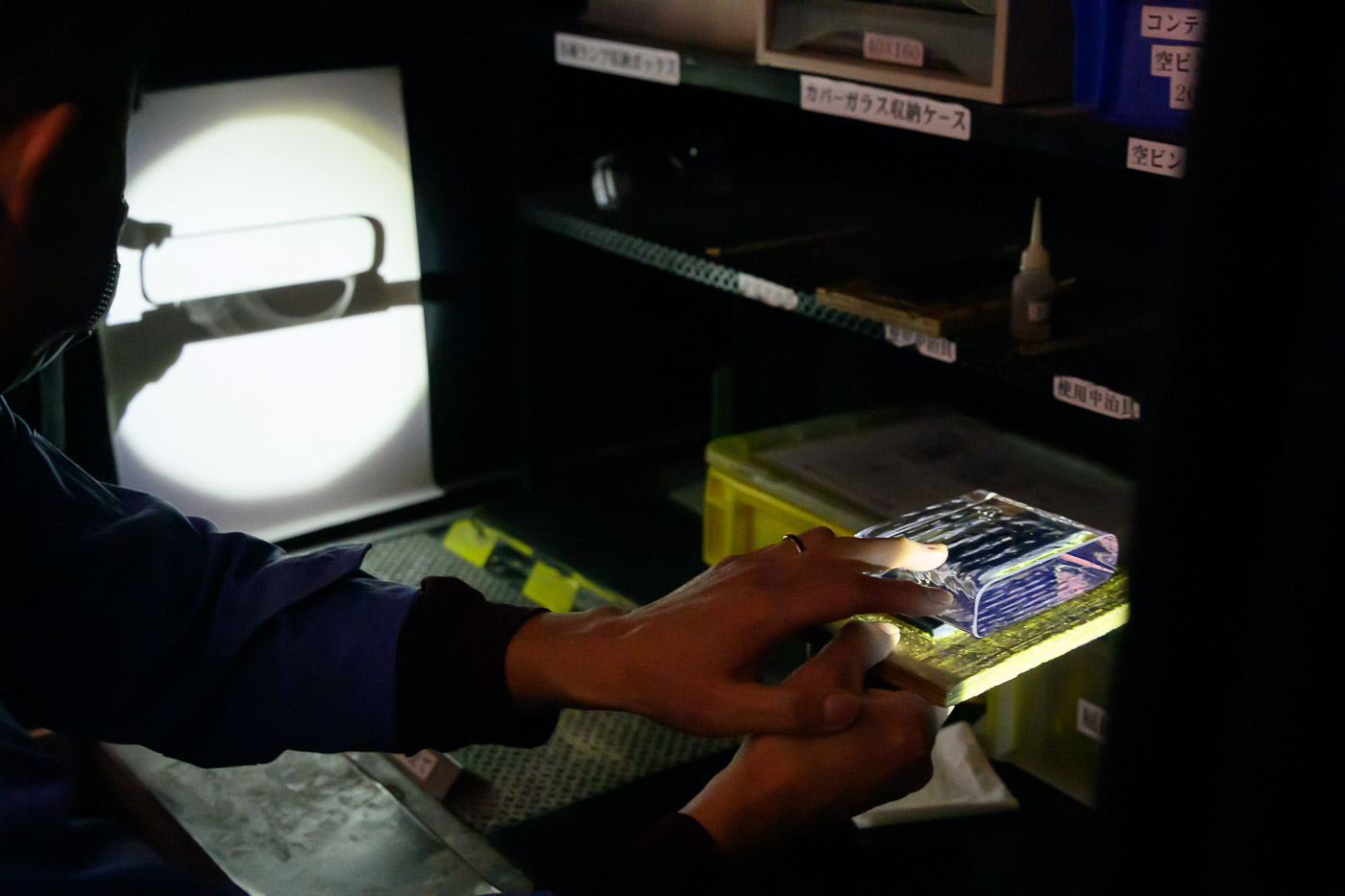
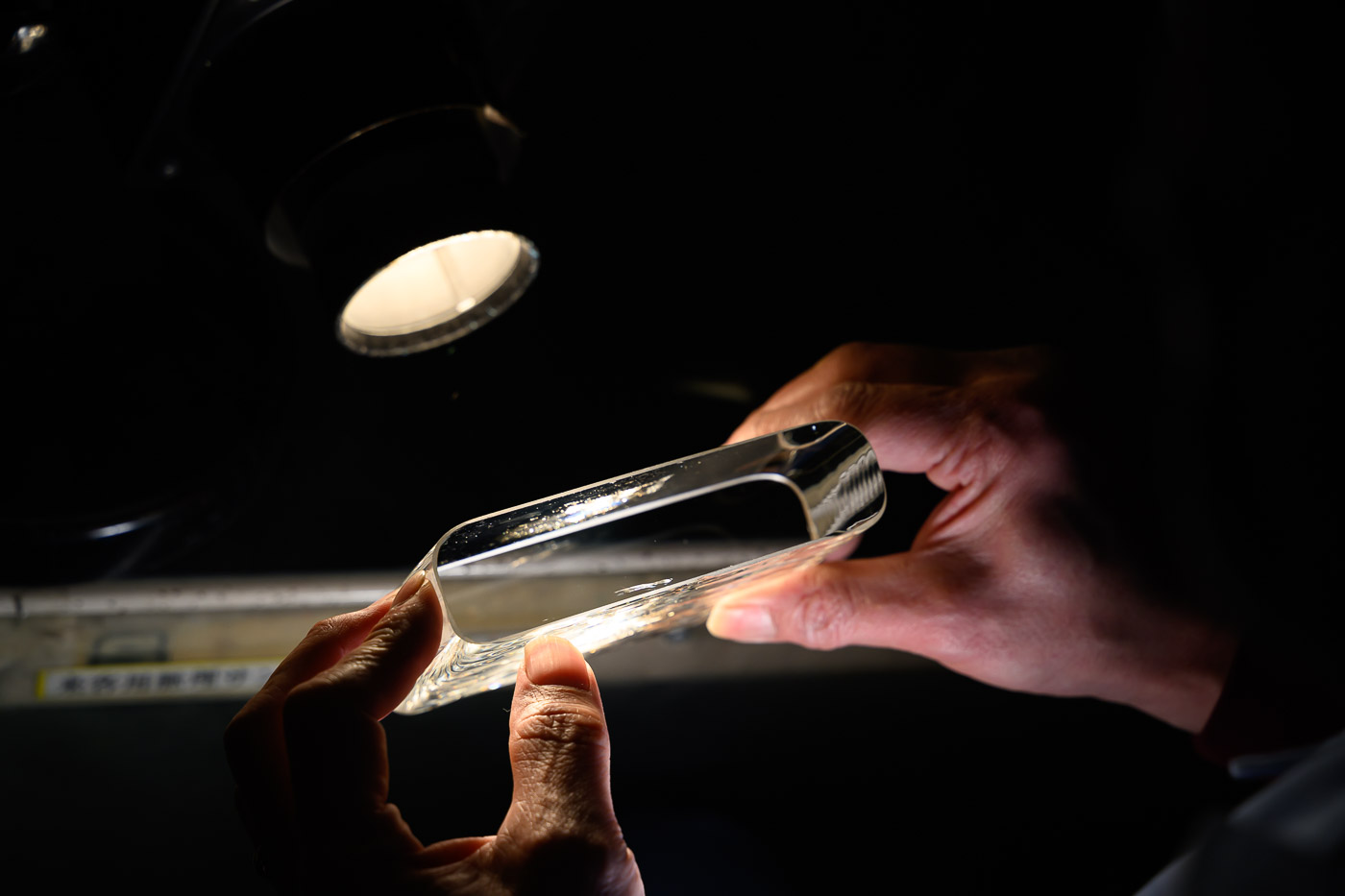
Ces blocs de verre sont ensuite transportés vers un atelier où ils sont découpés, dans la longueur, en bandes plus fines, soit à l’aide d’un fil en métal chauffé à 180° pour couper le verre en deux, soit dans une machine dotée de lames.
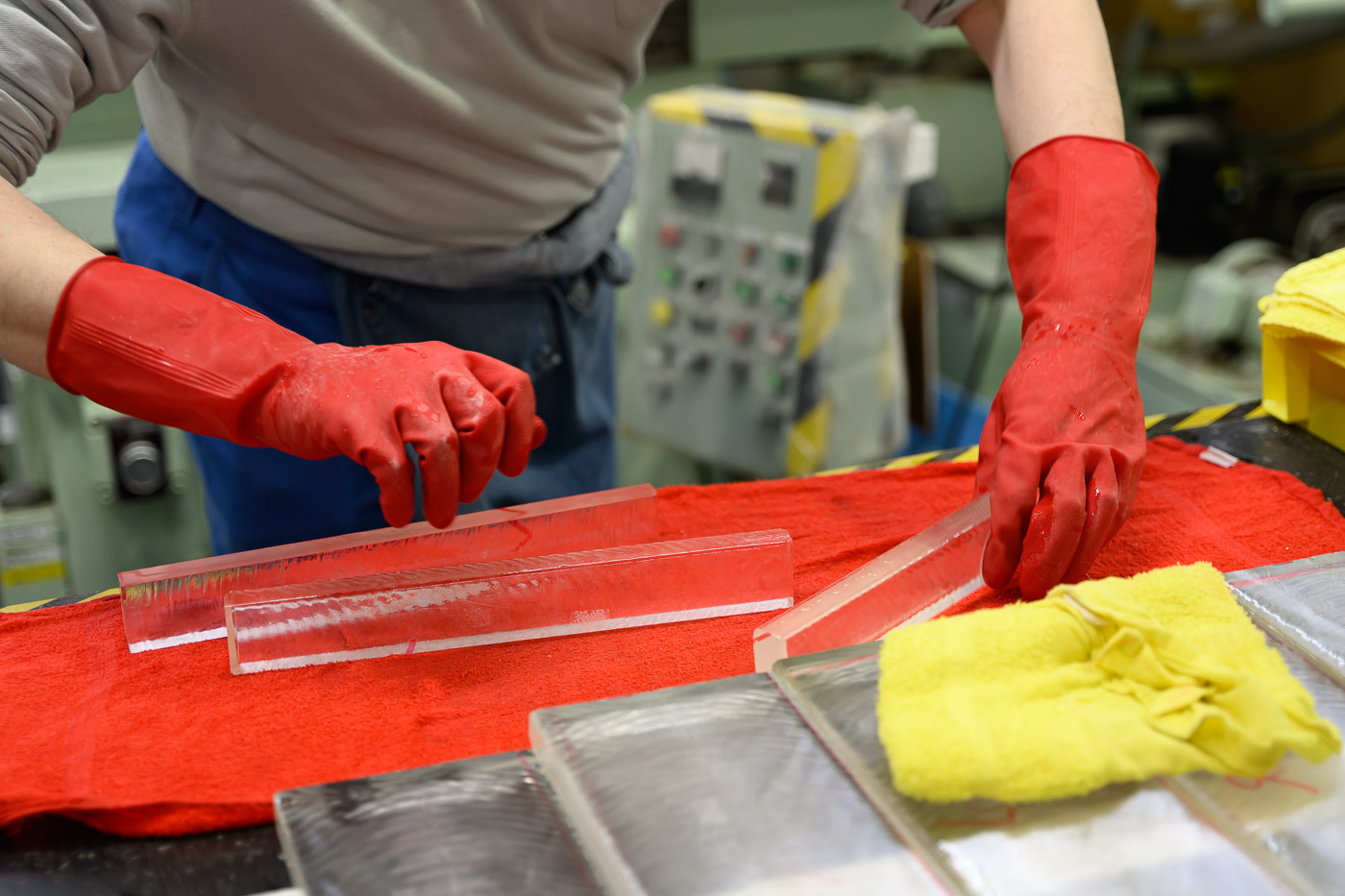
Le verre est découpé à la main en petits cubes puis pesé de manière précise afin de vérifier le poids de chaque bloc.
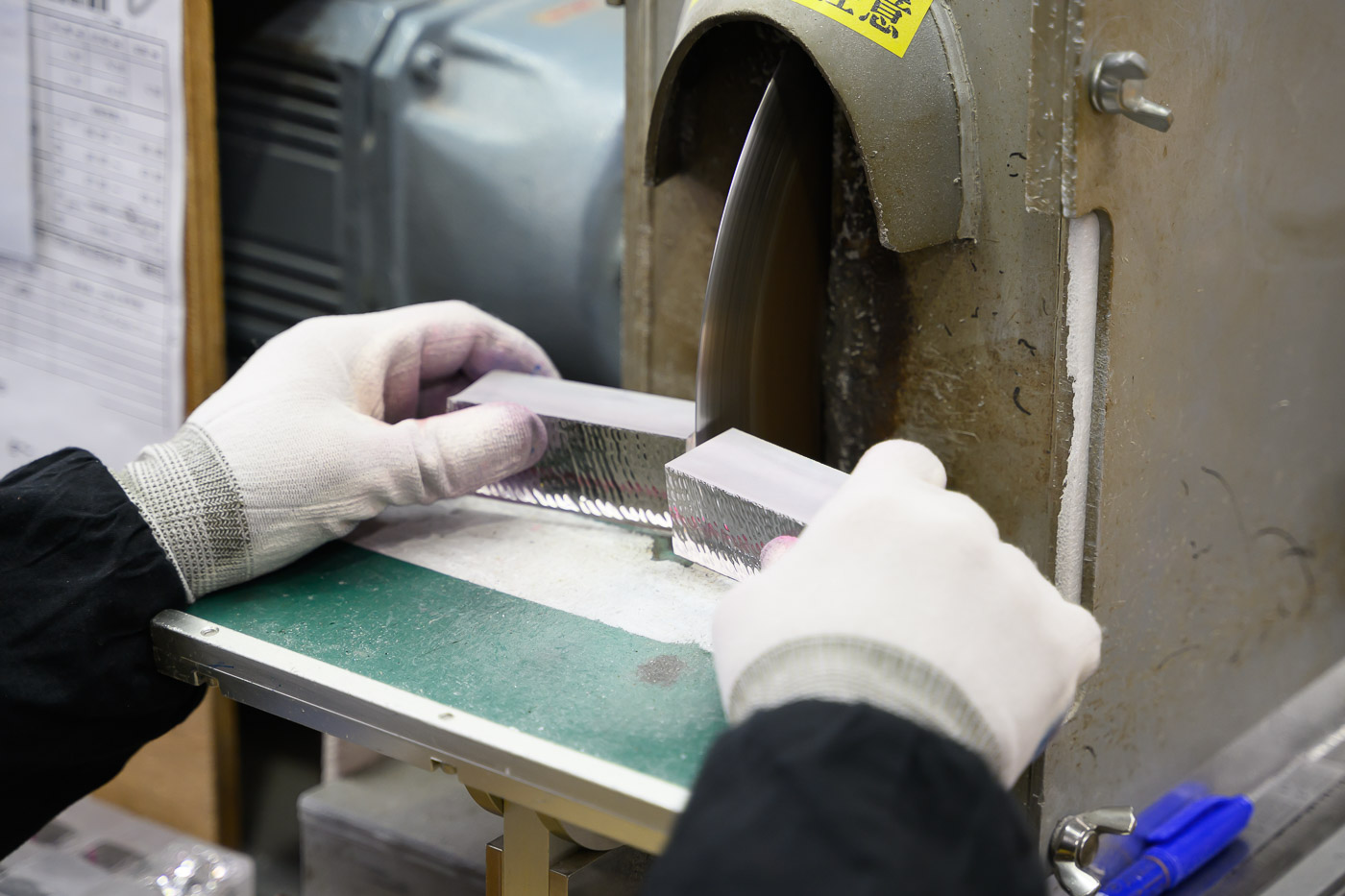
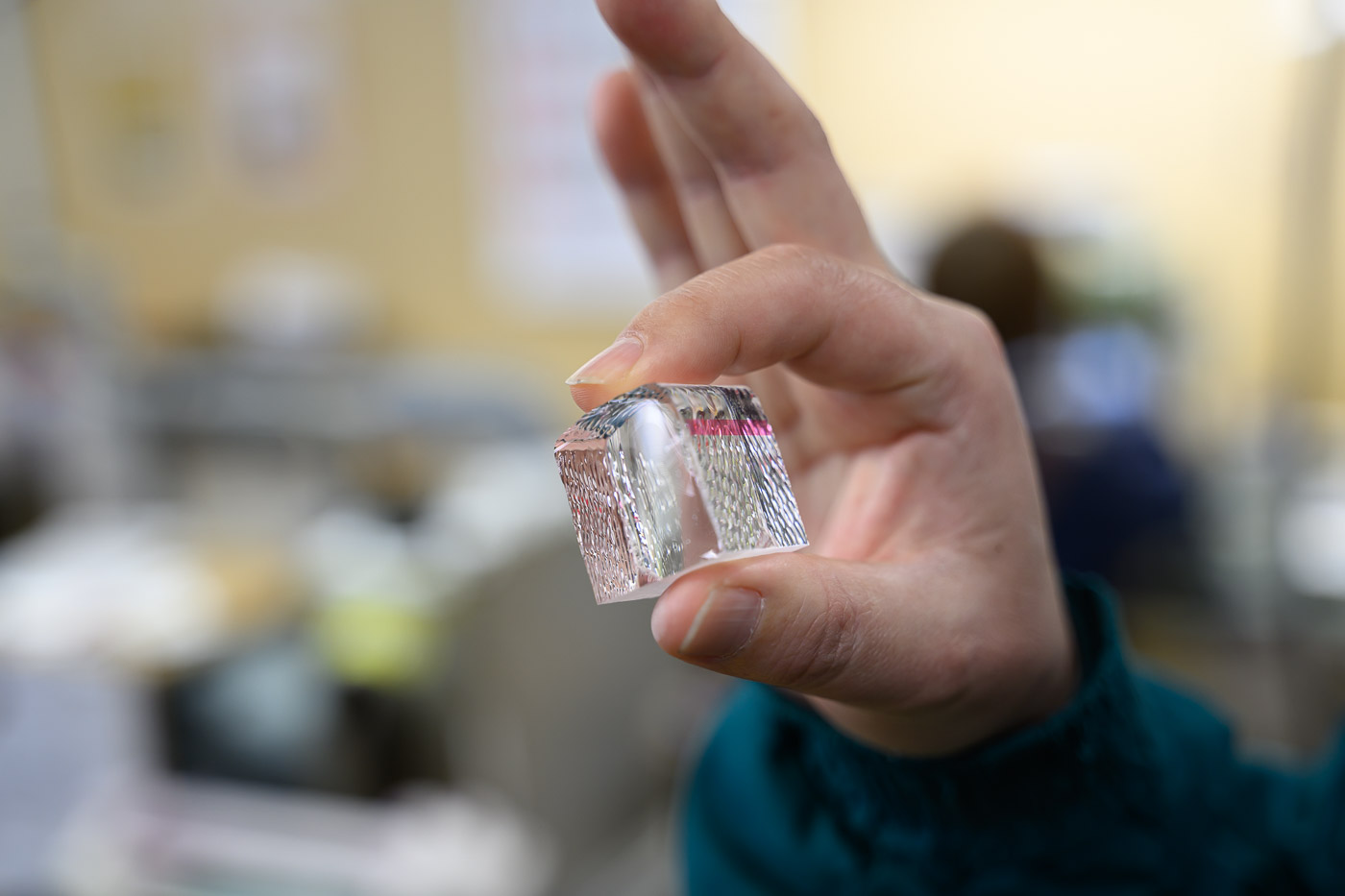
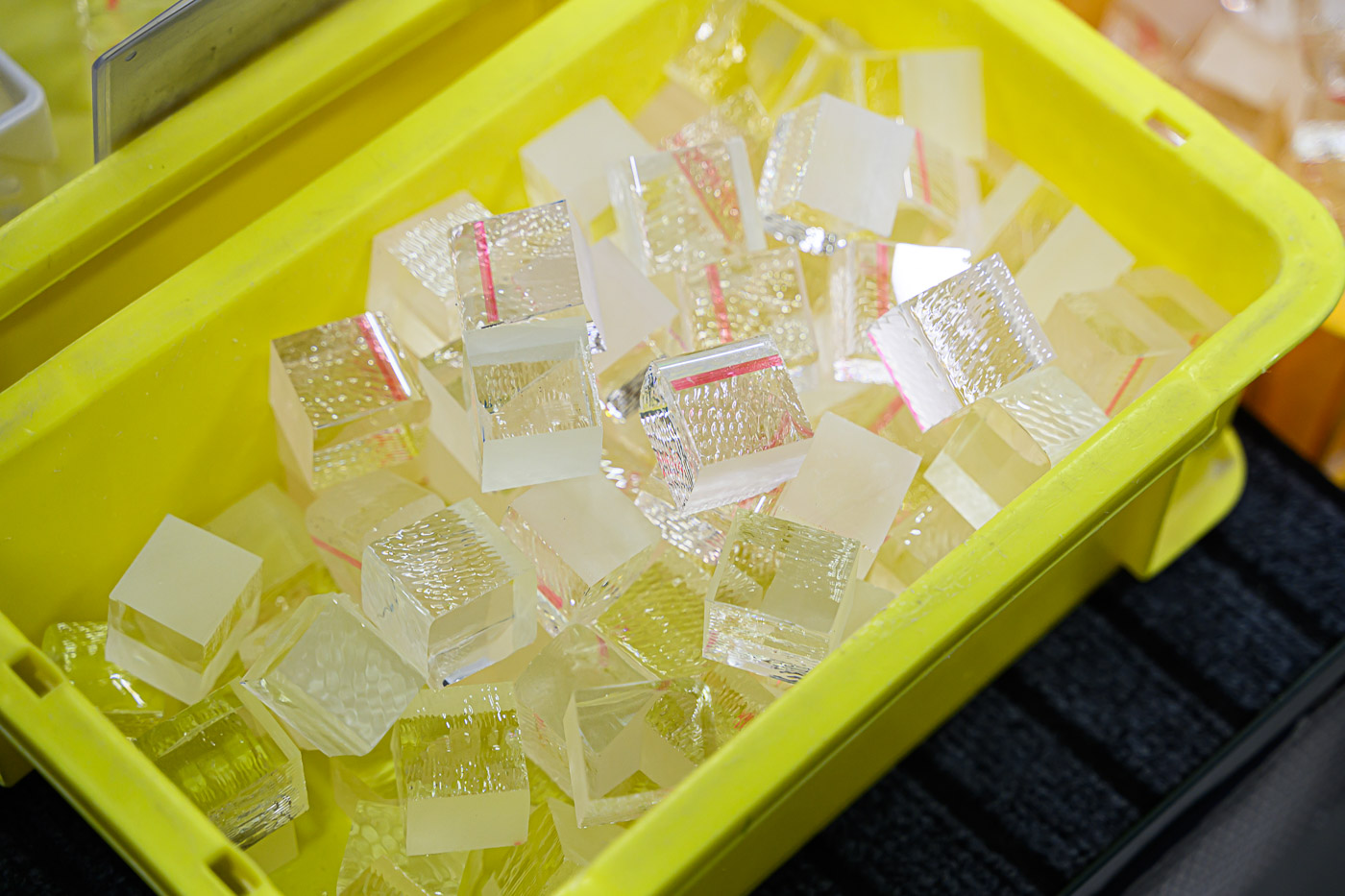
Ensuite, les cubes sont mélangés à des cailloux ou des billes placées dans des récipients, avec de l’eau et du sable. Grâce à une rotation contrôlée et au phénomène d’abrasion, le verre est poli pour ajuster le poids de chaque morceau.
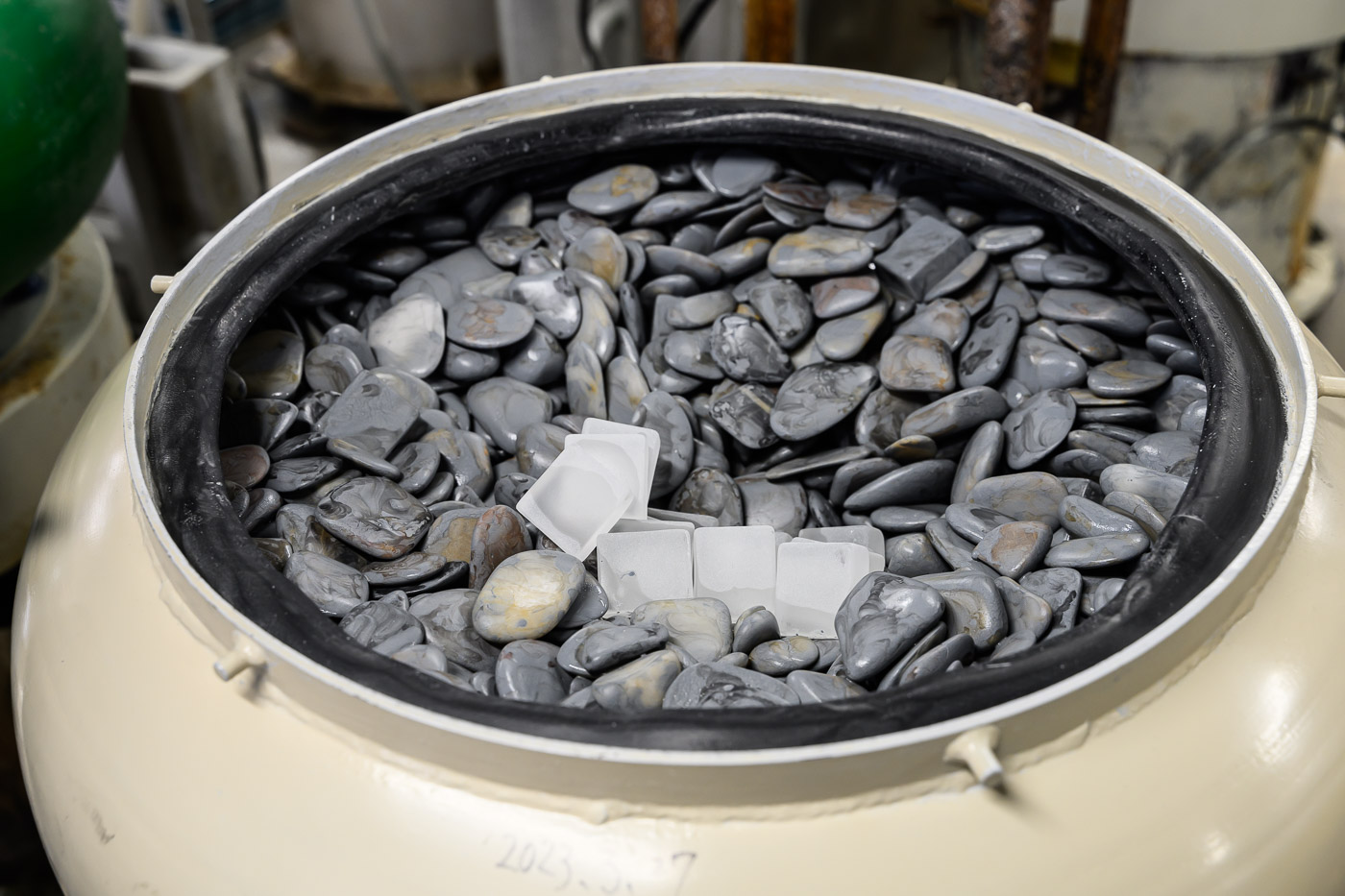
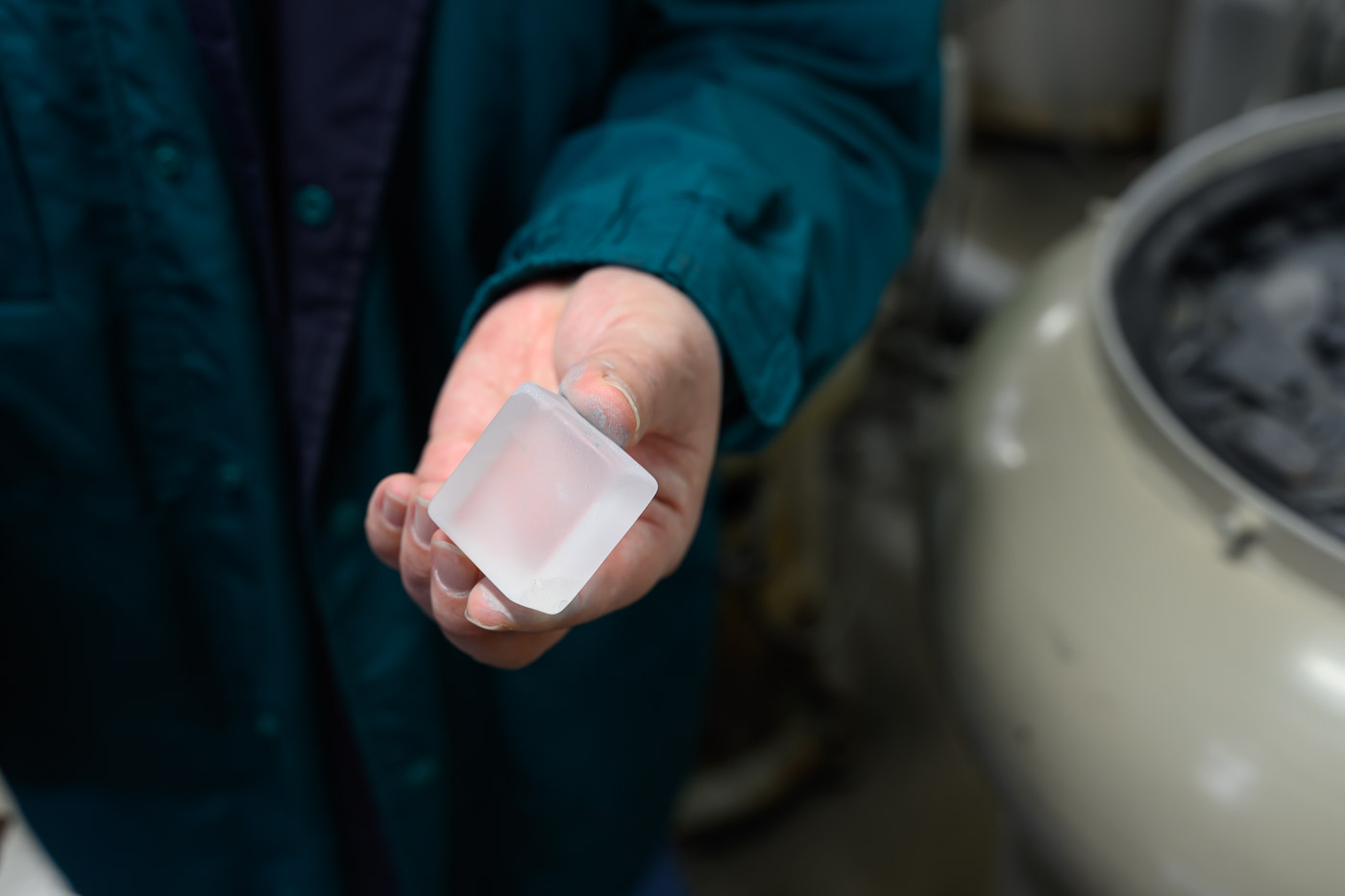
Au sortir de cette étape, les cubes de verre, plus ou moins gros selon la lentille visée, disposent de bords arrondis. Ils sont enduits d’une poudre, comme une sorte de farine, qui permet d’éviter que le verre ne colle au moule. À ce moment-là, le verre est prêt à subir sa dernière étape.
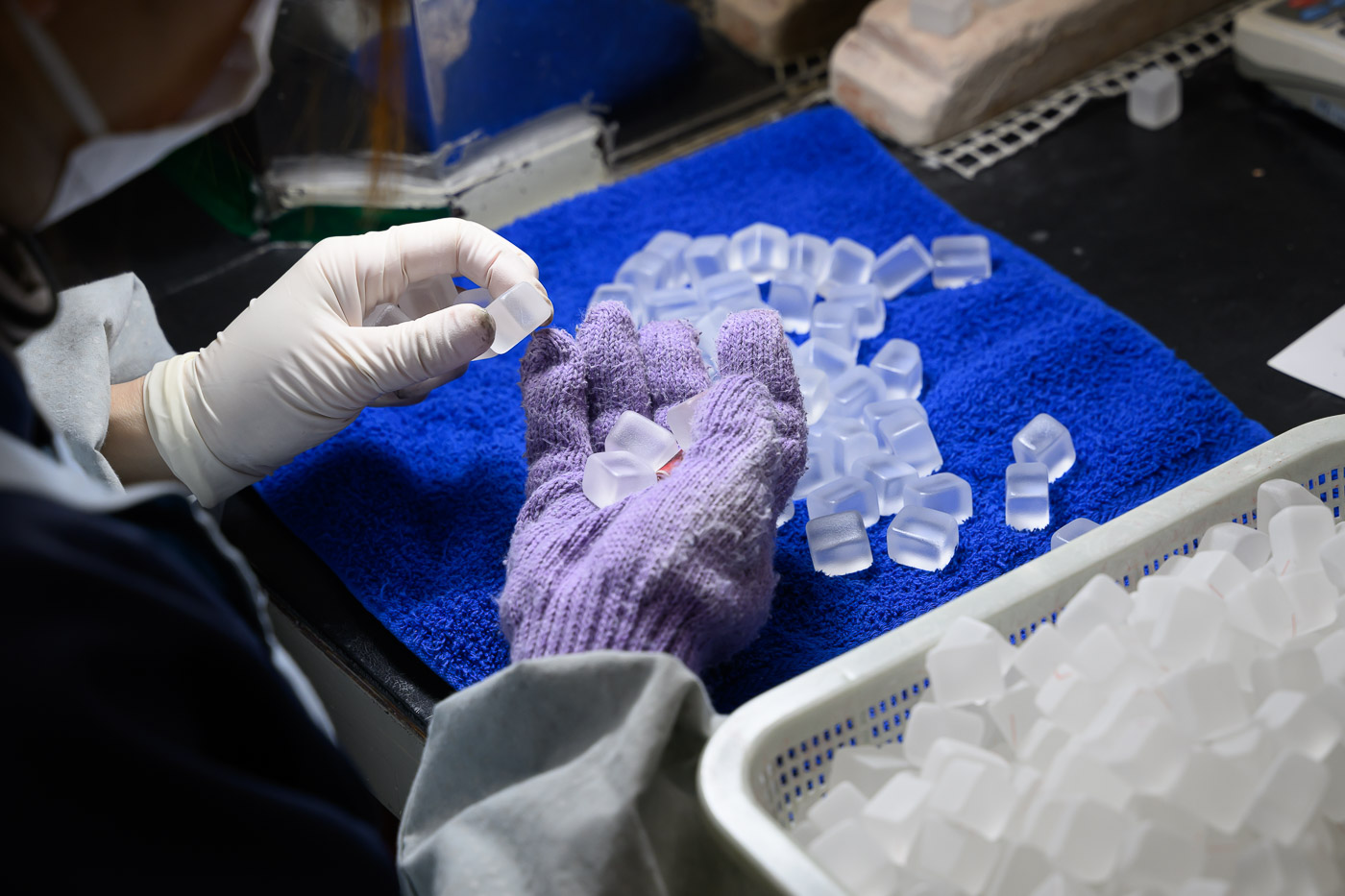
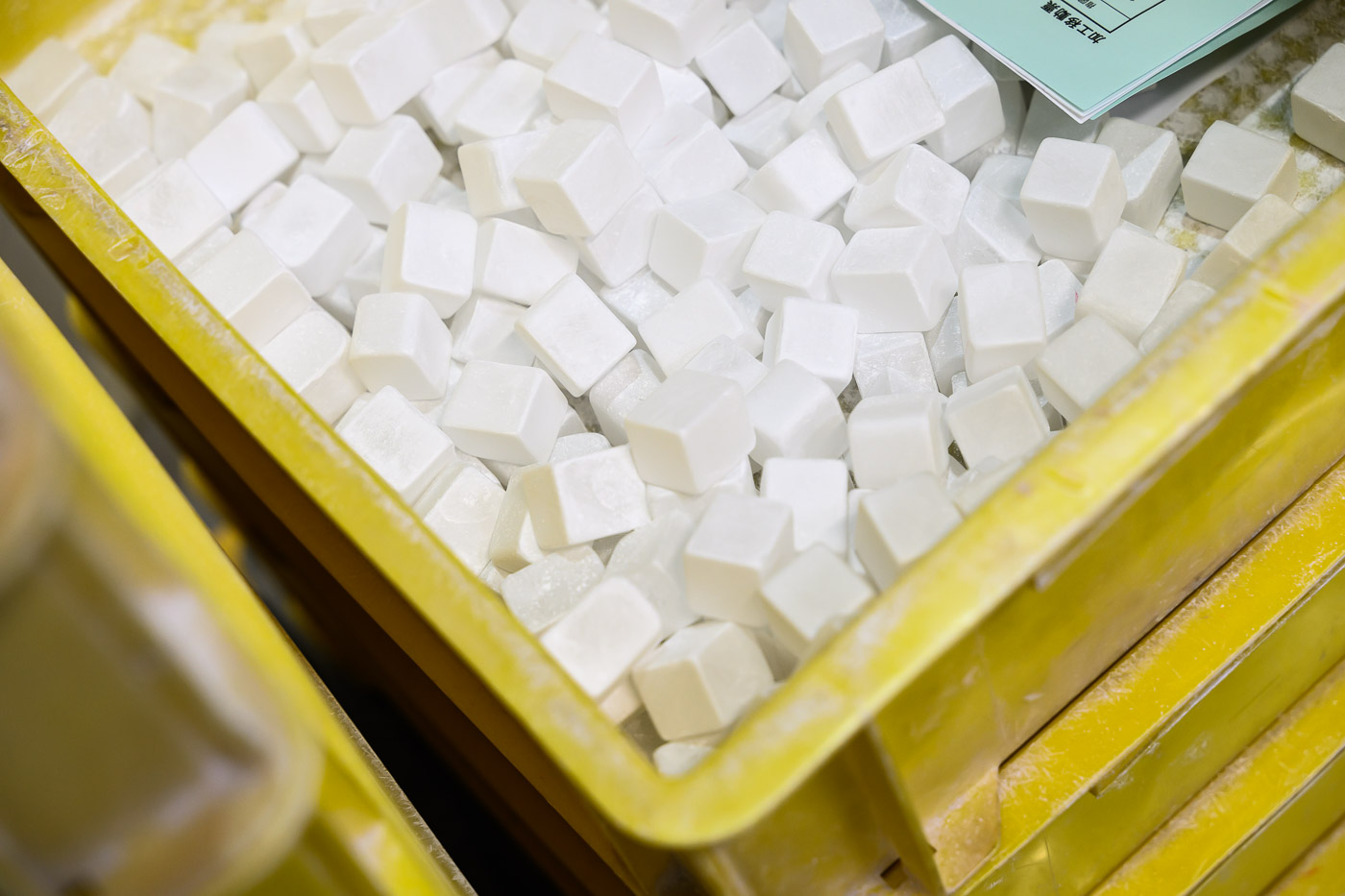
La presse, ultime étape de transformation pour les blocs de verre
L’étape du pressage des blocs de verre est celle qui va donner sa forme finale à la lentille. Pour cela, les petits cubes de verre sont placés dans des creusets sur un convoyeur, puis sont réchauffés dans un four, afin d’être plus malléables.
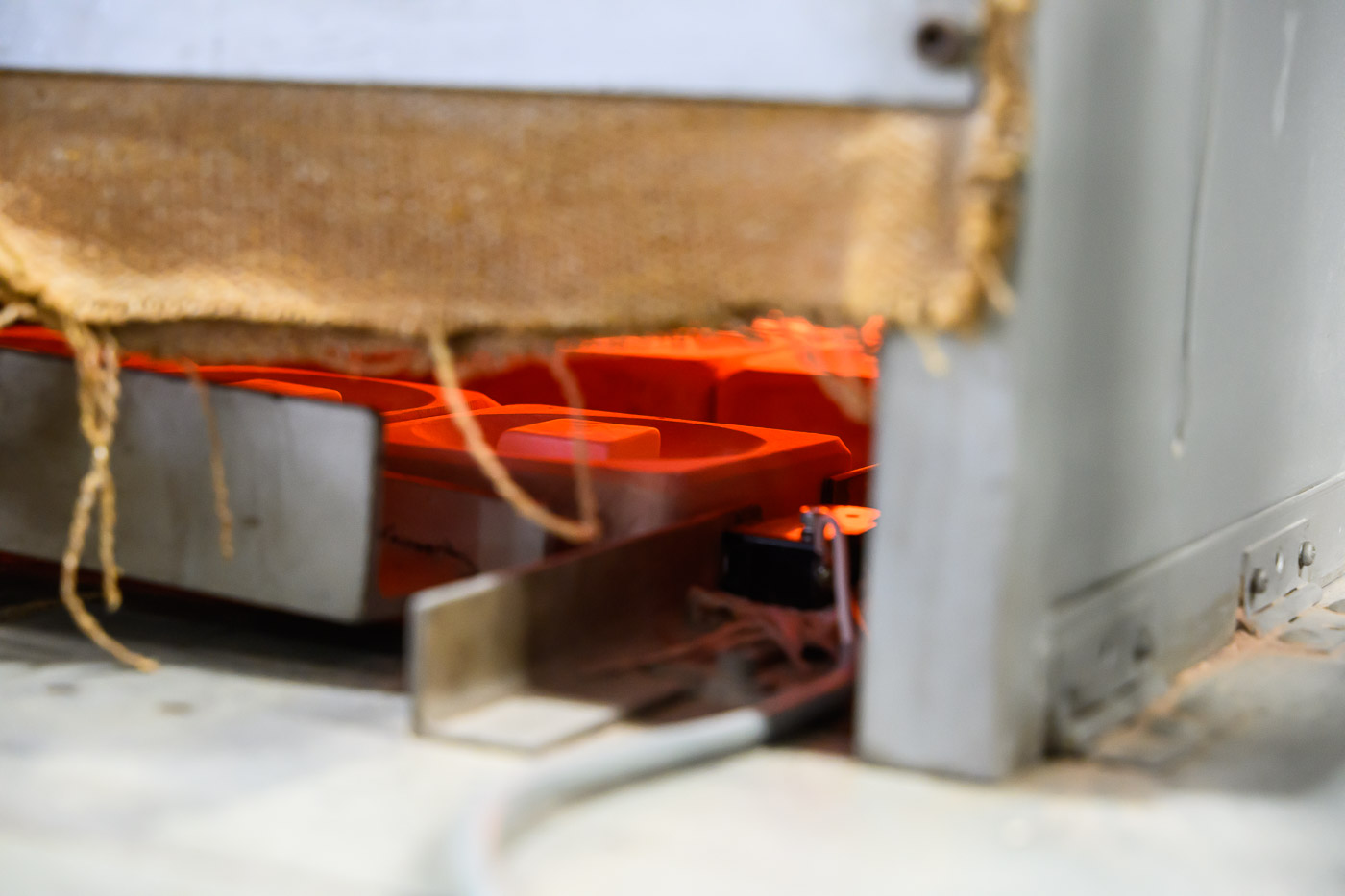
Ensuite, les cubes sont placés dans de petits moules, puis pressés pour obtenir la forme de la lentille voulue.
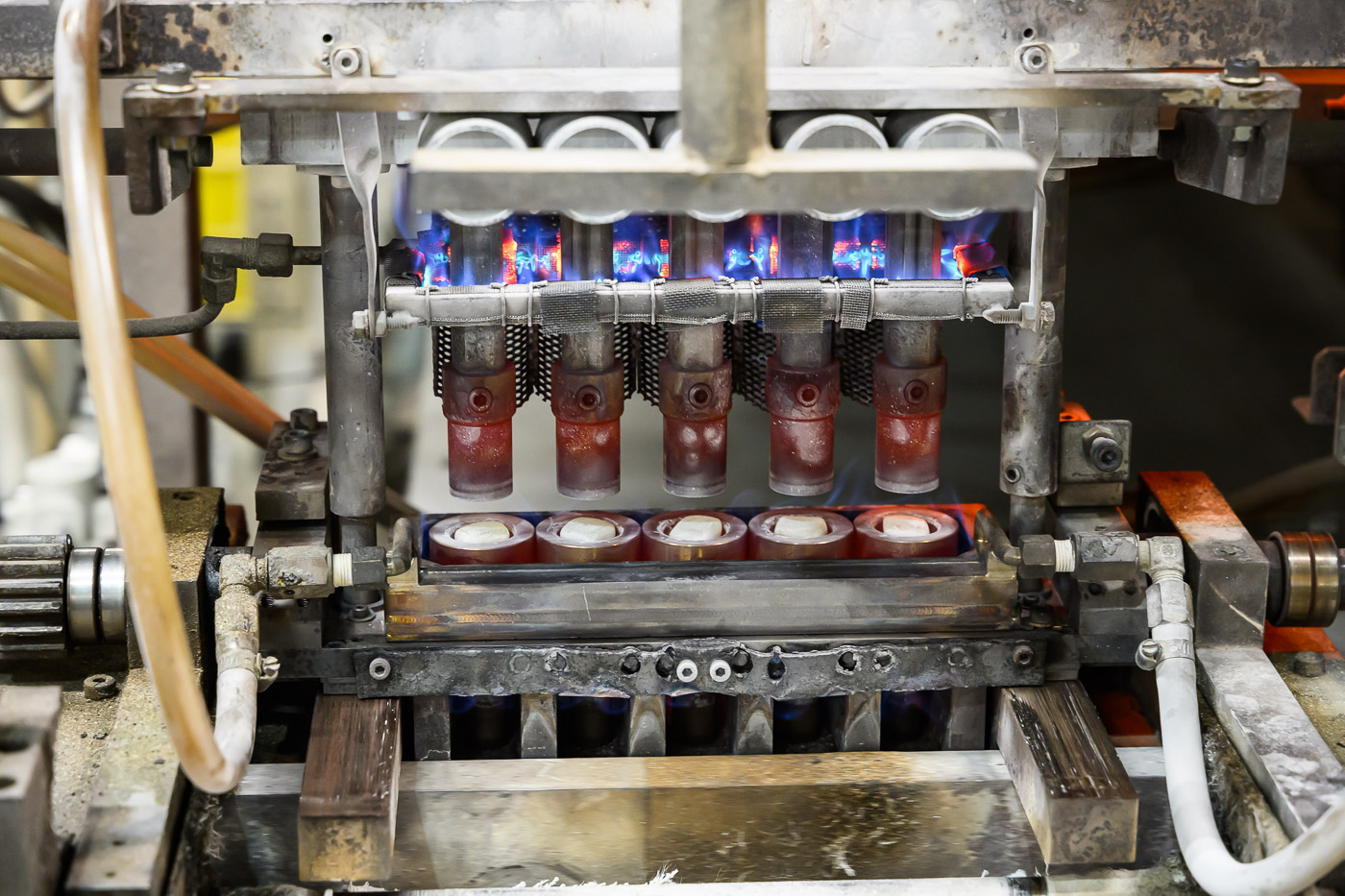
Alors que pour les petites lentilles, le processus est automatisé, pour les blocs de verre les plus gros, cette étape est entièrement manuelle. Une fois les cubes en verre sortis du four, un employé les transvase dans un moule. Un second employé place ensuite ce moule sous un vérin pneumatique chauffé à haute température puis actionne la presse pour donner sa forme à la lentille.
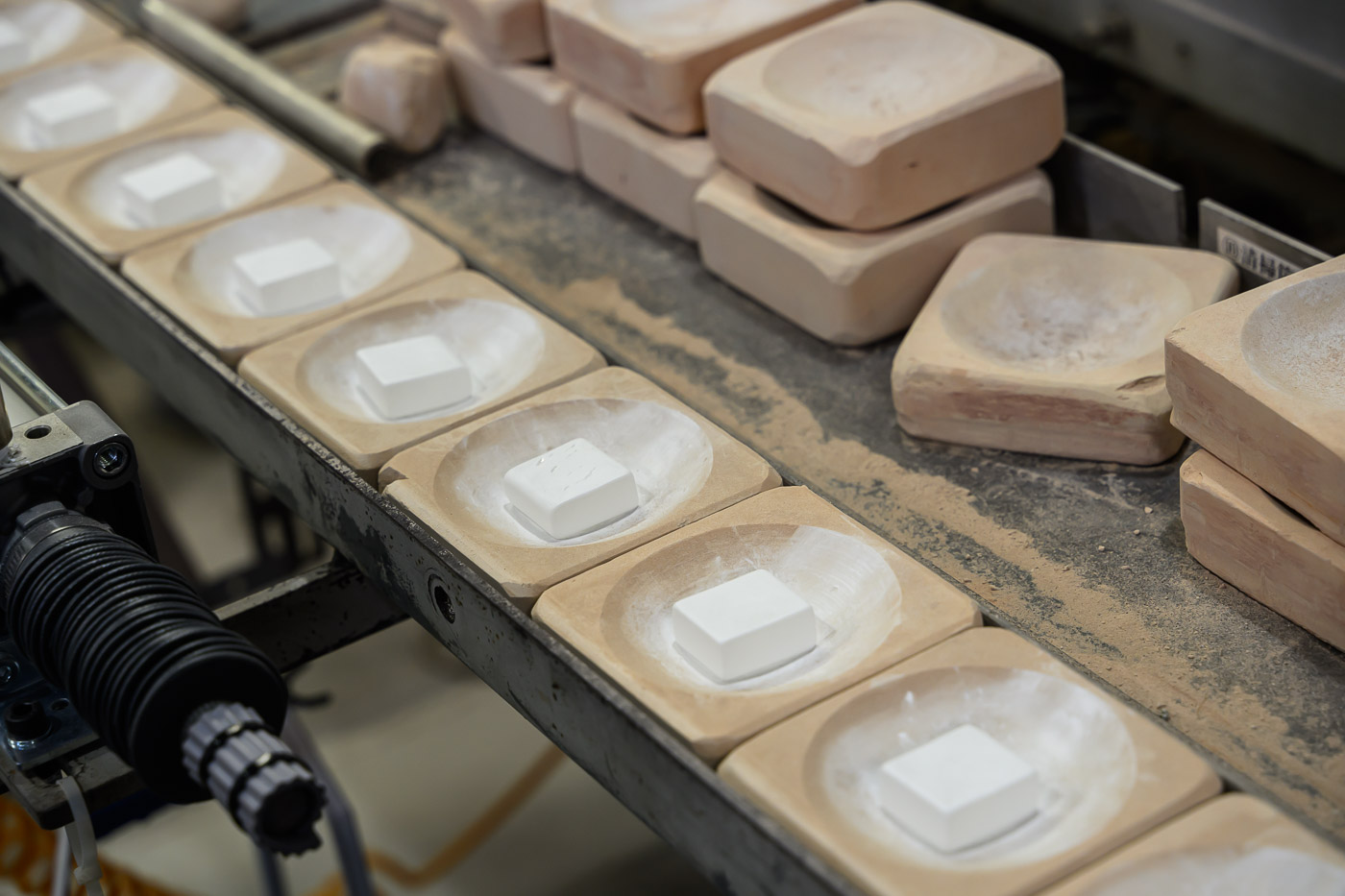
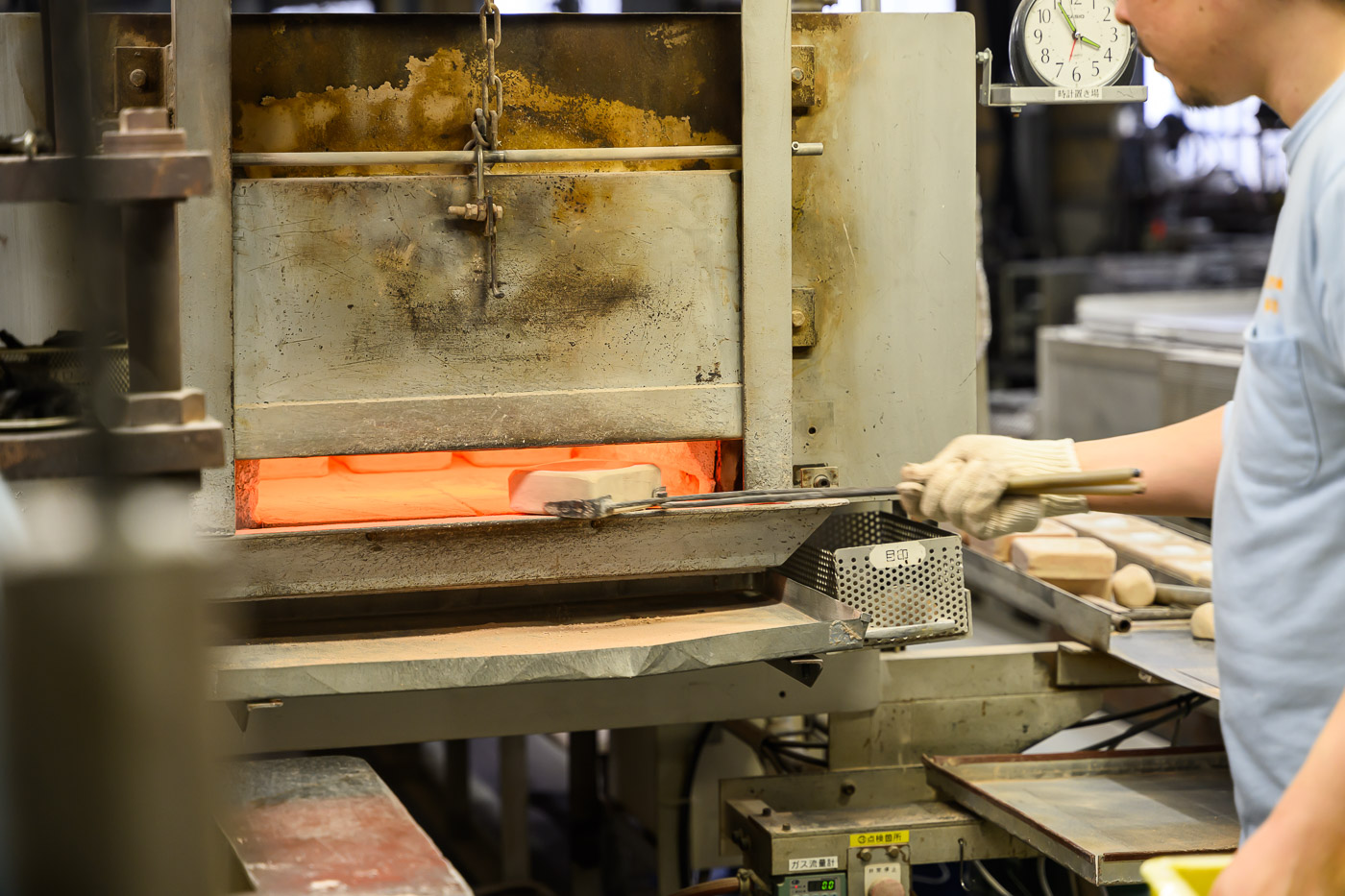
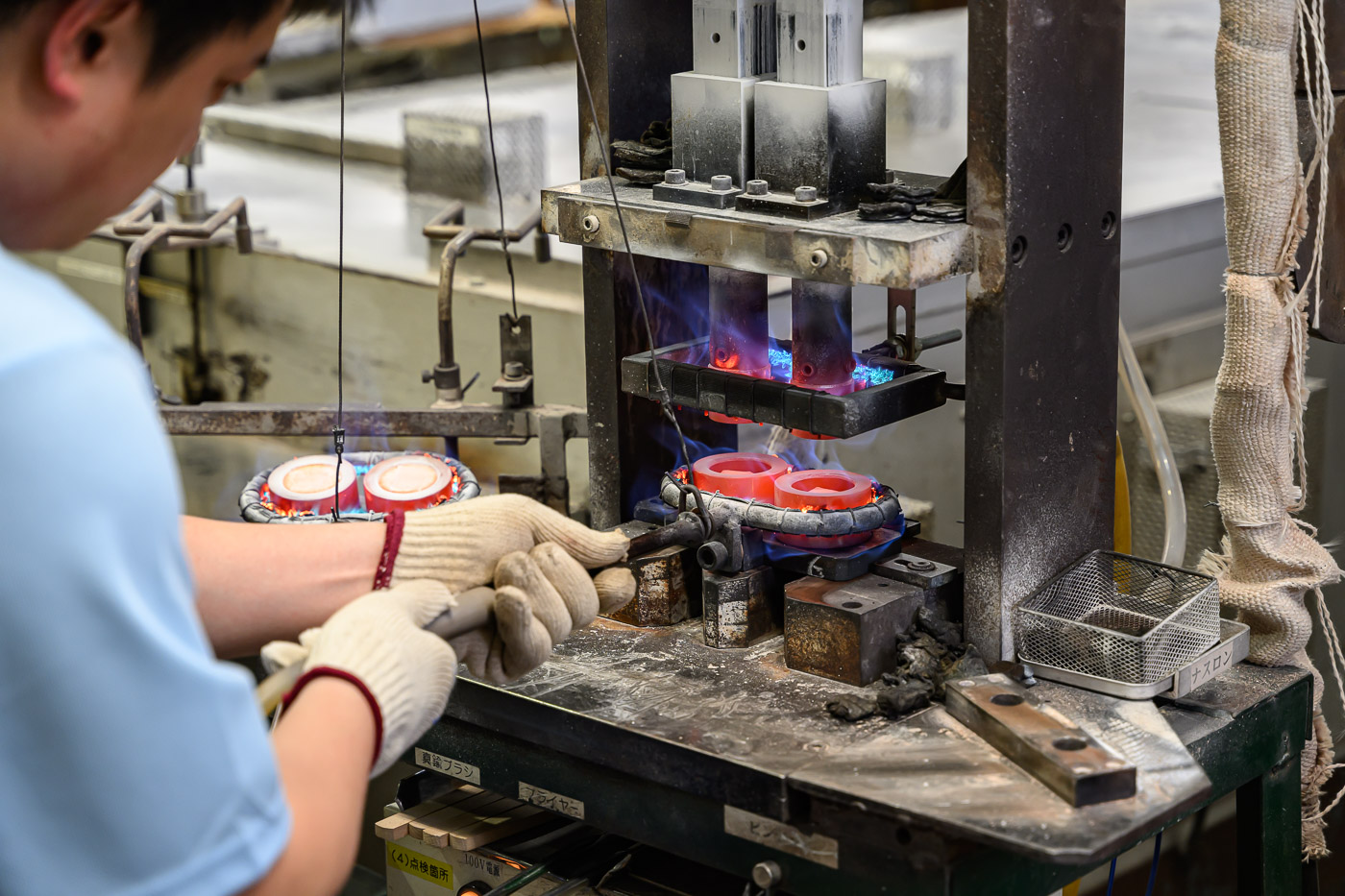
Enfin, un troisième employé récupère les morceaux de verre, qui ressemblent désormais à une galette, et vient les placer sur un autre convoyeur en direction d’un autre four qui va venir abaisser la température du verre de manière progressive.
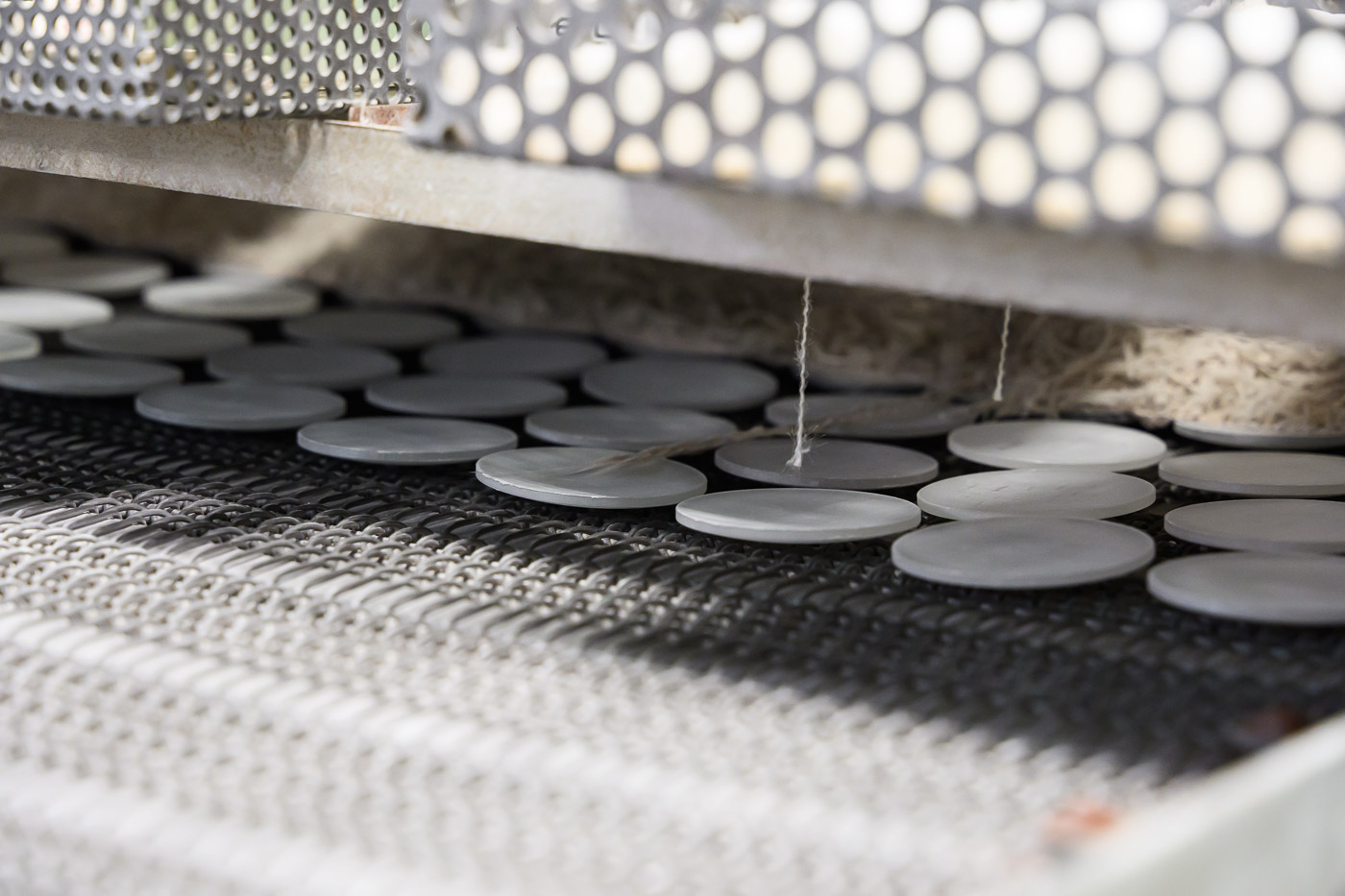
Après cela, la dernière étape est le recuit, qui consiste à placer le verre – une nouvelle fois – dans un grand four pour réchauffer puis refroidir le verre de manière contrôlée, afin d’éviter que les lentilles ne cassent en refroidissant. Le recuit permet également de contrôler l’indice de réfraction. Ensuite, le refroidissement se fait de manière très lente et dure environ une semaine, ce qui permet également de relâcher les tensions dans le verre et d’homogénéiser les performances des lentilles.
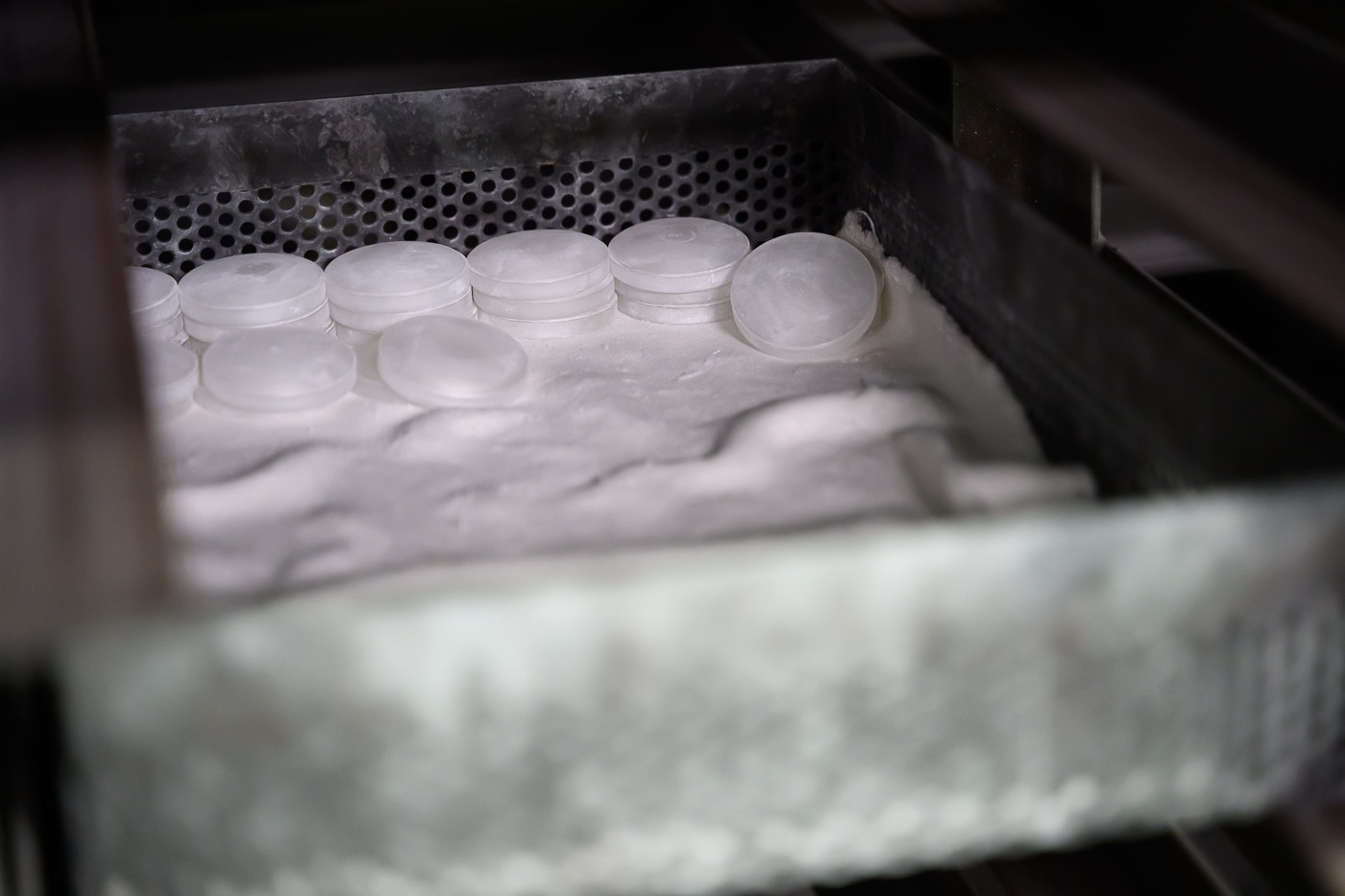
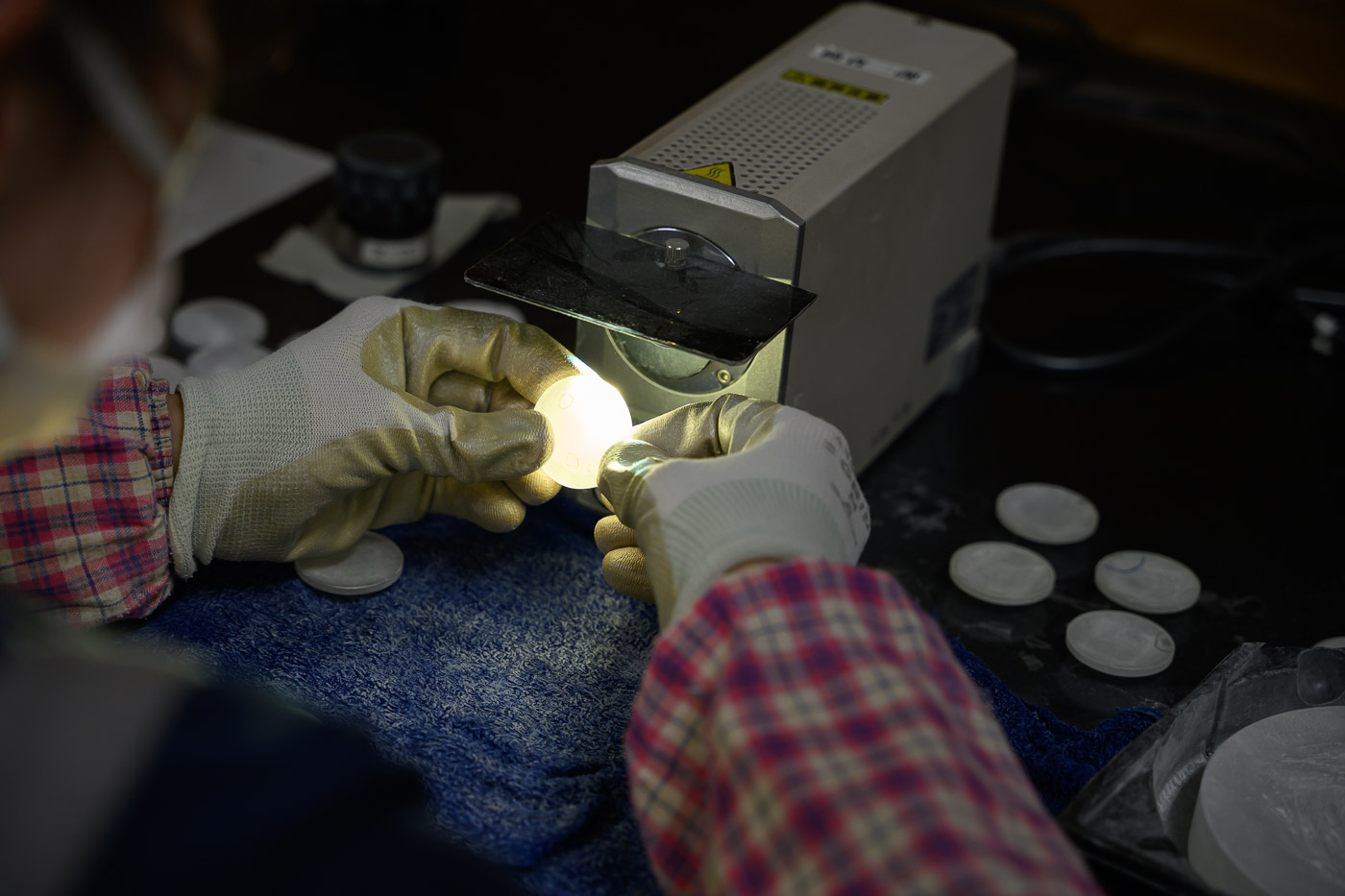
Une fois le verre refroidi, ce dernier est une nouvelle fois inspecté, avant d’être emballé pour être expédié aux différents clients de Hikari Glass, ainsi qu’aux usines Nikon de fabrication d’objectifs, comme celle de Tochigi au Japon.
C’est à ce moment-là que les lentilles seront polies puis traitées avant d’être assemblées au sein des objectifs Nikkor que les Nikonistes ont l’habitude d’utiliser.
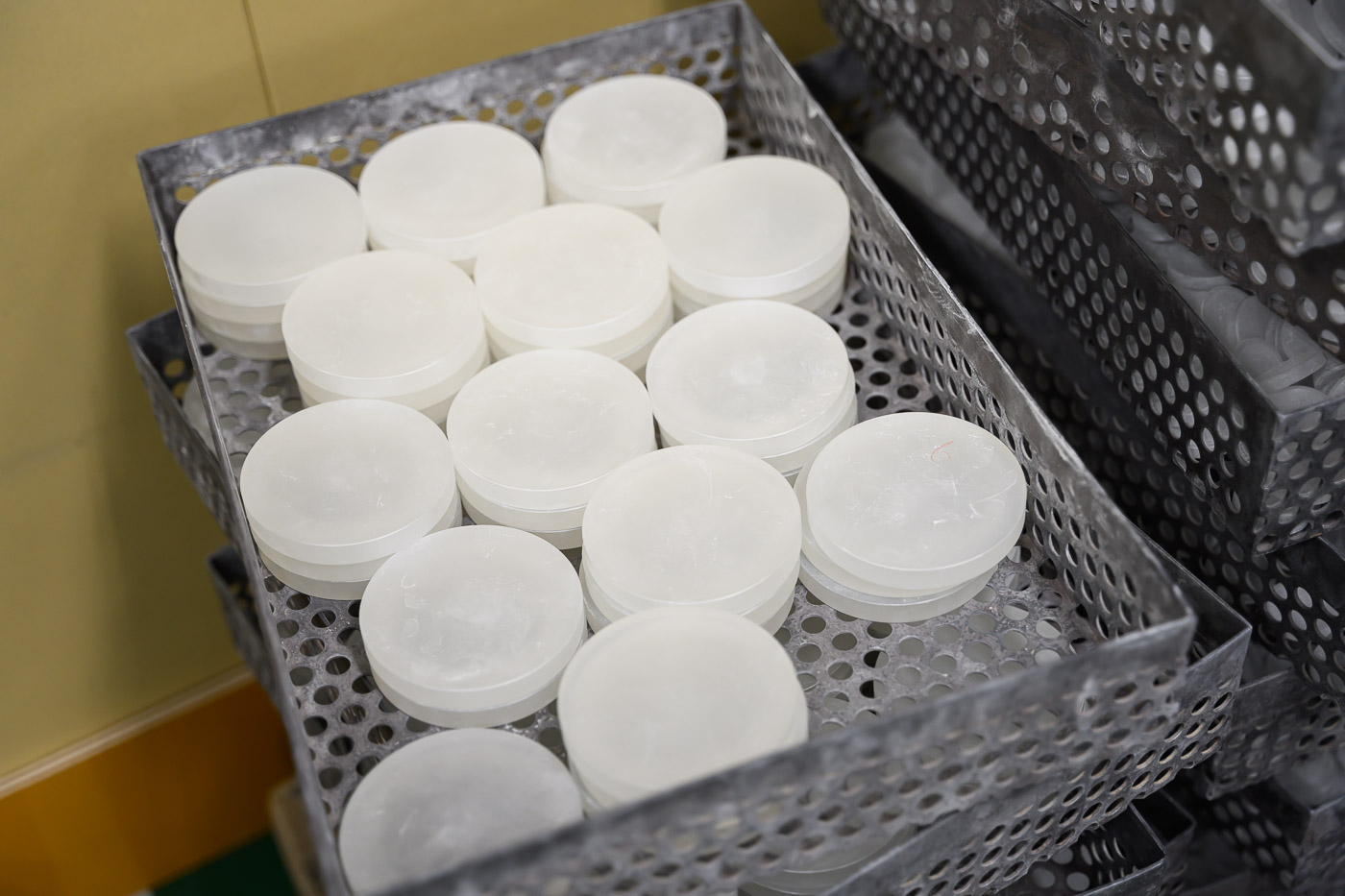
Bilan de la visite de Nikon Hikari Glass
Notre visite à l’usine Nikon Hikari Glass à Yuzawa nous a permis de découvrir l’incroyable travail nécessaire à la fabrication du verre optique de haute qualité, depuis le mélange des matières premières et la fusion, jusqu’à la formation des lentilles par moulage sous haute température. Cette visite a également mis en lumière l’importance historique et technologique de Nikon dans le monde de l’industrie optique.
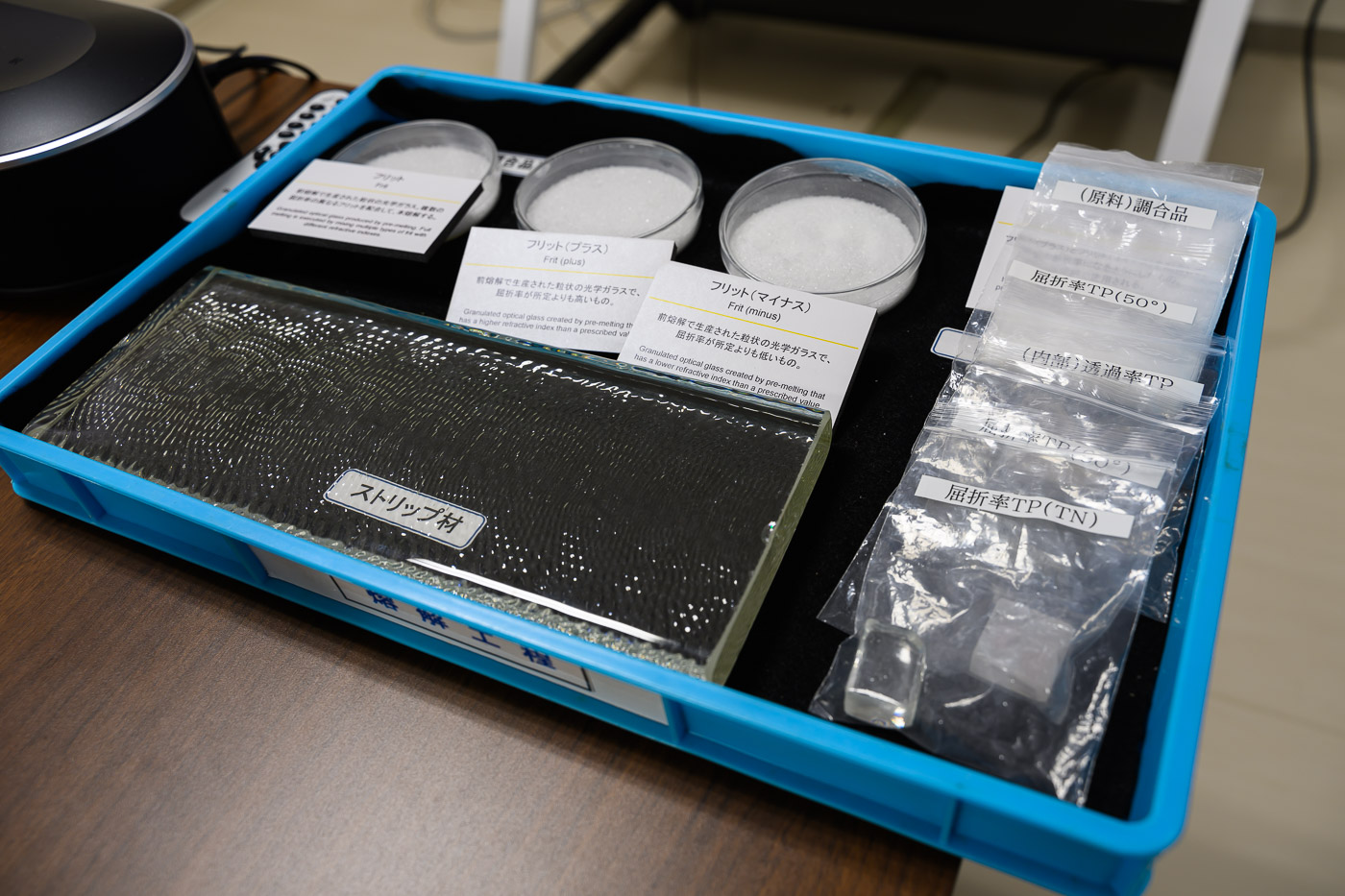
L’usine Nikon Hikari Glass dispose d’un savoir-faire unique, combinant des techniques traditionnelles et des méthodes modernes, permettant de produire du verre optique de la plus haute qualité, utilisé dans les objectifs Nikkor, mais aussi dans une variété d’instruments optiques de précision.
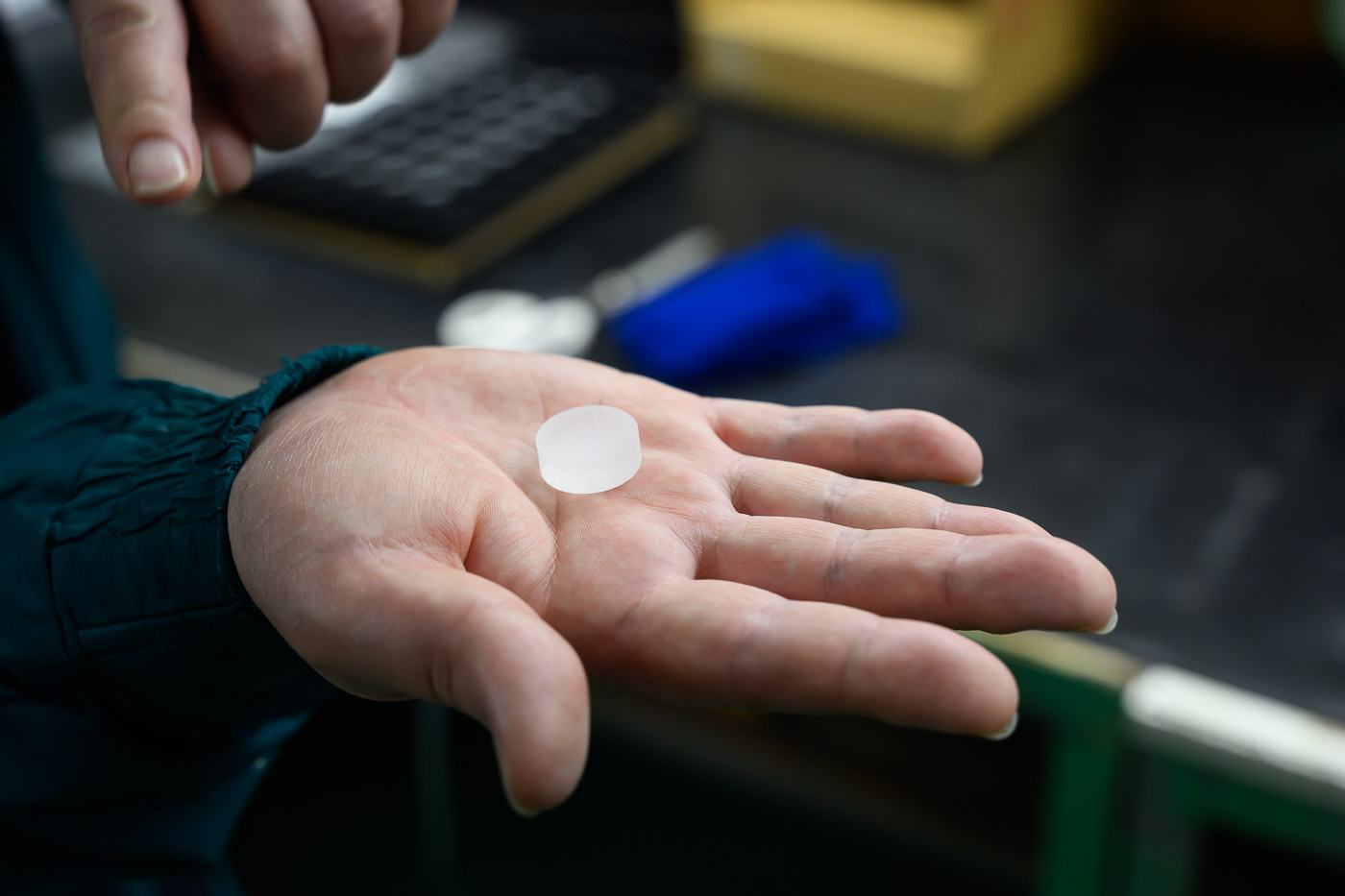
Cette visite nous rappelle l’importance du savoir-faire artisanal et de la précision technique dans la fabrication d’objectifs qui permettent de capturer la beauté du monde avec la plus haute qualité.
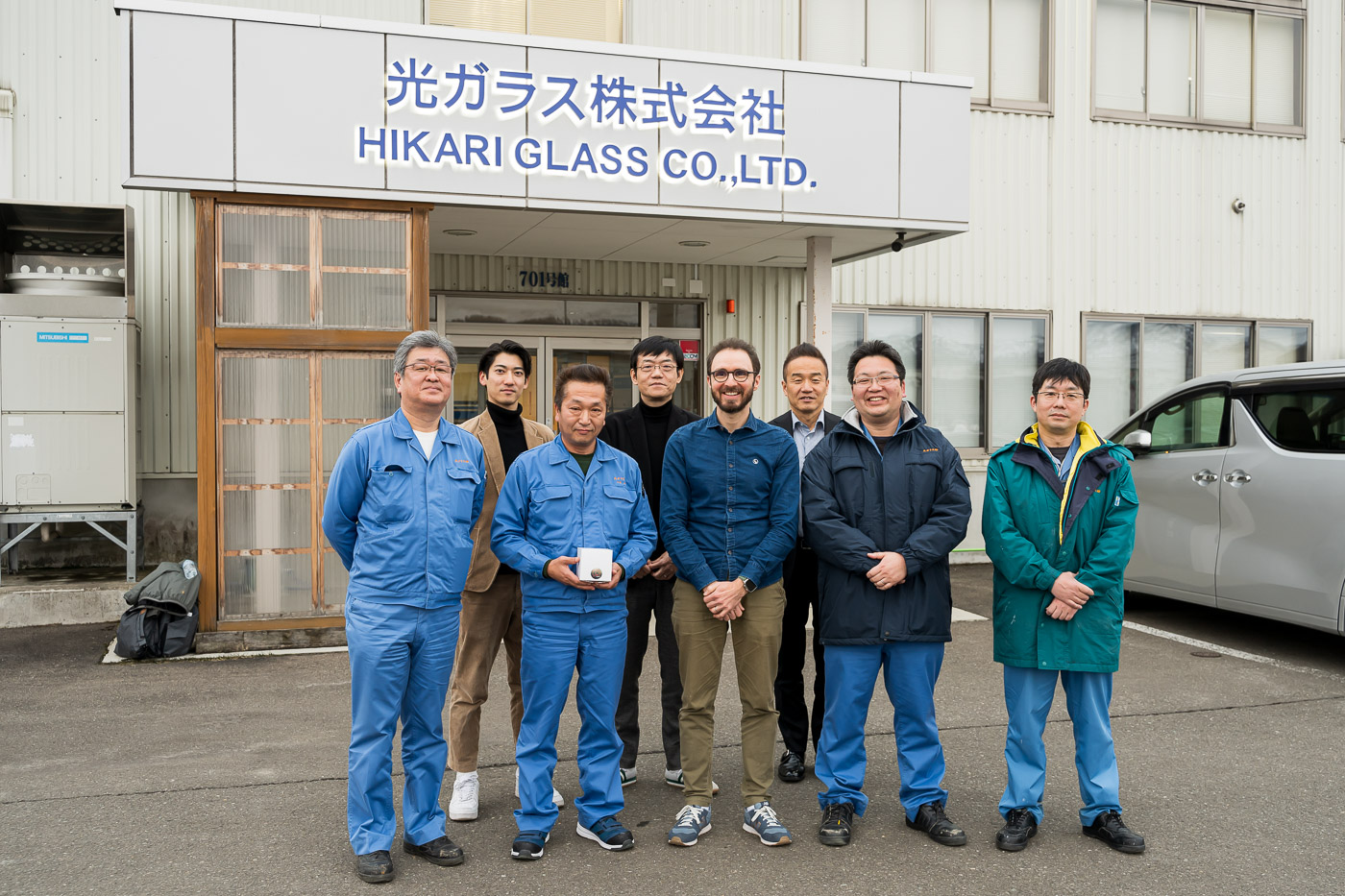
Nous remercions les équipes de Nikon France, Nikon Japon ainsi que le personnel de l’usine Hikari Glass à Yuzawa qui nous ont permis de découvrir ce procédé de façonnage des lentilles.