Sigma has a single manufacturing plant for photographic equipment, located in Japan, in Aizu-Wakamatsu, Fukushima Prefecture, north of Tokyo. During our visit to CP+, we took the opportunity to visit the Sigma Aizu factory to explore the manufacturing process of Sigma lenses.
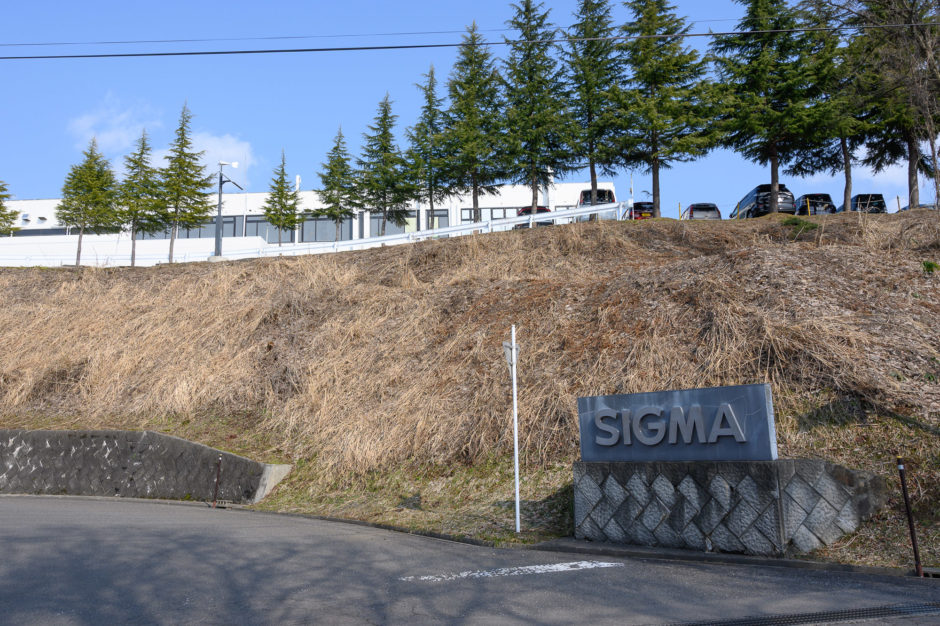
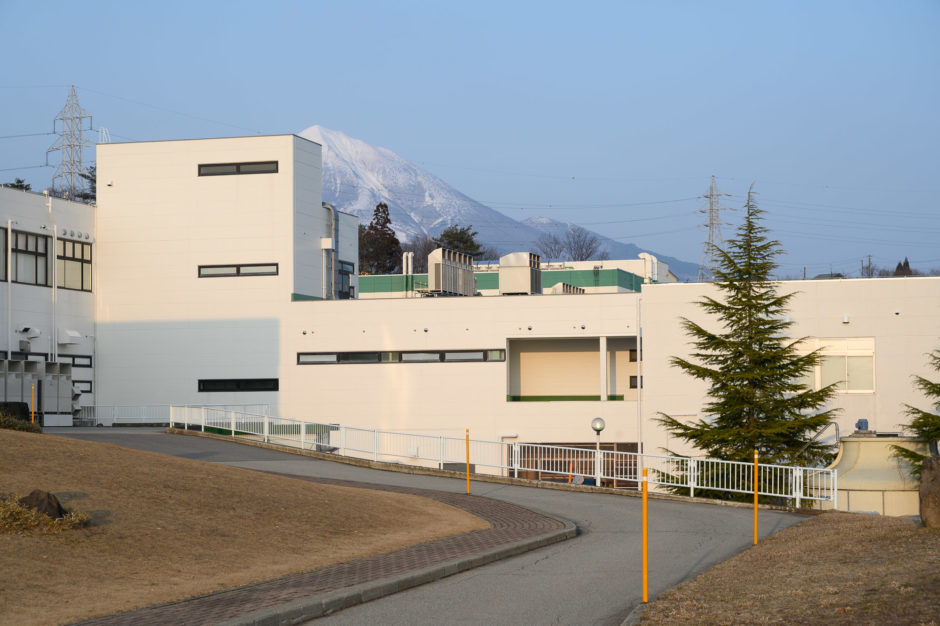
To reach the Aizu factory from Tokyo, one must take the Shinkansen – Japan’s high-speed train – to Koriyama, followed by a regional train that brings travelers closer to the mountainous region, where snow was still visible in March. In total, it takes about 3 hours to reach Aizu from Tokyo by train.
Sommaire
- Sigma and Aizu: The History
- A Modern Facility Dedicated to Magnesium at Sigma
- Sigma Manufactures Its Own Parts, Even the Smallest
- The Workshop Where Molds for Machines Are Made
- Painting Process and Manual Quality Control
- The Stages of Sigma Lens Processing
- Assembly of Sigma Lenses
- The Sigma Museum: A Journey Through the Optician’s History
Sigma and Aizu: The History
The Sigma Aizu factory was built in the early 1970s by Michihiro Yamaki, the founder of Sigma. Nestled at the foot of Mount Bandai, visible from the factory, this optical manufacturing plant has gradually expanded and now employs 1,400 people across a 54,757 m² facility.
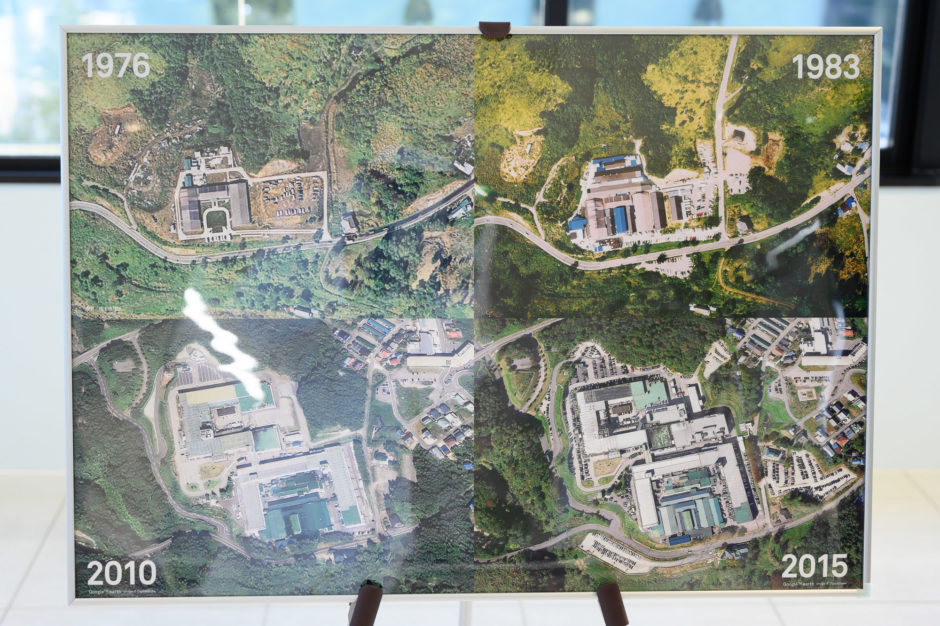
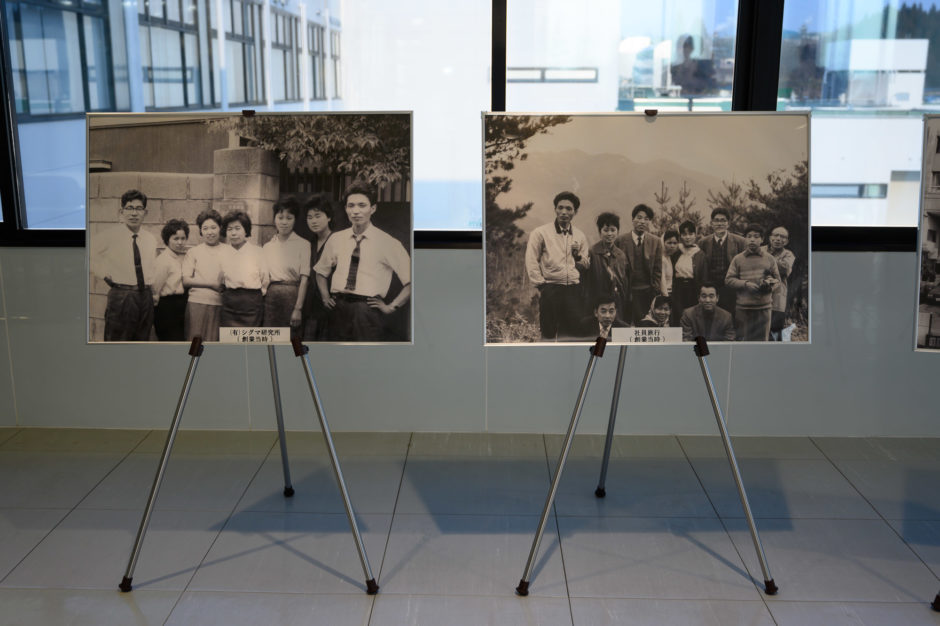
Aizu is a city with a population of 120,000, and Sigma is one of the region’s major employers. Why build a factory in such a remote location, with sometimes harsh winters? As Sigma CEO Kazuto Yamaki explained in an interview, the people of the region “may be a bit conservative, but they maintain their beautiful and traditional Japanese mindset: working hard, being very humble, speaking little, and focusing on their tasks. This mentality is very different from modern Japan, and it works extremely well for designing high-quality products like those made by Sigma.”
At Aizu, the Sigma factory can produce up to 80,000 lenses and 2,000 cameras each month.
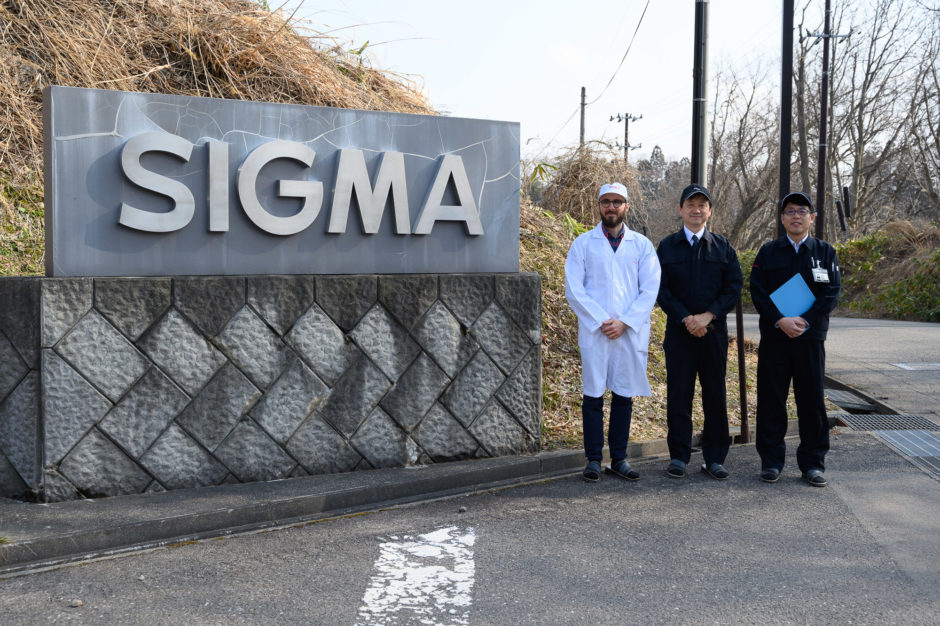
Before starting our factory tour, Sigma introduced us to its company philosophy, particularly in terms of resource management. Sigma operates under the slogan “Small Office, Big Factory”, meaning the company aims to minimize non-essential staff to maximize production capacity. While Sigma’s headquarters are located in Kawasaki, Tokyo, only 200 people work there, 75% of whom are engineers developing new products. Administrative and support functions are kept to a minimum.
Another key element of Sigma’s philosophy is vertical integration of its factory and local procurement of materials. Sigma manufactures many components in-house to achieve the highest quality at the best price. When outsourcing is necessary, the company selects suppliers located near Aizu.
A Modern Facility Dedicated to Magnesium at Sigma
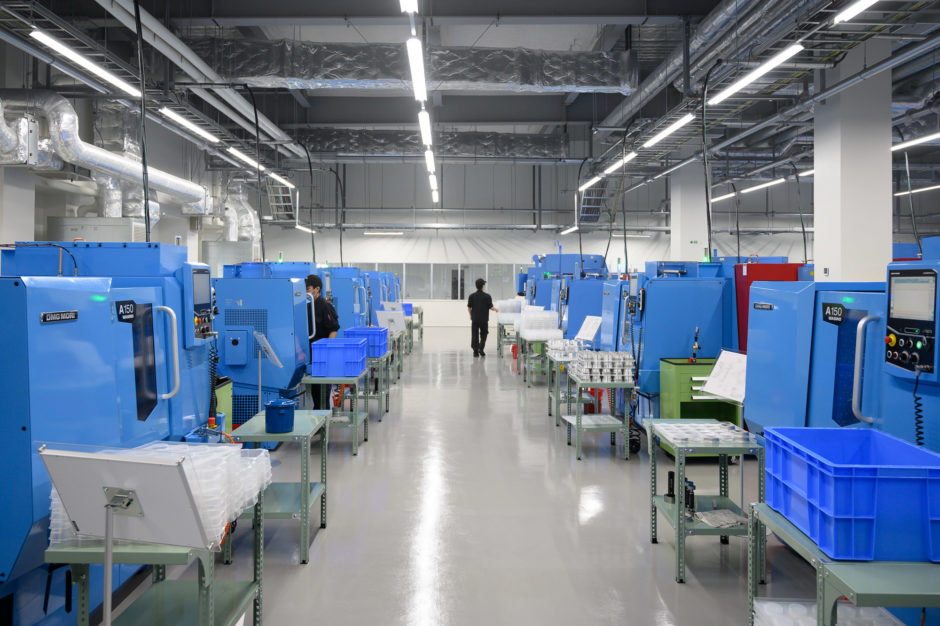
This vertical integration was further expanded in 2018 with the construction of a new section of the Aizu factory, slightly apart from the main building for safety reasons, dedicated to machining magnesium alloy components used in select Sigma lenses and camera bodies. Magnesium is a strong yet lightweight alloy, found in certain Sigma telephoto lenses such as the 60-600mm F4.5-6.3 DG OS HSM Sports and the 70-200mm F2.8 DG OS HSM | Sports.
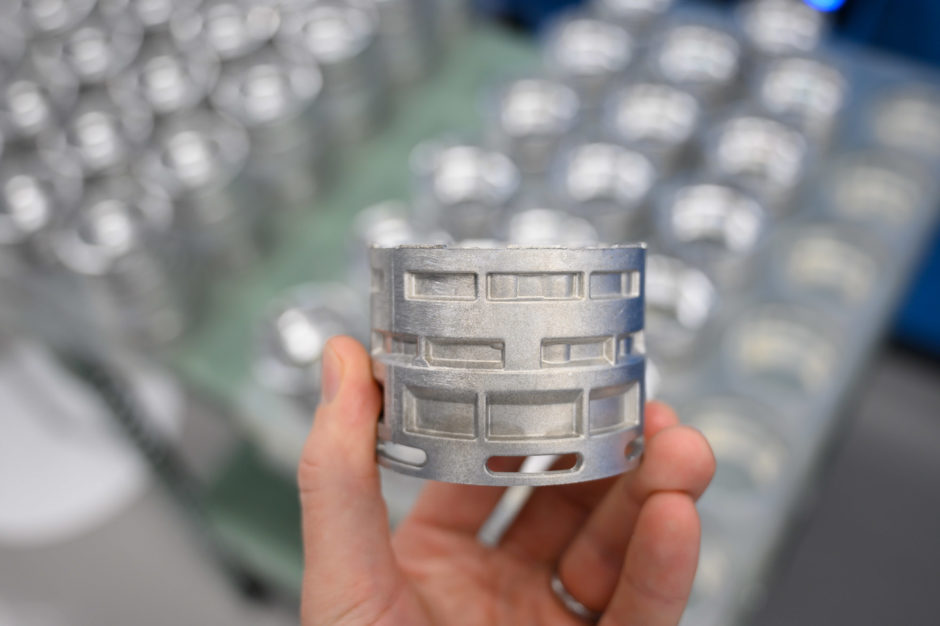
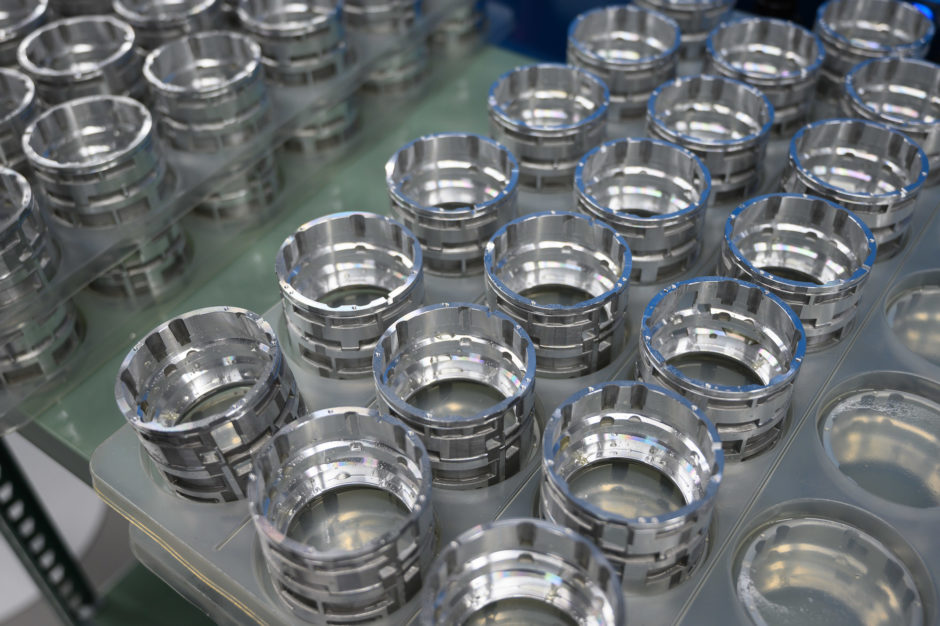
In this section of the factory, magnesium components are polished, cut, or drilled to obtain the final parts used by Sigma. The machines are modern, and most tasks are automated, with a few employees responsible for placing the elements in the machines and operating them.
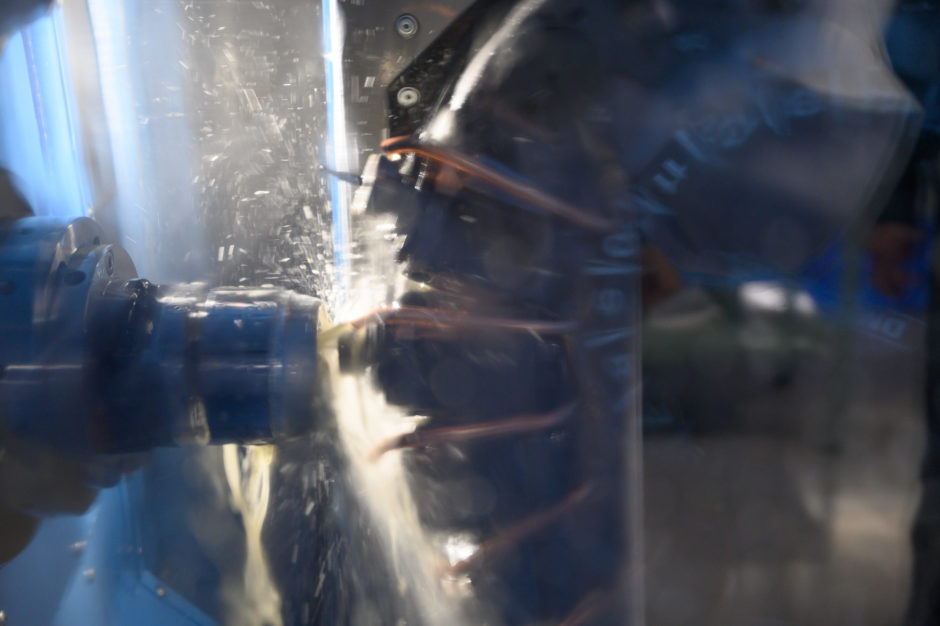
Sigma Manufactures Its Own Parts, Even the Smallest
The next part of the factory tour takes us to a larger section, featuring a green floor where brass and aluminum parts are machined. Among the parts manufactured here are lens mounts, barrels, and other metallic elements that make up a camera lens. Stacks of boxes filled with mounts wait to move to the next stage or to be machined by these specialized machines. This area clearly illustrates Sigma’s policy of manufacturing its own components, down to the tiny screws and brass components that fit in the palm of a hand.
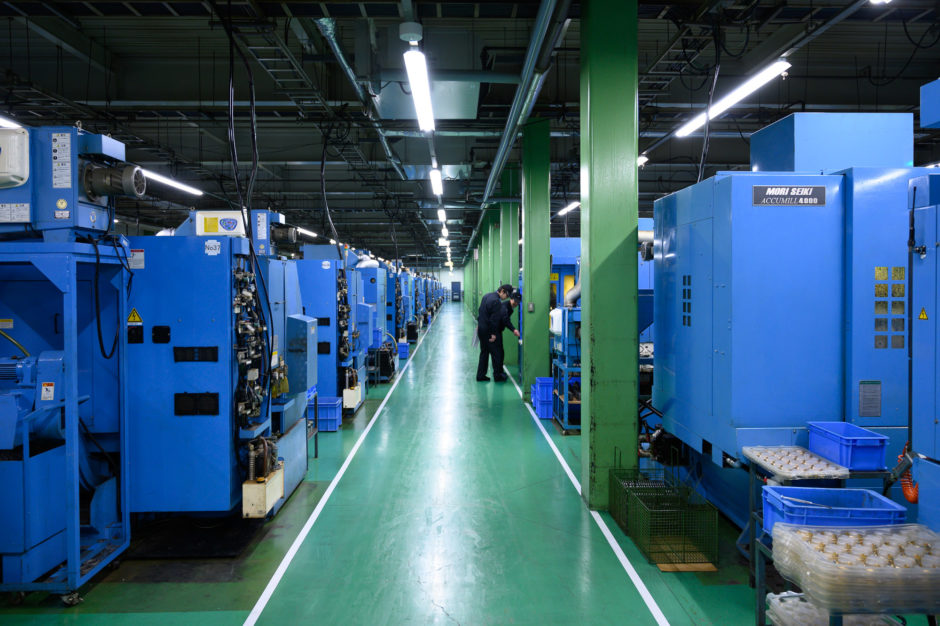
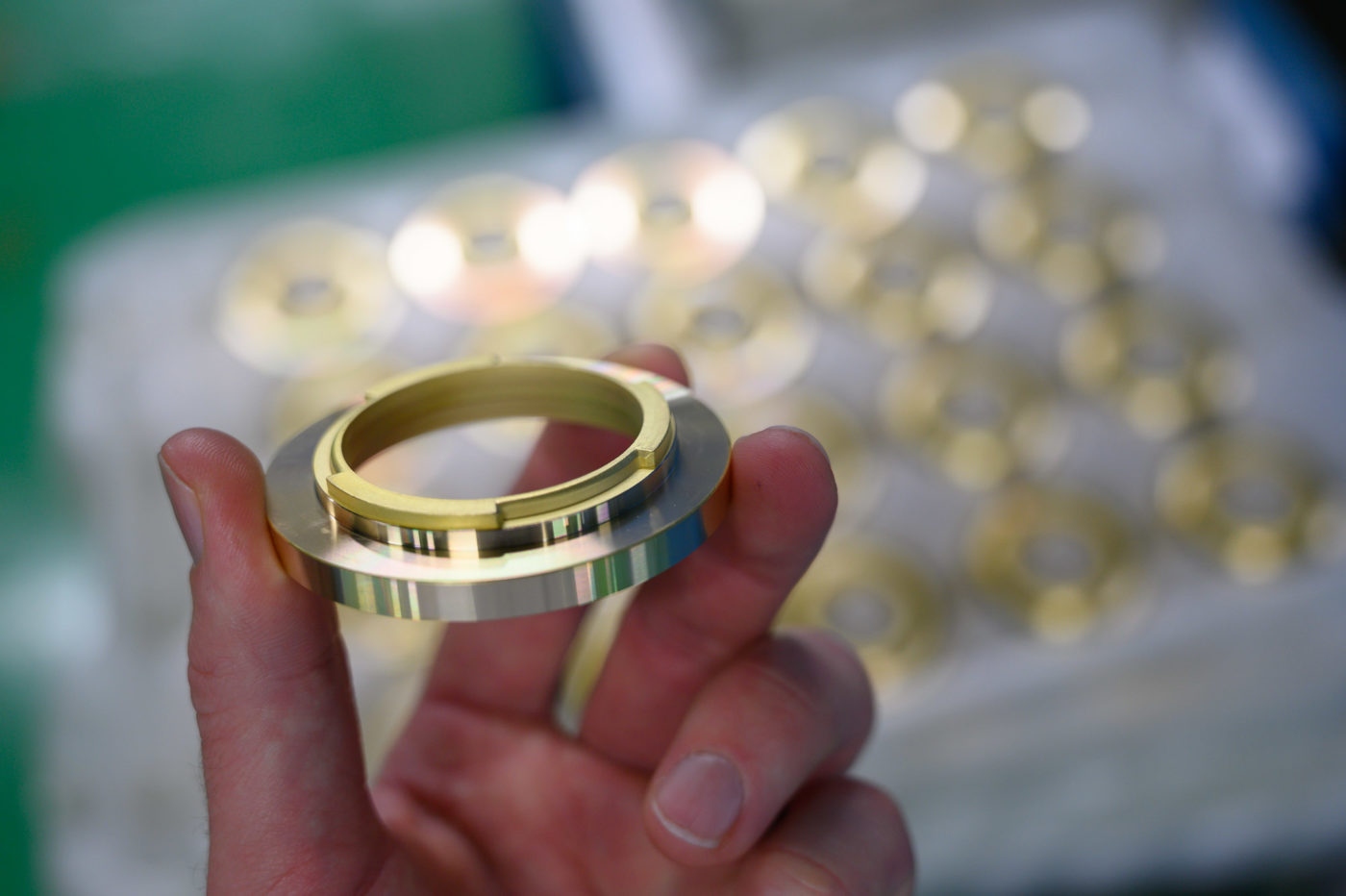
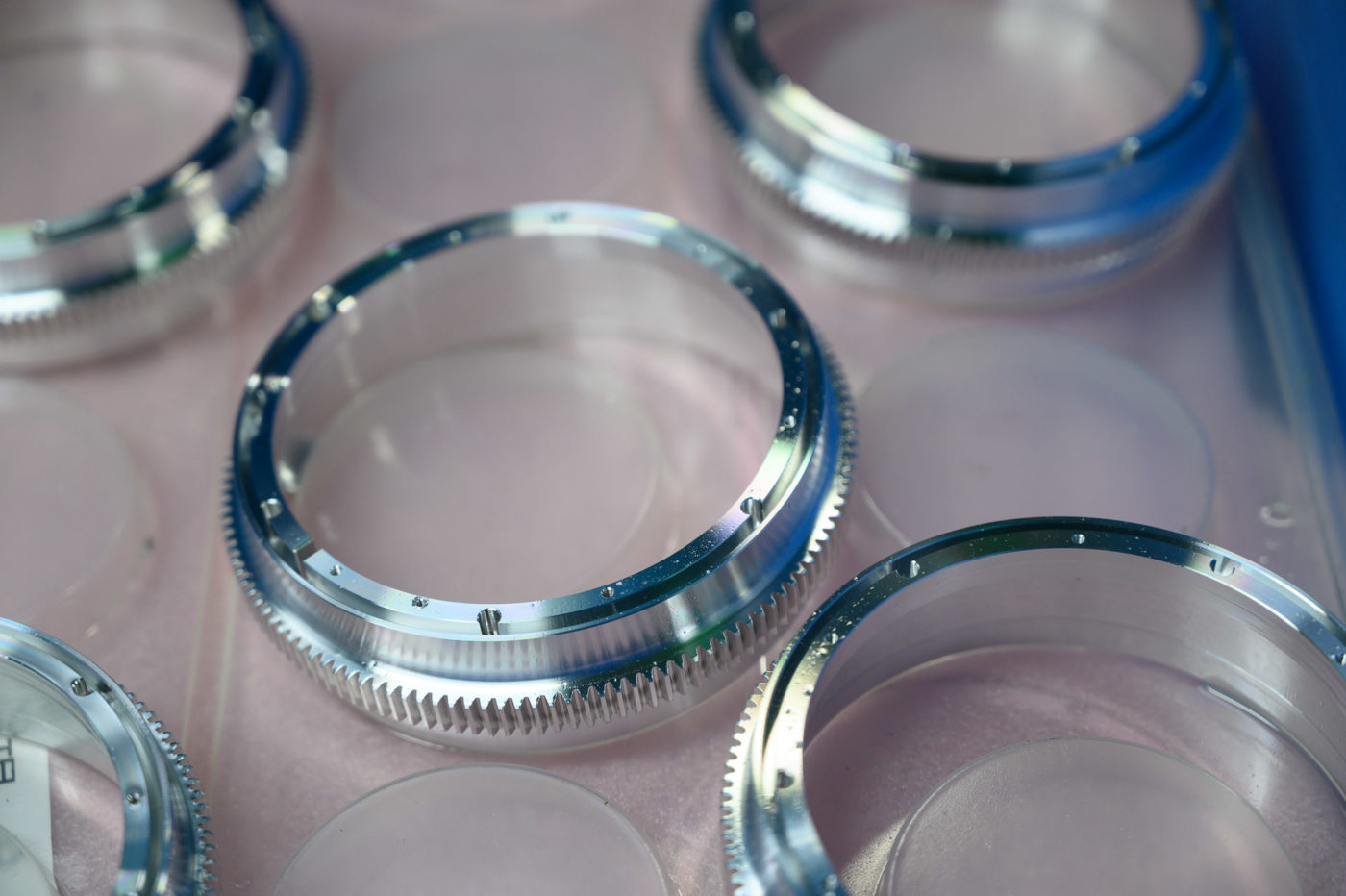
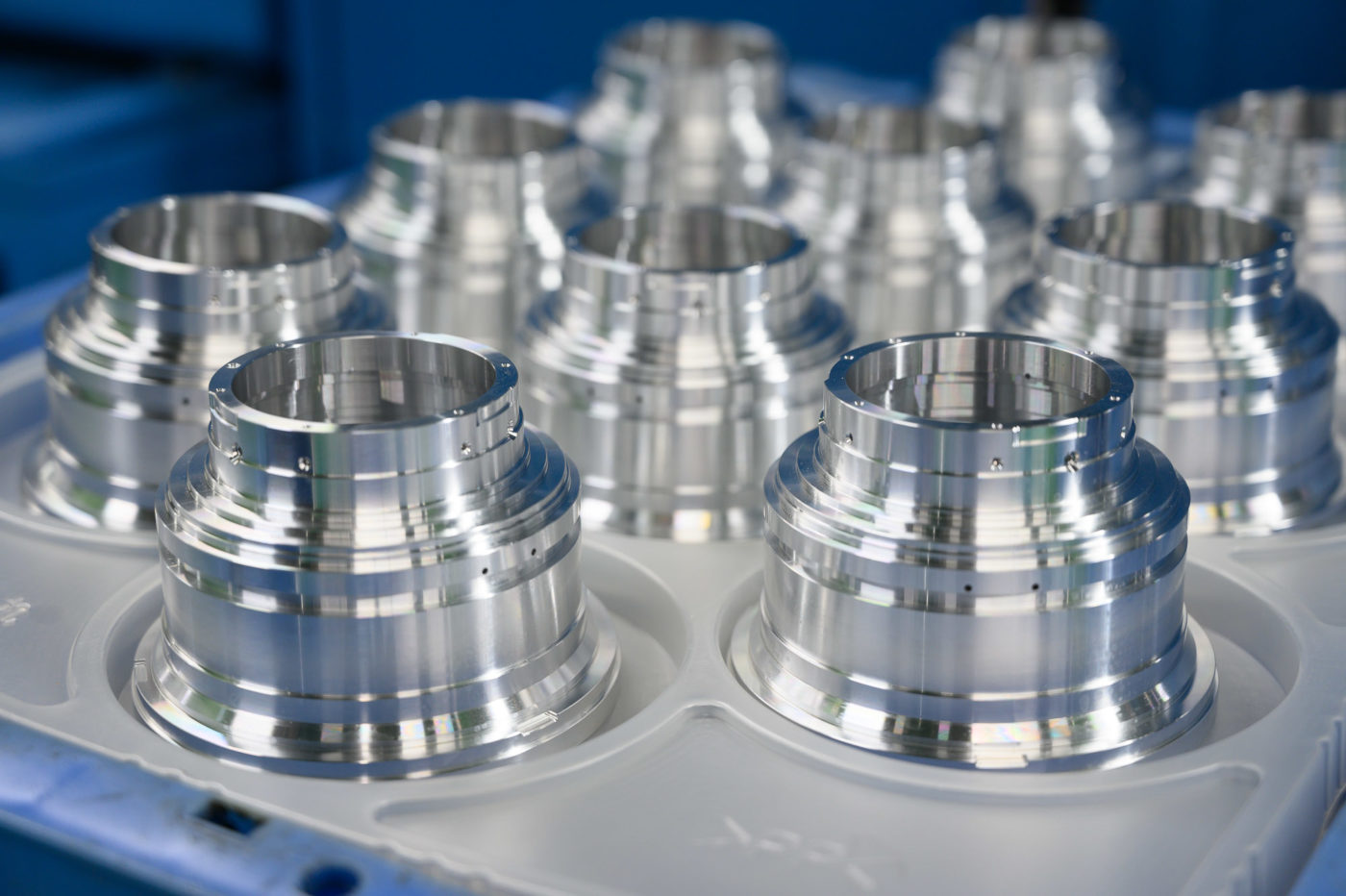
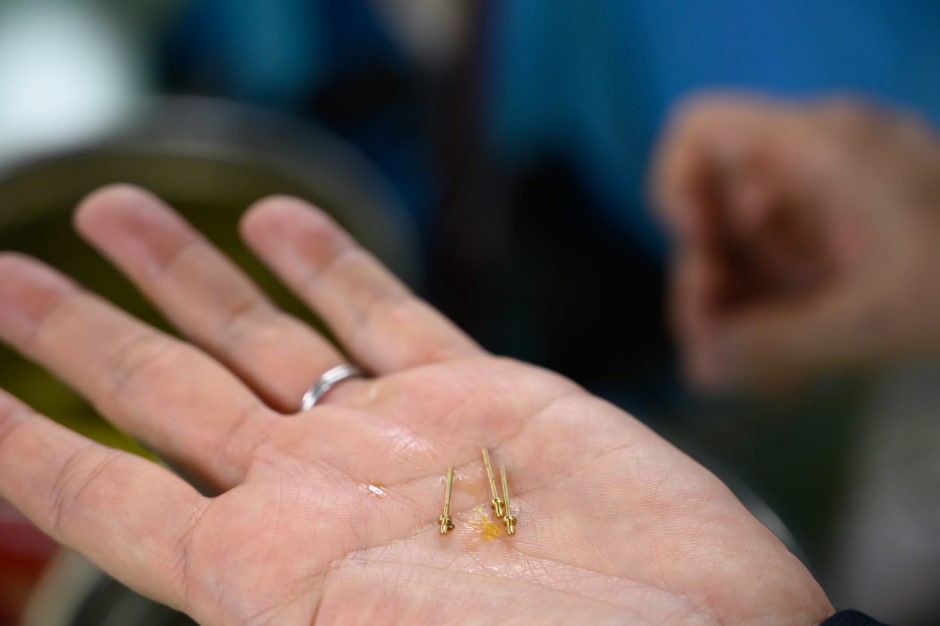
Here is an example of a robot machining a lens mount. The robot removes the part and places it into the processing machine:
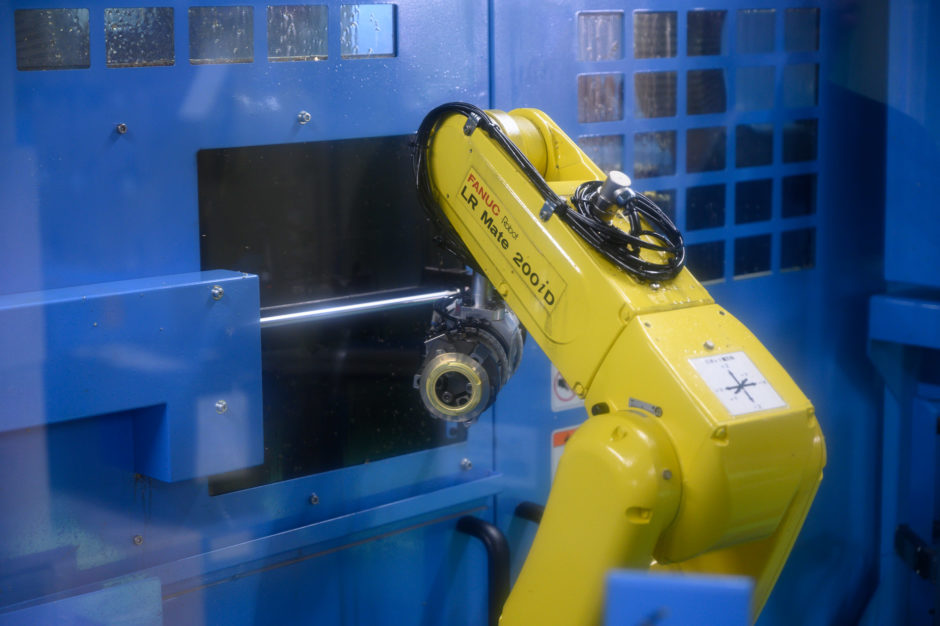
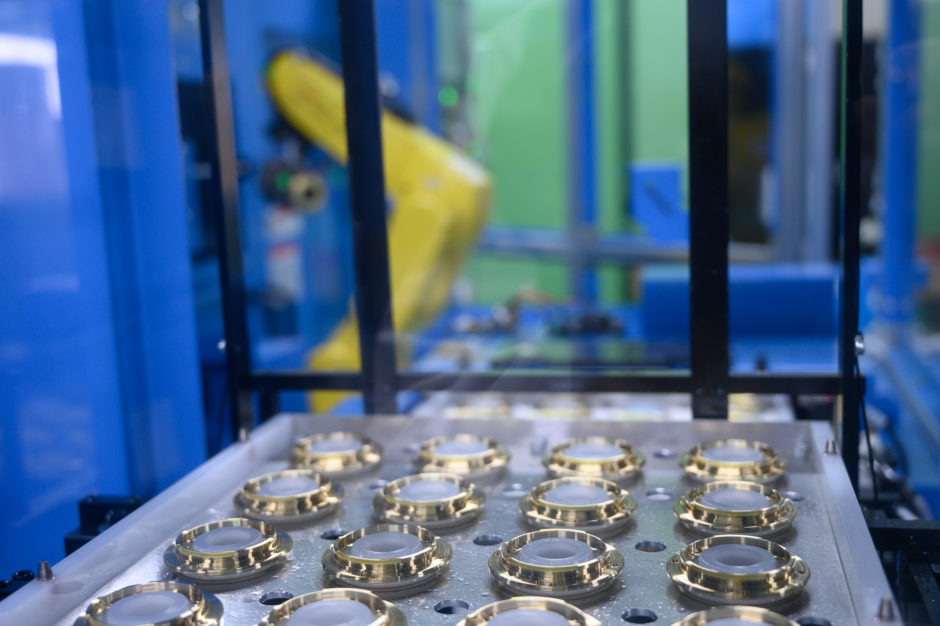
This is what a part looks like before and after machining on a CNC lathe:
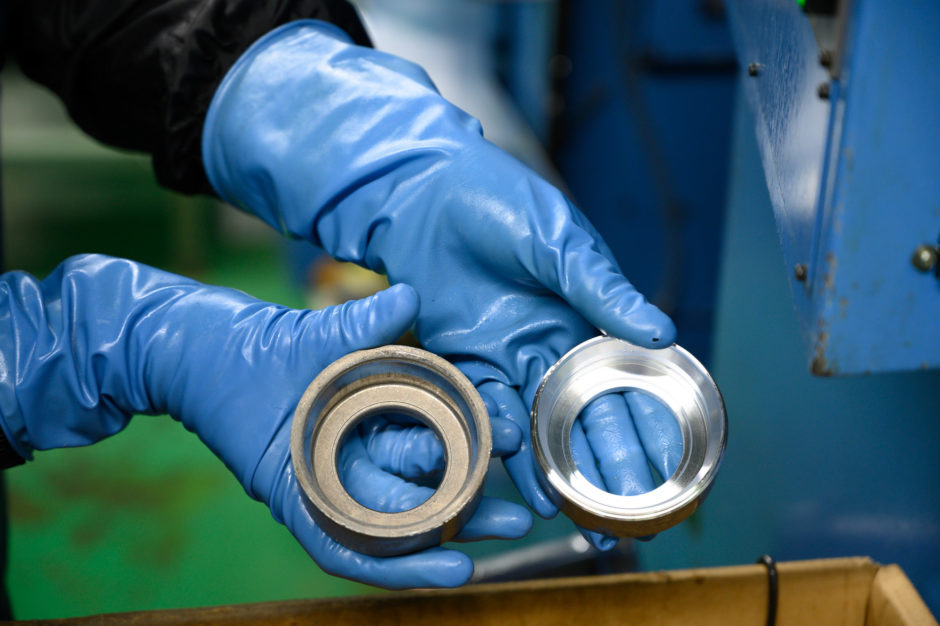
In fact, before actually seeing a fully assembled lens, many stages are required, and Sigma integrates as many production steps as possible. The waste generated from machining is, of course, collected for recycling.
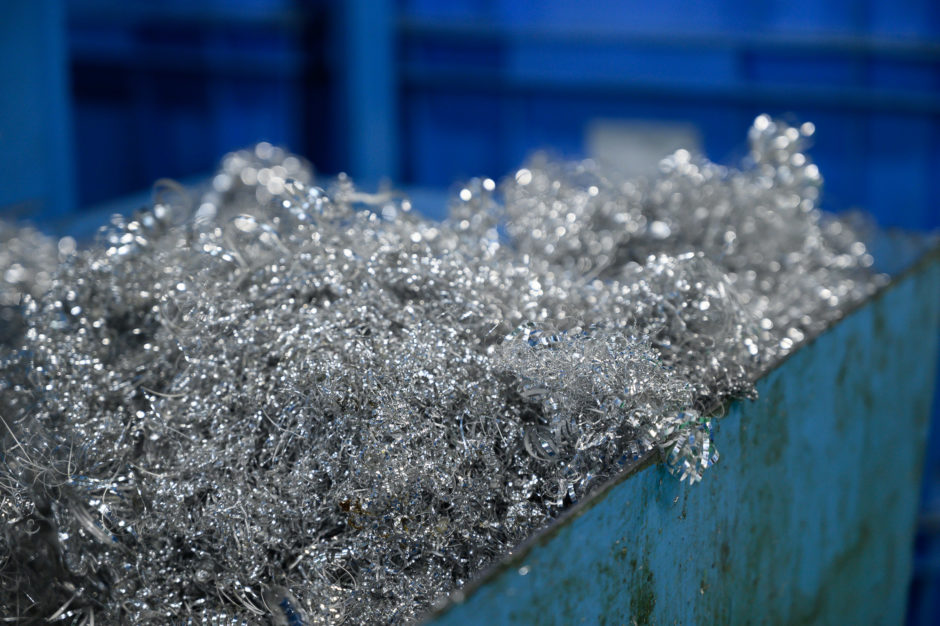
At the time of our visit, the production line was actively manufacturing the Sigma 60-600mm F4.5-6.3 DG OS HSM Sports, a telephoto lens with a barrel made of multiple materials designed to minimize size and weight, including magnesium and carbon fiber-reinforced plastic.
Here, for example, is the CAM system of the 60-600mm :
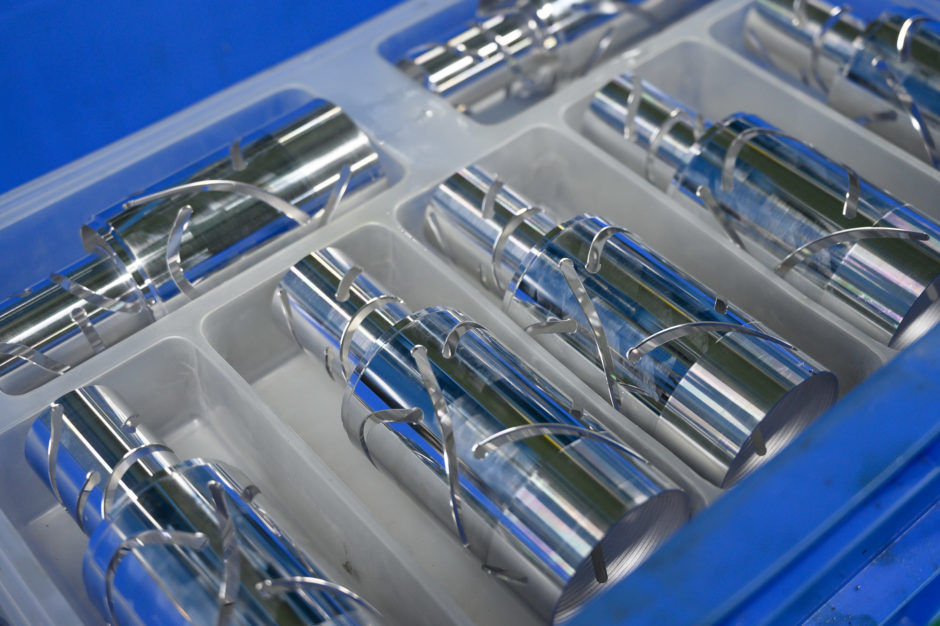
The Workshop Where Molds for Machines Are Made
Next, the tour continues as we enter the workshops where molds for machines are manufactured to create numerous plastic or metal parts. Once again, I was surprised by the number of small parts produced on-site, as well as by the high level of integration within the Aizu factory. Here, molds are crafted with remarkable precision, showcasing an artisanal spirit that is ever-present in this section of the facility.
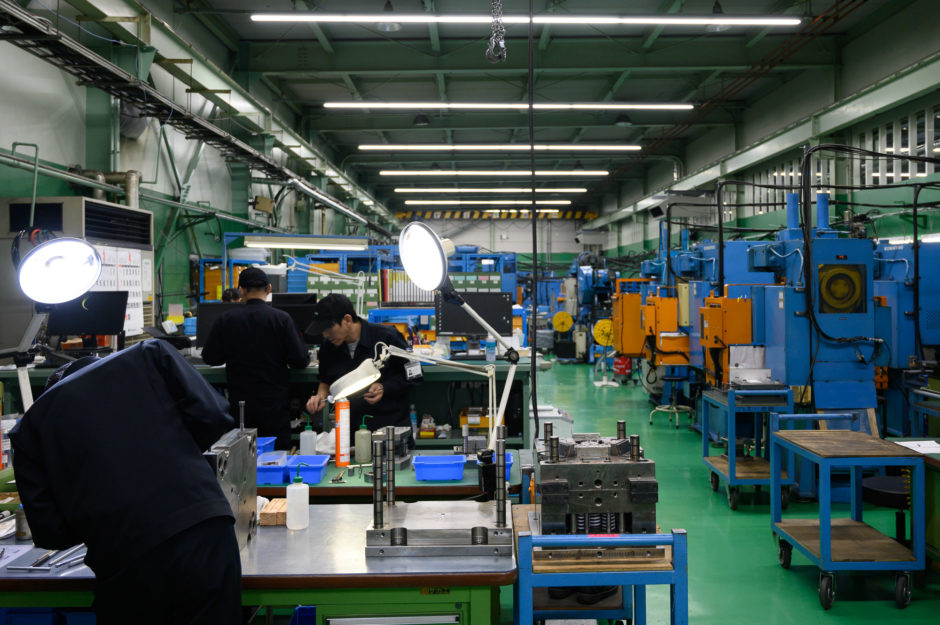
Here, we can see a metal mold undergoing Electrical Discharge Machining (EDM), a process that removes material from a metal workpiece using electrical discharges. This technique is particularly useful for machining extremely hard metals.
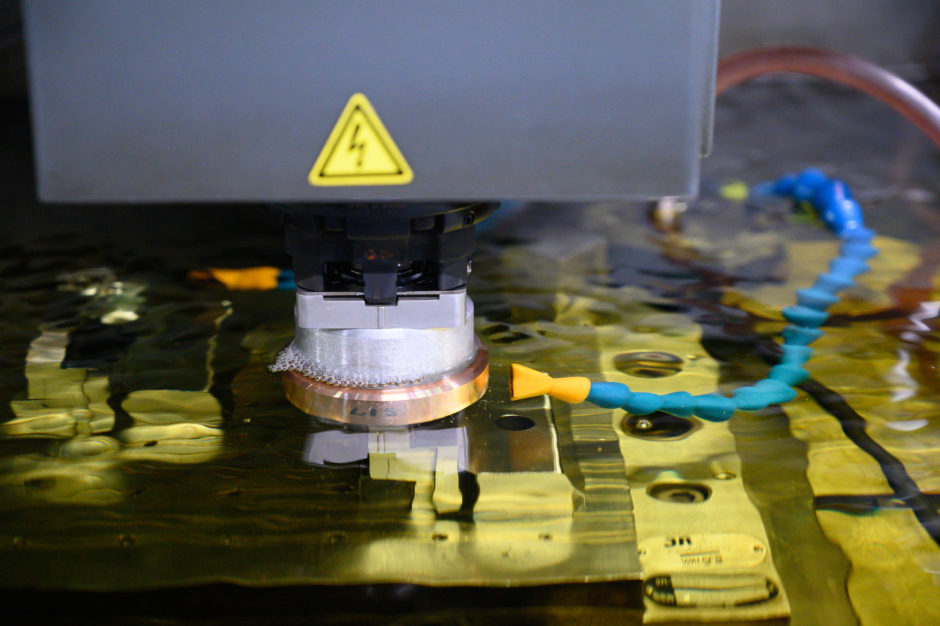
To give you an idea of how many molds are needed to produce various parts, here is a shelf where unused molds are stored. According to Sigma, more than 1,000 molds are in use.
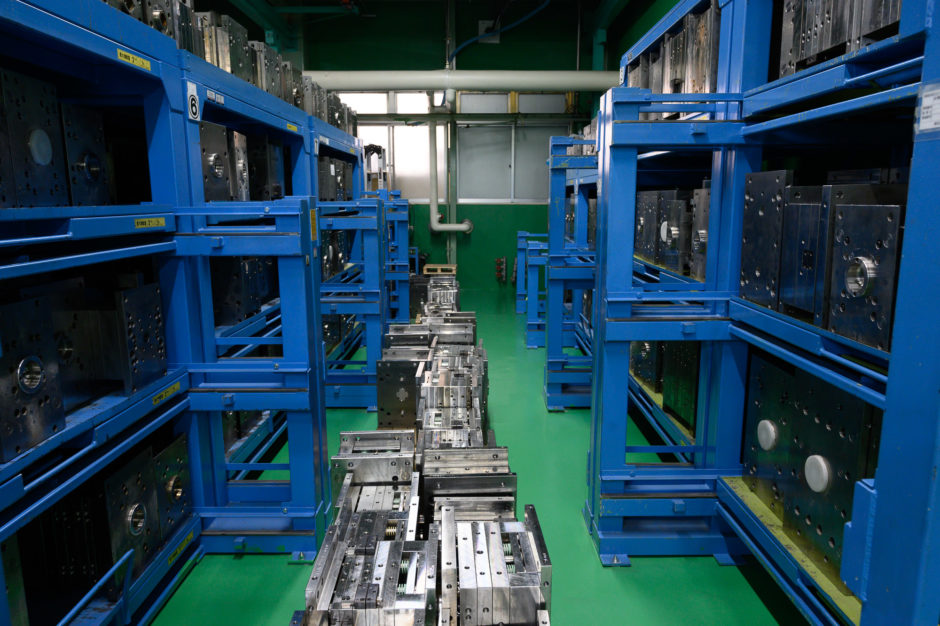
These molds allow for the manufacturing of numerous plastic and metal parts, which are also bent by the same machines. Here, for instance, is the machine that cuts diaphragm blades for lenses from an aluminum sheet.
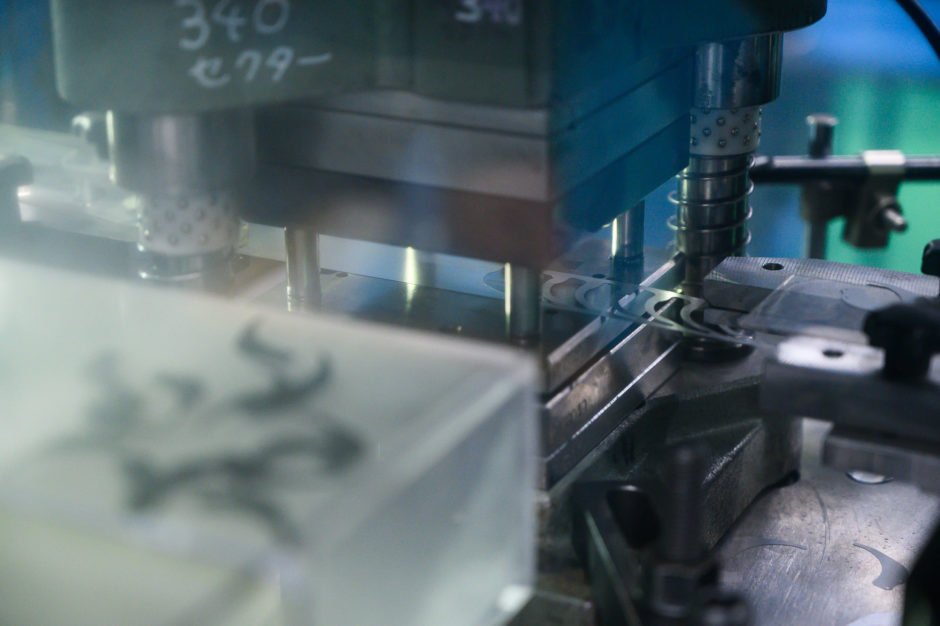
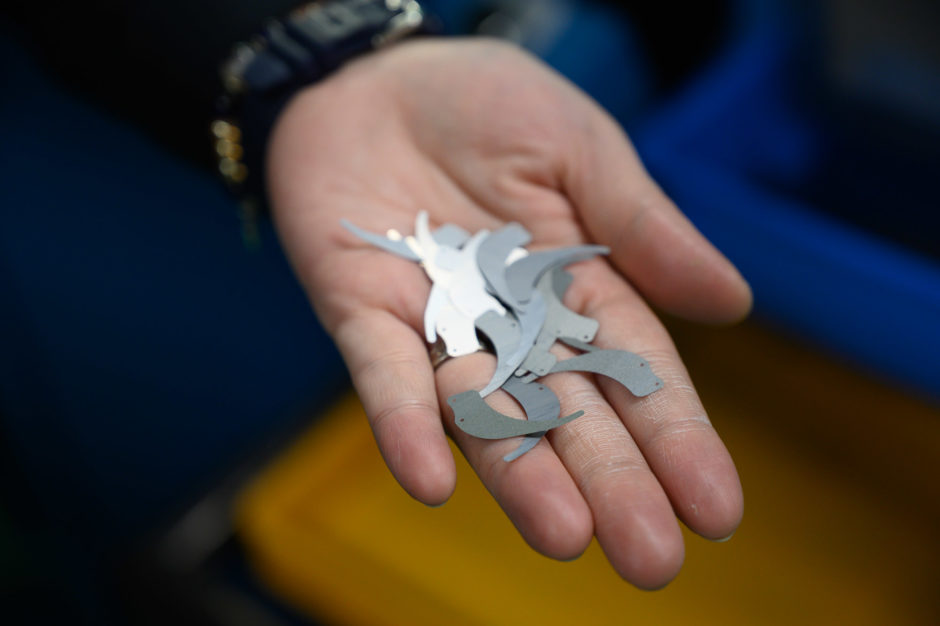
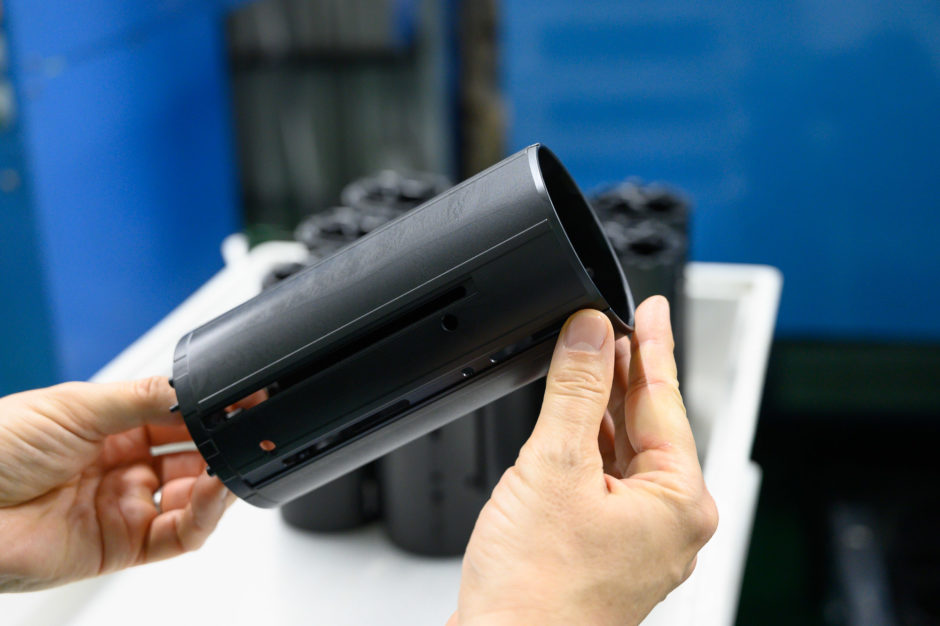
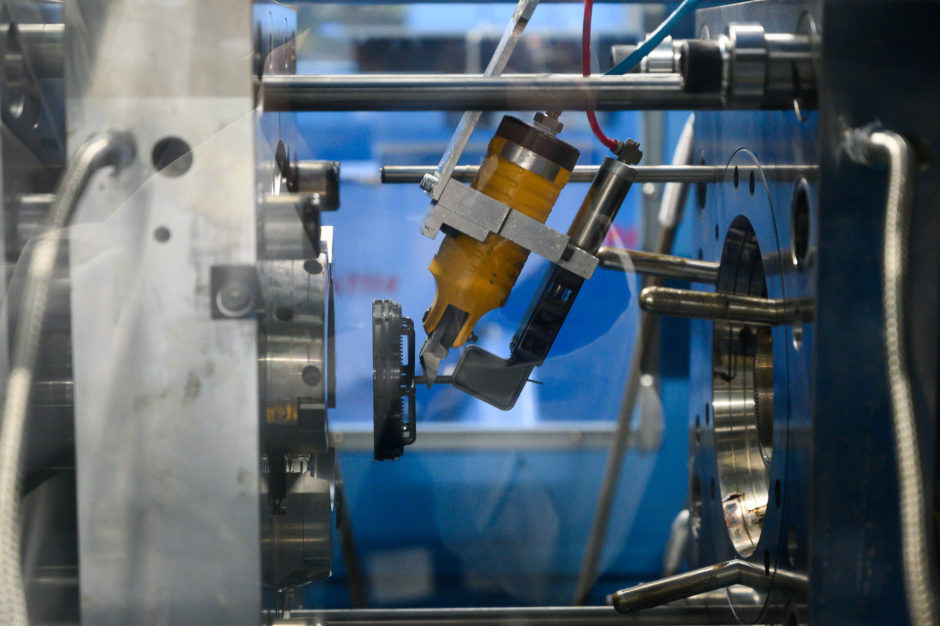
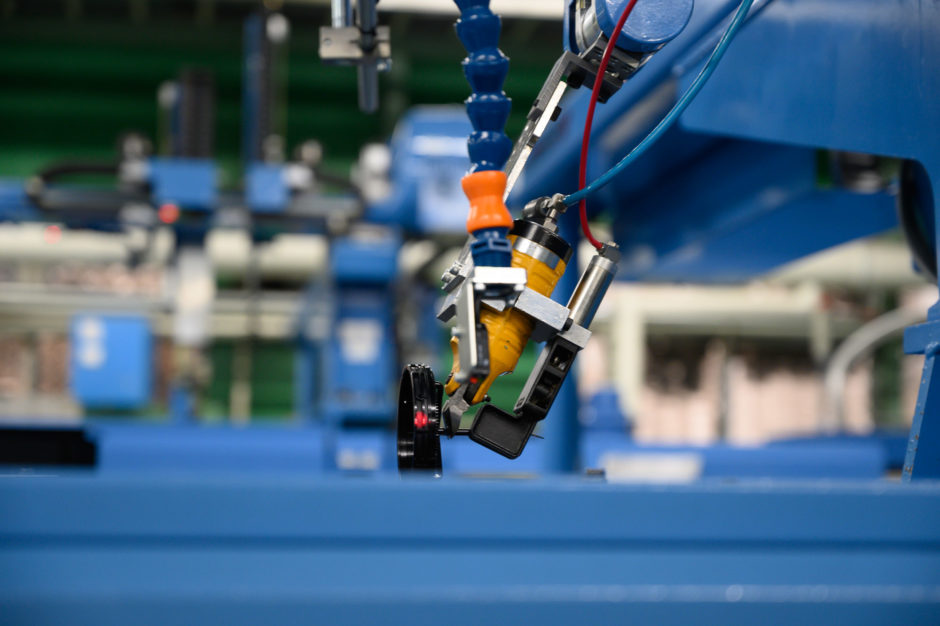
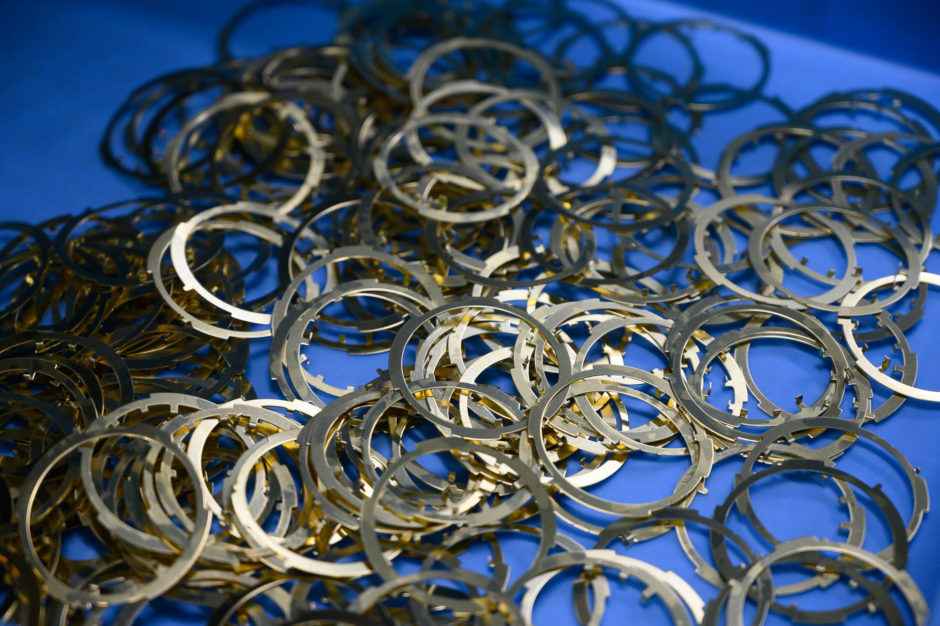
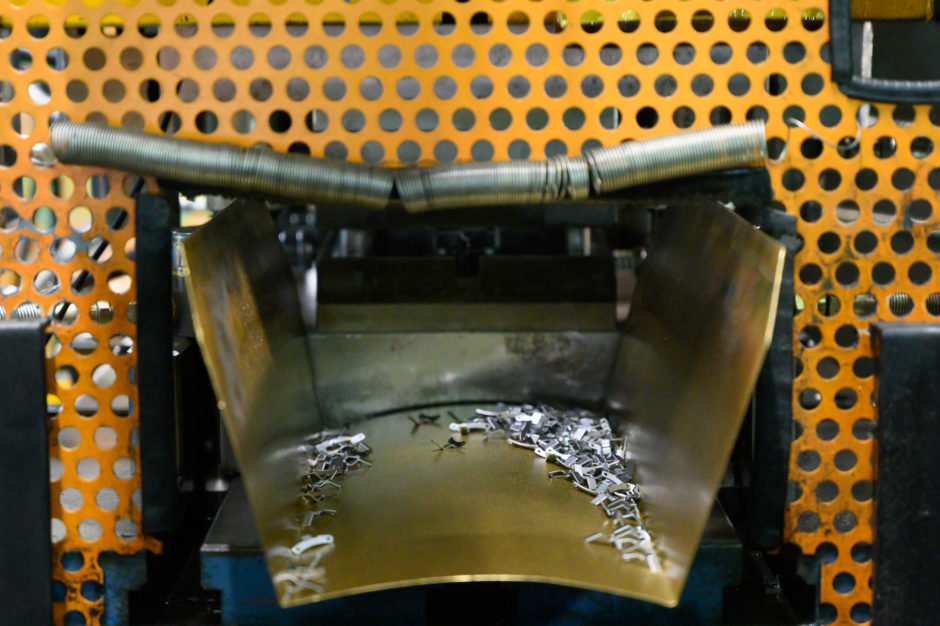
Painting Process and Manual Quality Control
Once the parts have been machined, it is time to paint them individually or in batches. Machines apply the paint to the various components, which are then manually inspected piece by piece by an operator to ensure a flawless finish. Some very precise details are painted by hand:
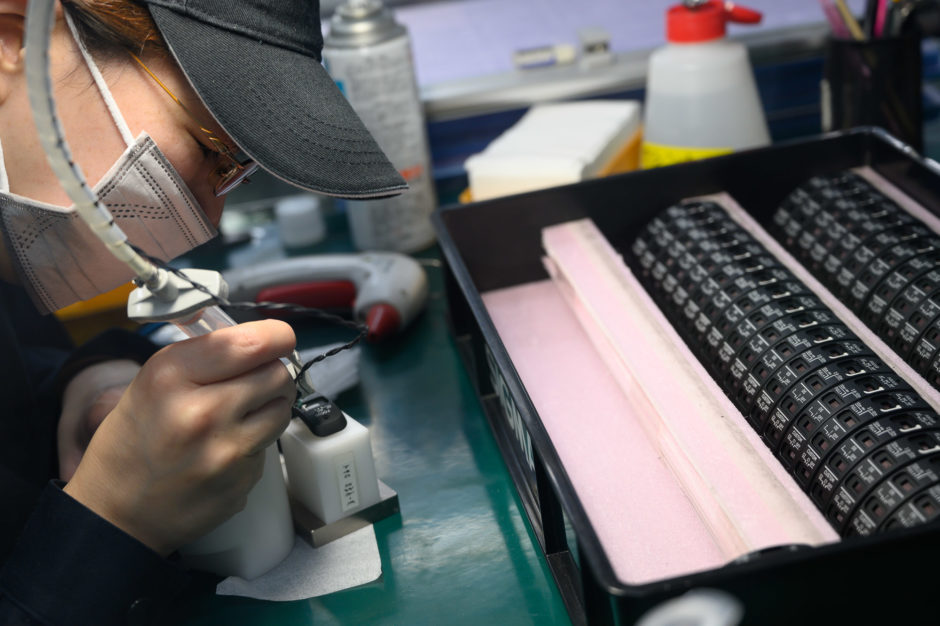
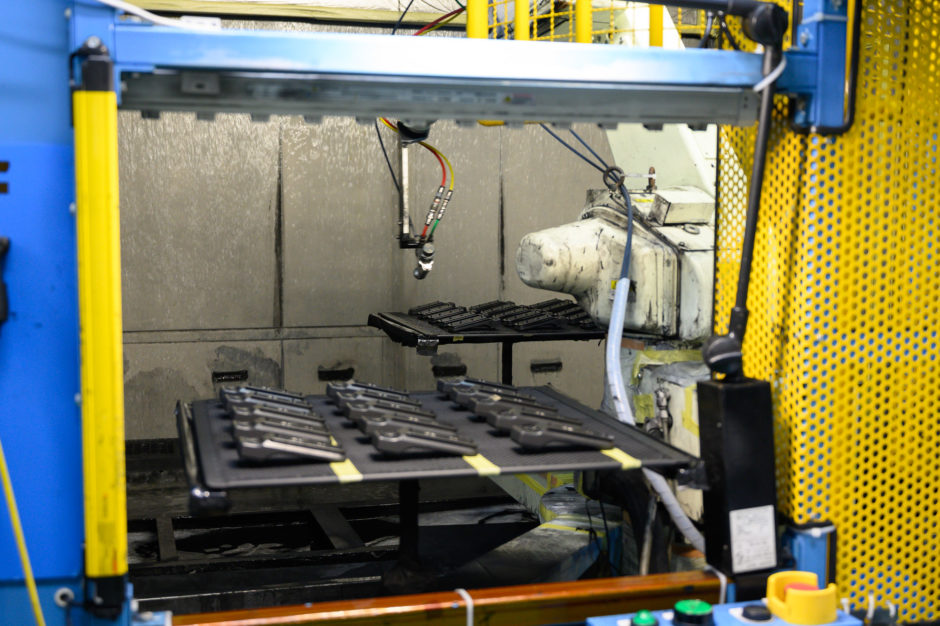
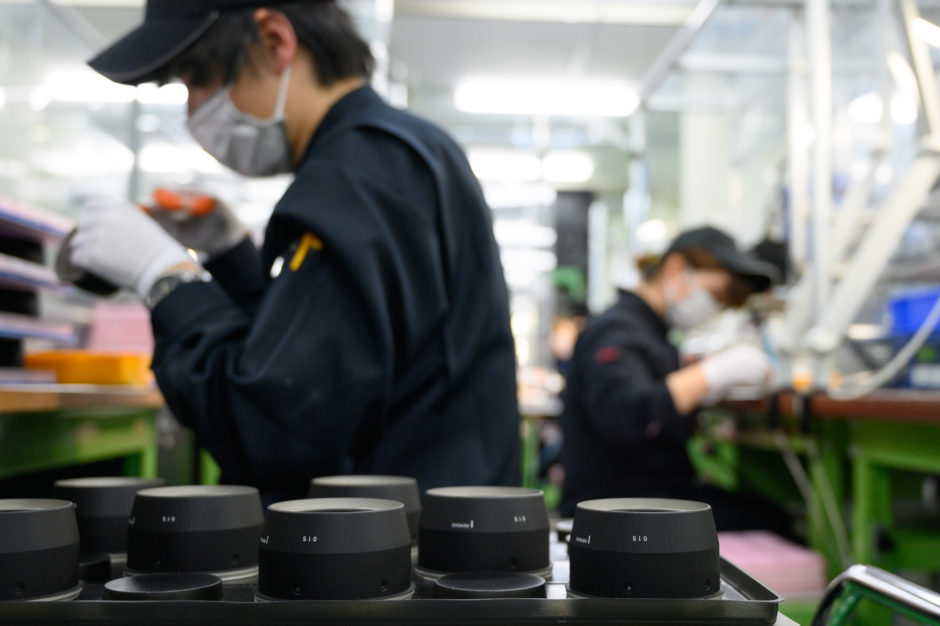
Switches are painted white, tripod collars are placed on trays to be painted by robots, and lens mounts are chrome-plated in a bath, while aluminum parts are blackened to achieve the final appearance.
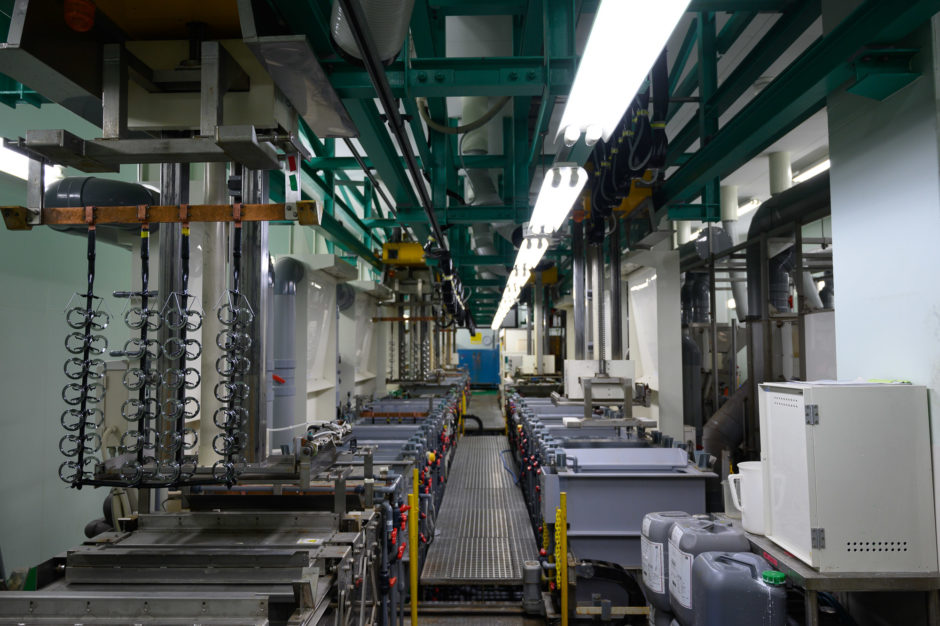
The Stages of Sigma Lens Processing
After passing through various workshops, we arrive at the optics section and the assembly area for Sigma lenses.
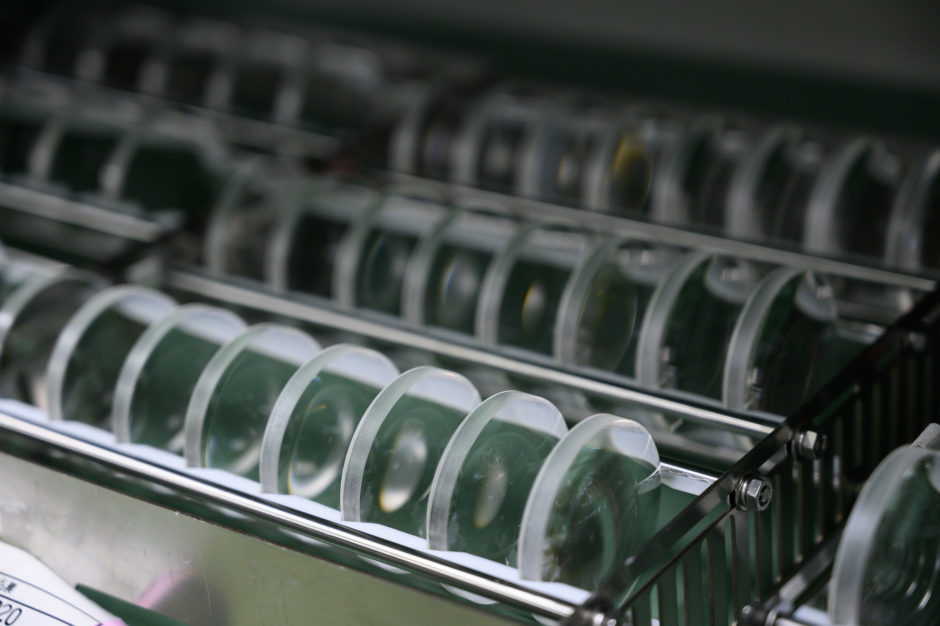
As with all lens manufacturing, each optical element undergoes a multi-step process, including polishing, centering, and coating. Although the glass received by Sigma is pre-polished, all curvatures must be refined with the highest precision.
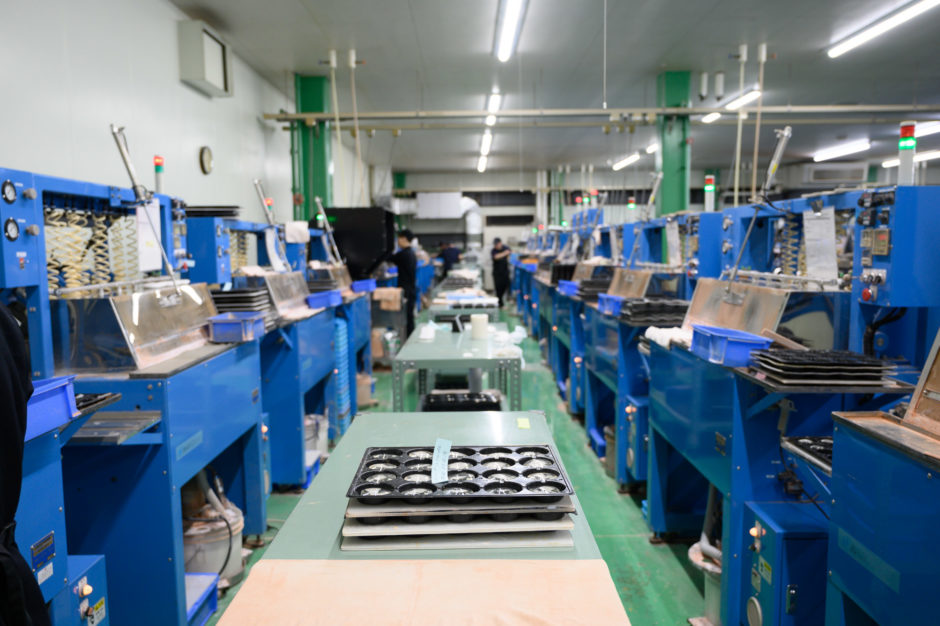
A first polishing is performed using a resin mixed with diamond powder to make the glass more transparent. Then, a second, finer polishing is carried out using machines that hold the lens with a suction cup and position it for ultra-precise finishing. Dozens of machines work on lenses of various diameters.
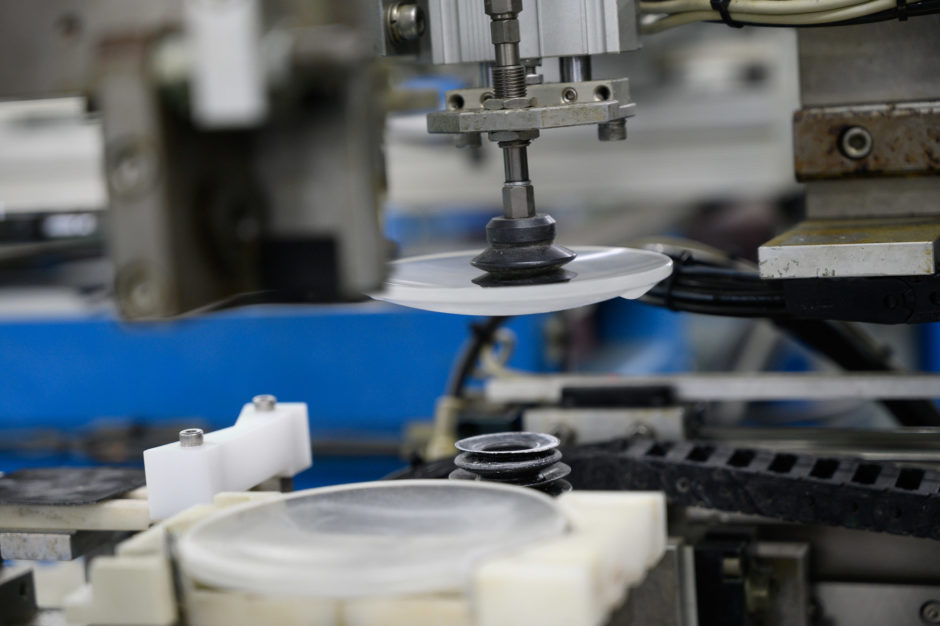
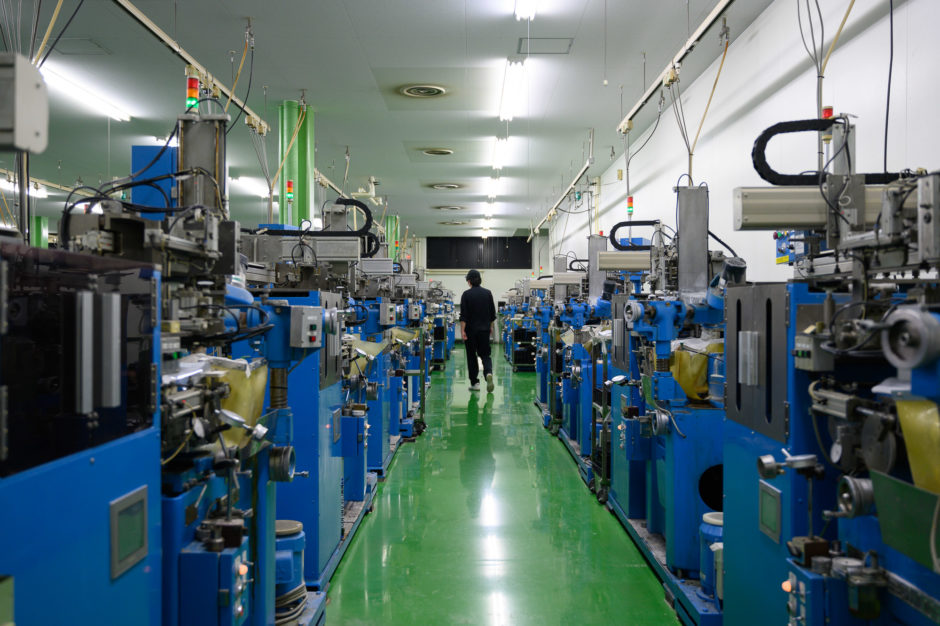
In some cases, Sigma uses a highly specialized technique to create molded aspherical lenses, which help eliminate many optical aberrations without making the optical design excessively complex. This lens is made by heating glass to 600°C and pressing it into a mold to achieve the desired shape. The process is lengthy, as the glass must be heated and then cooled, taking several hours. It is also very expensive, requiring highly specialized equipment. However, this technique allows for the creation of unique optical elements, such as the large 80mm molded aspherical lens found in the Sigma 14-24mm F2.8 DG HSM Art.
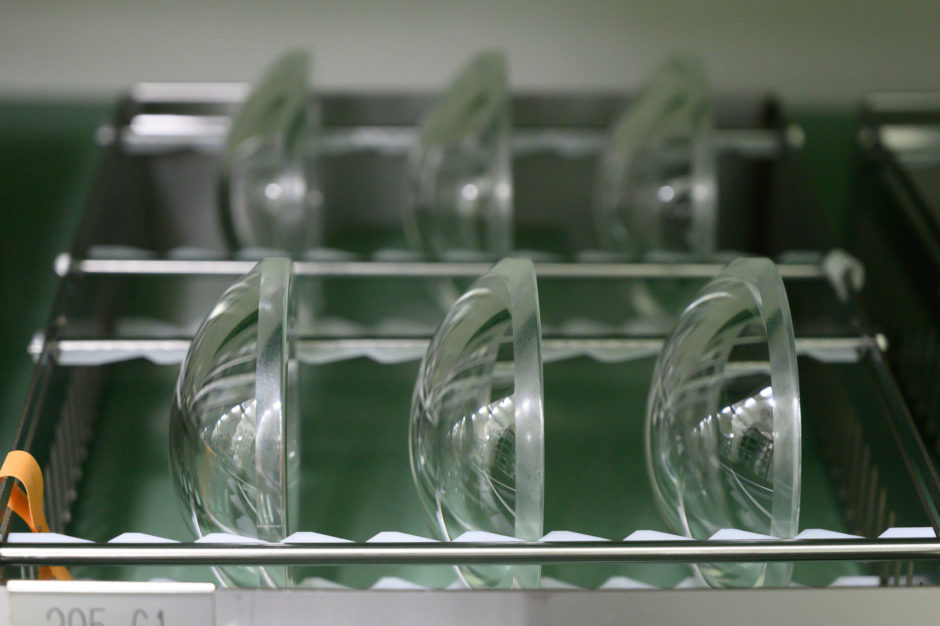
Once polished, the lenses become transparent and move on to the centering process, ensuring the optical axis is perfectly aligned for maximum performance. Next, the lenses undergo coating to reduce reflections. This coating is applied in large vacuum ovens. In these images, we see technicians handling the lenses, placing them on a dome structure before inserting them into the oven.
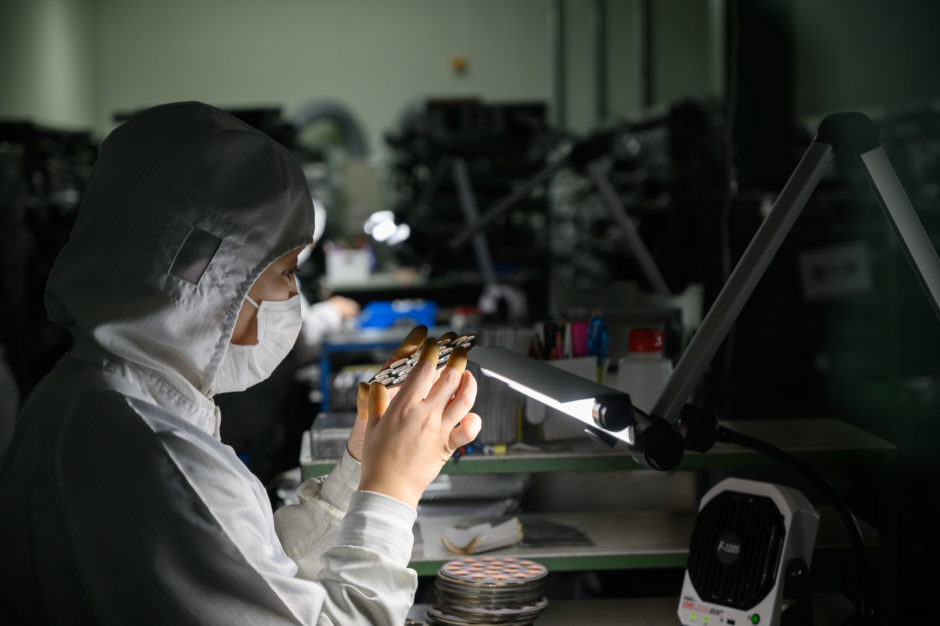
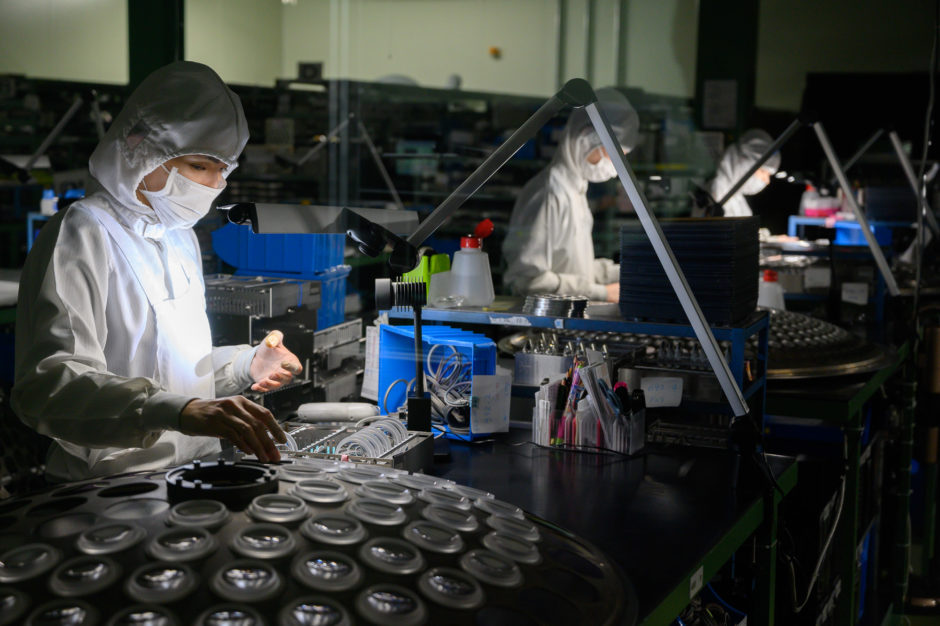
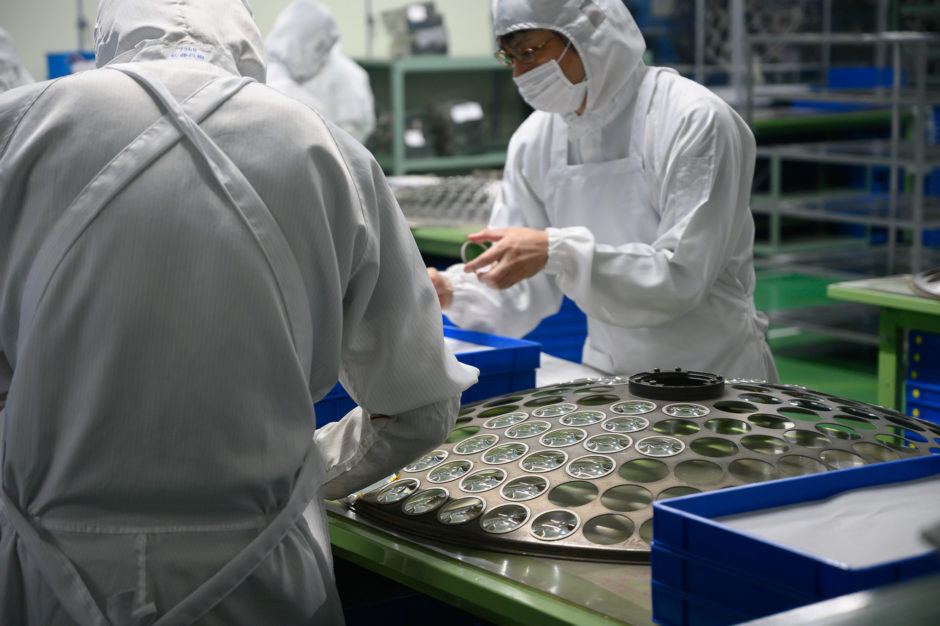
Assembly of Sigma Lenses
After these steps, it is time to assemble the different optical elements. In some cases, two lenses are bonded together to create an achromatic doublet, reducing chromatic and spherical aberrations. Quality control is performed at every stage of the assembly process, with regular measurements taken, though we were not allowed to take photos of this part of the process.
During our visit, we observed the assembly of the Sigma 60-600mm F4.5-6.3 DG OS HSM Sports lens, which was in production at the time.
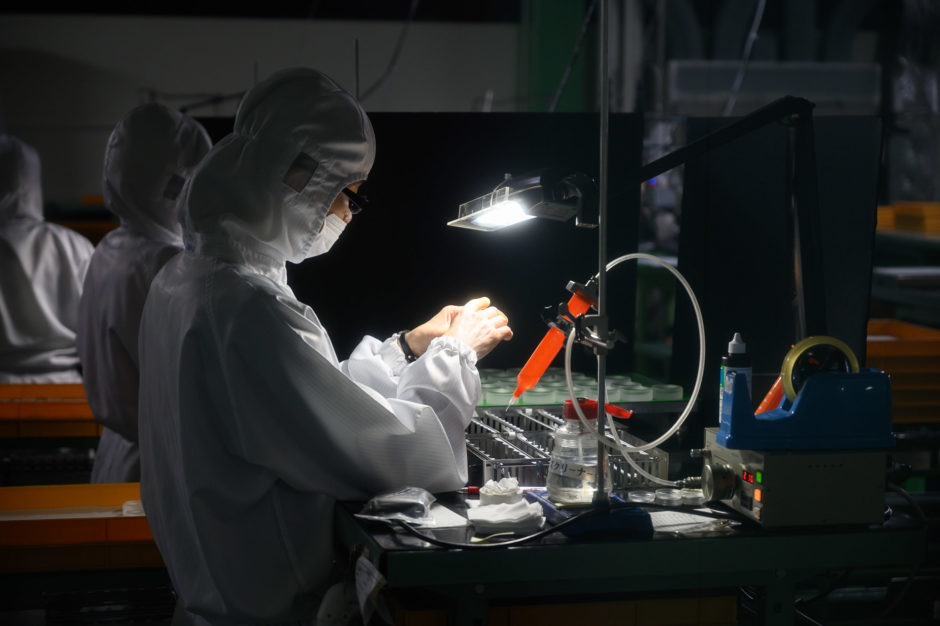
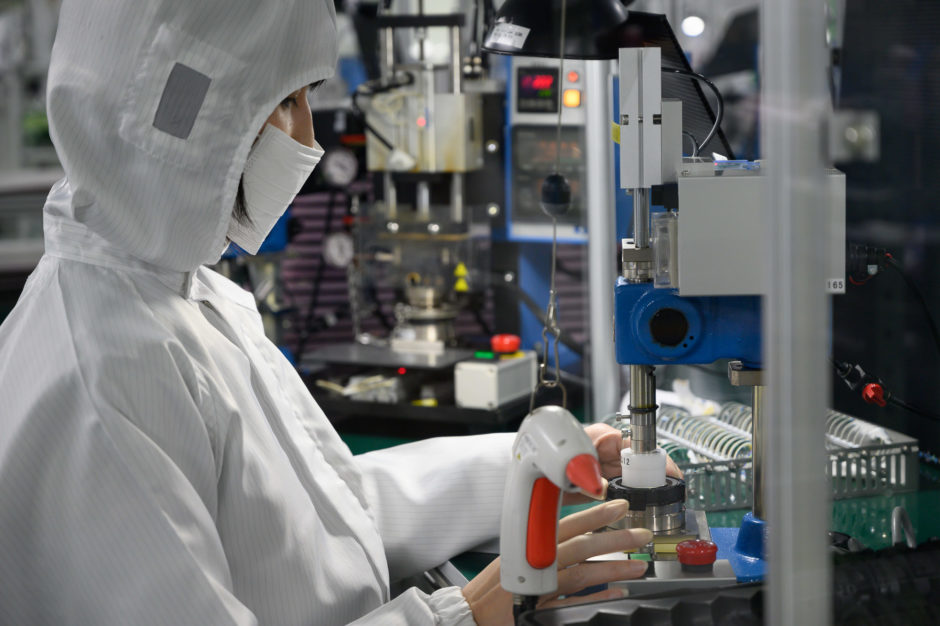
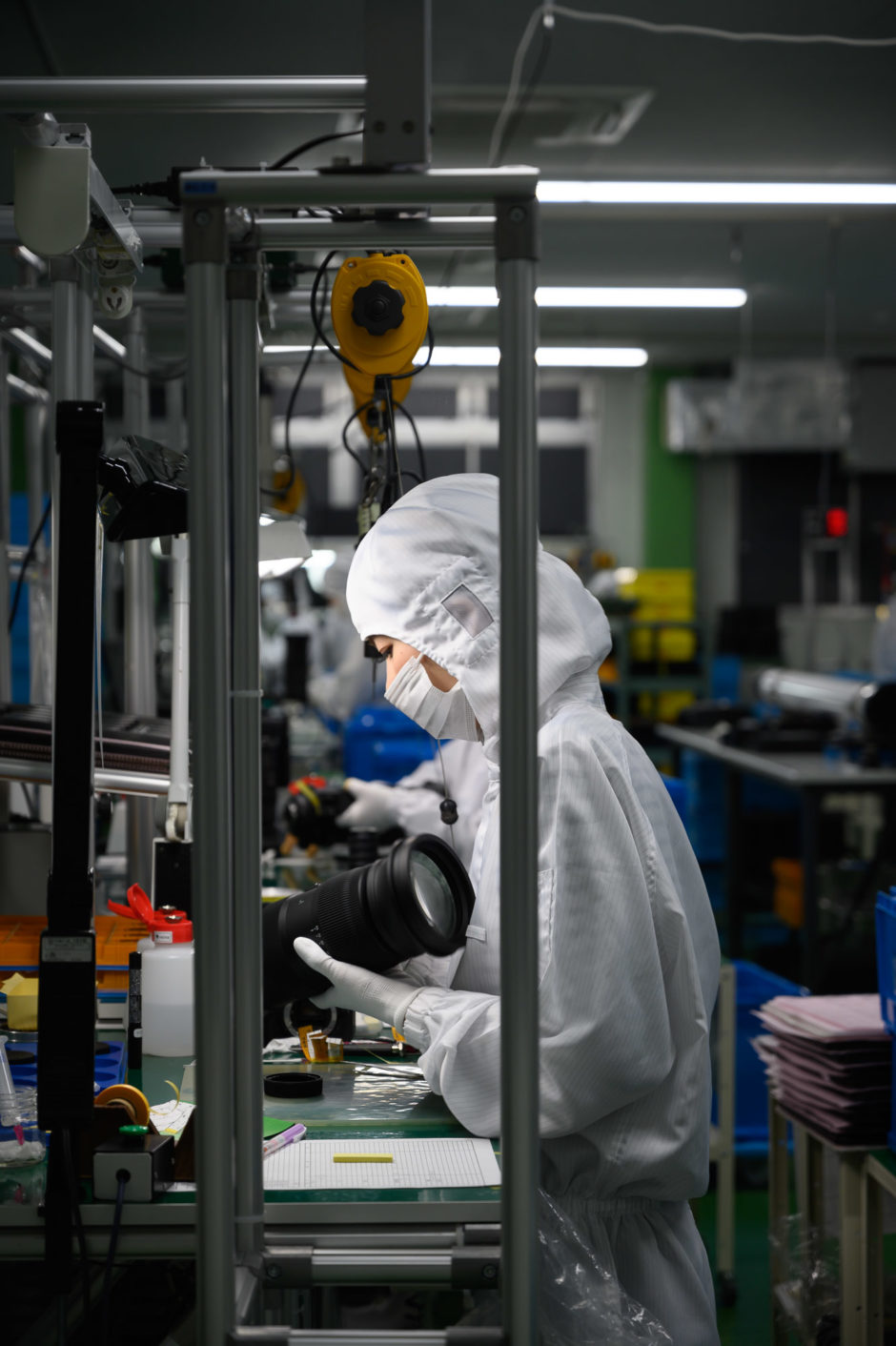
The Sigma Museum: A Journey Through the Optician’s History
Our visit concluded with a tour of the factory’s museum, where we could see historical pieces and the complete current lineup. The museum also features lens cross-sections, showing just how many elements are required to build a photographic lens. Here, for example, is the 150-600mm F5-6.3 DG OS HSM Sports, broken down into its individual components:
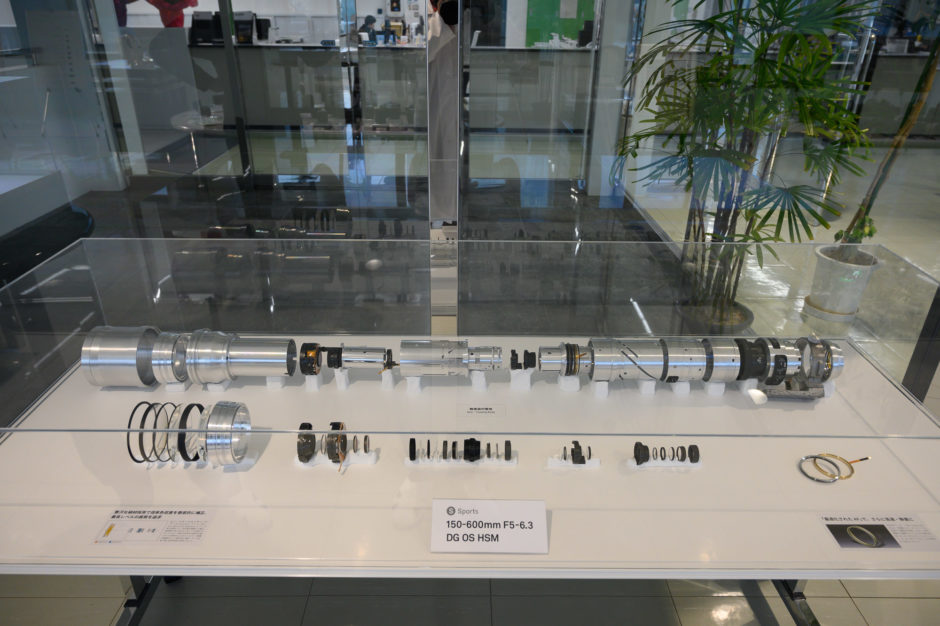
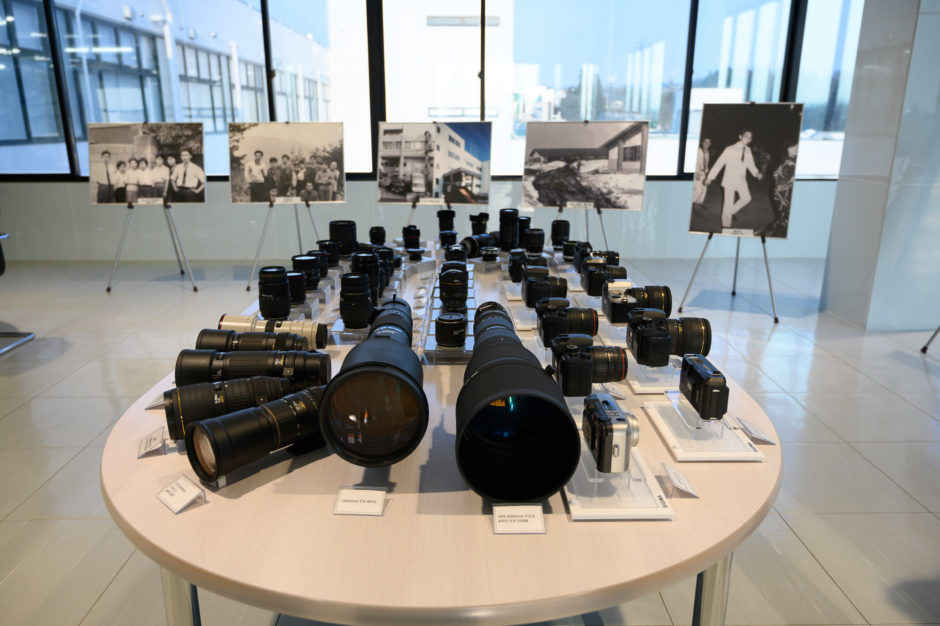
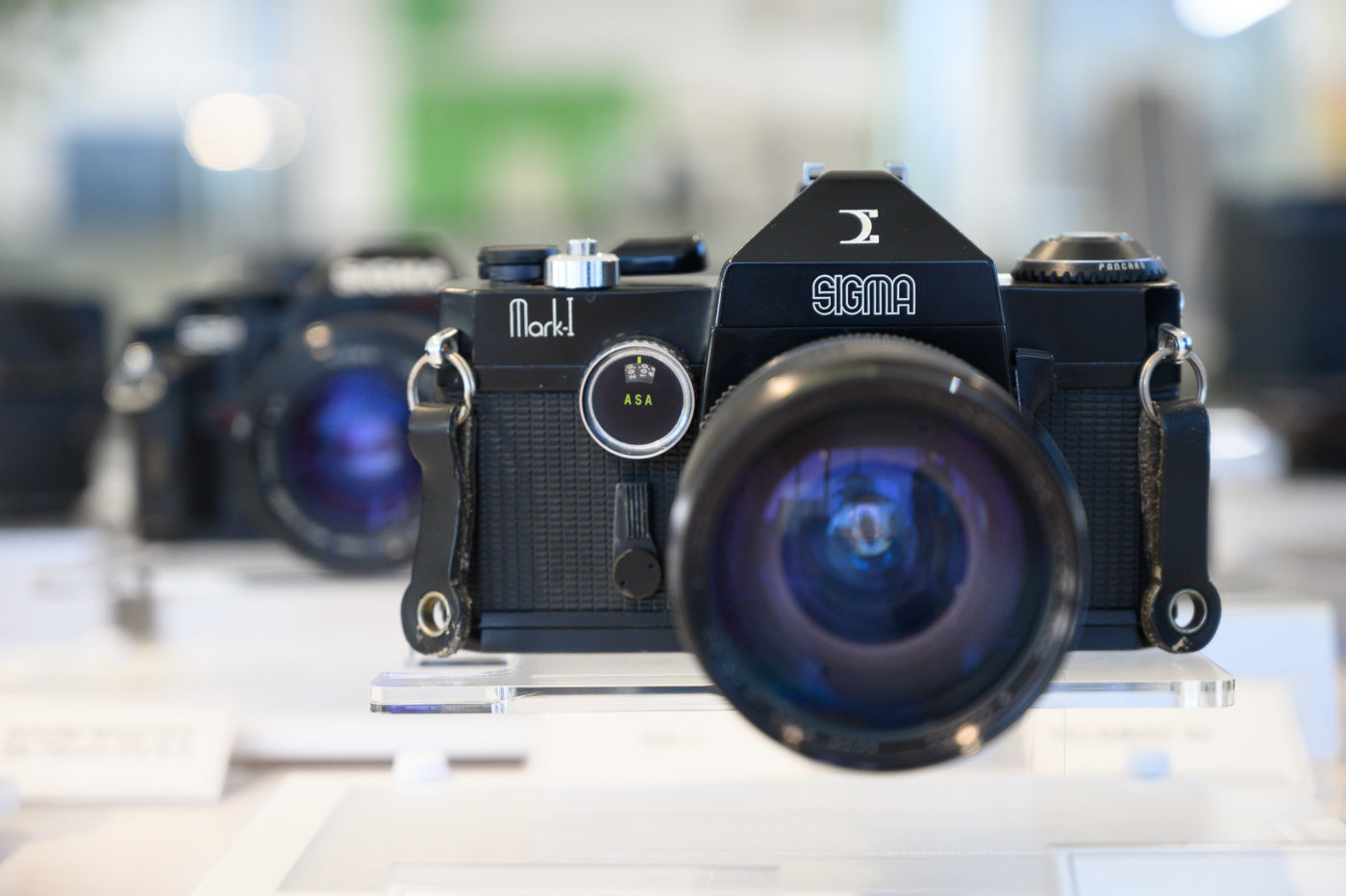
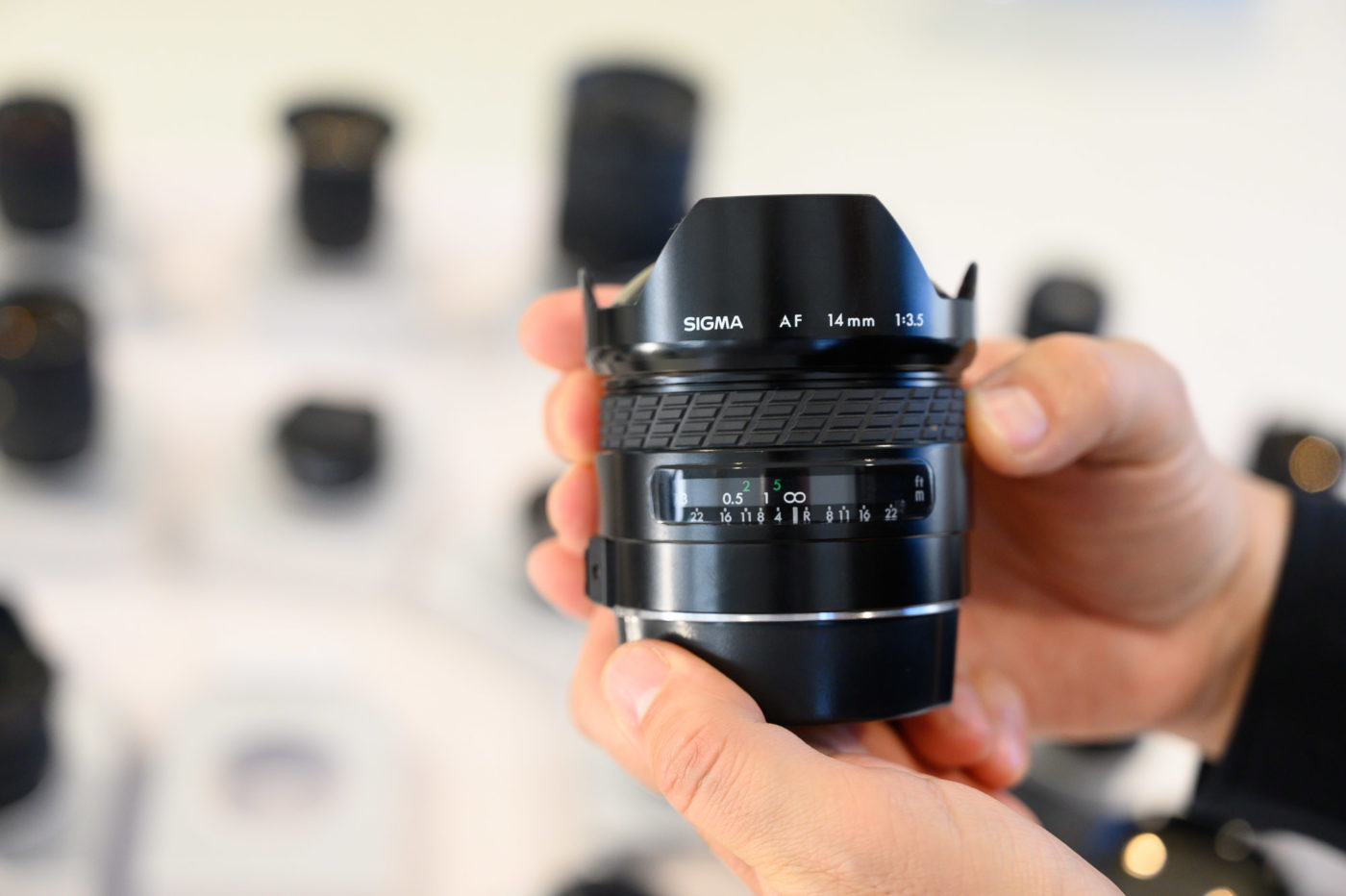
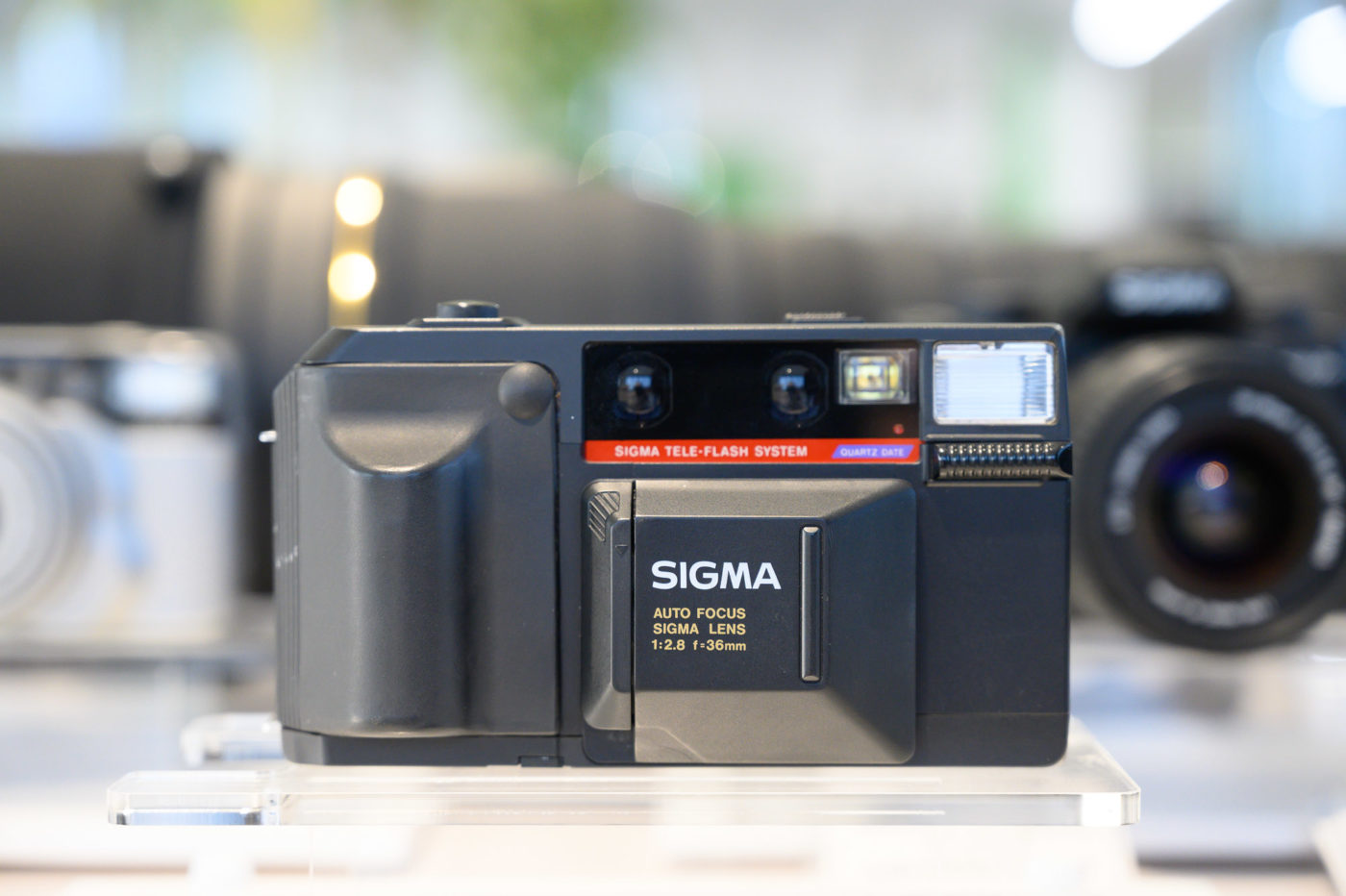
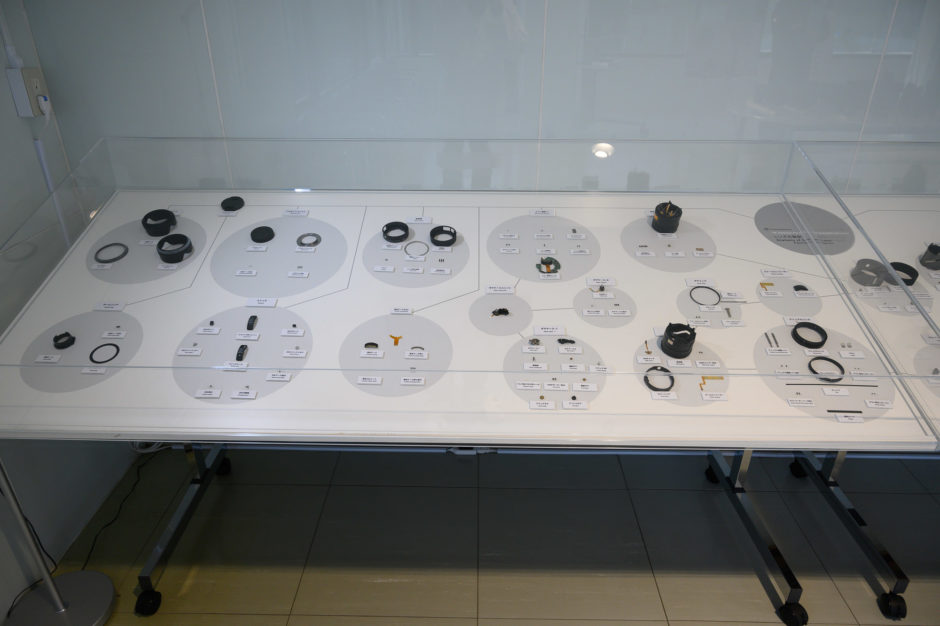
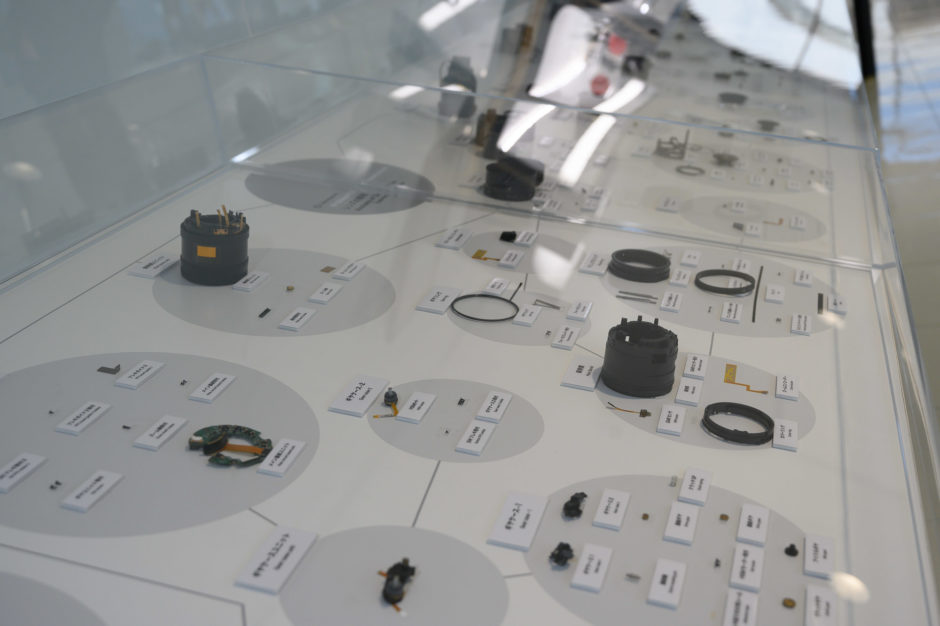
Before leaving, we took a final souvenir photo, in slippers of course, respecting Japan’s cleanliness and traditions.
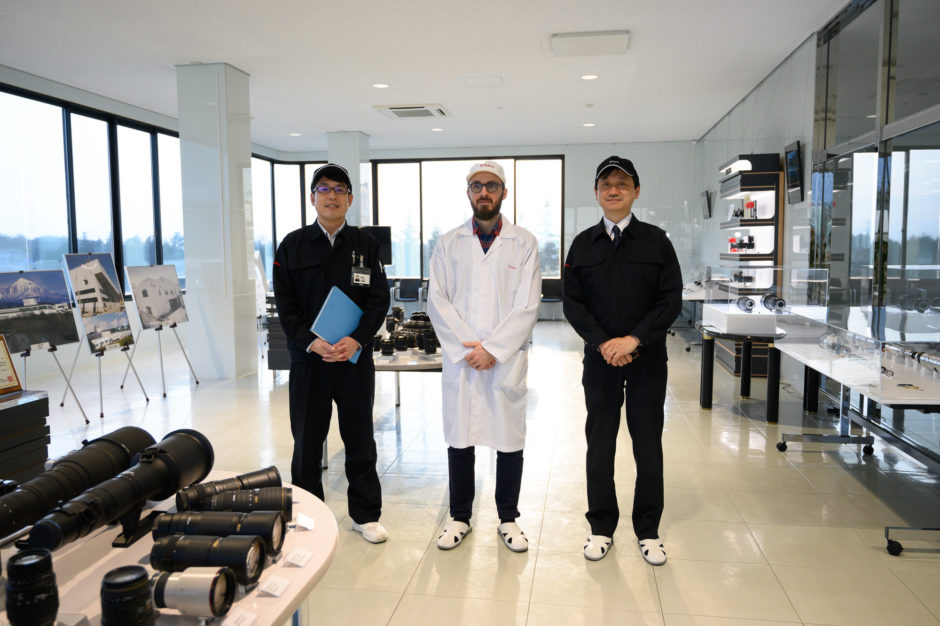
Our visit to the Sigma Aizu factory has come to an end, giving us an inside look at how Sigma lenses are made in Japan. What stood out the most was the exceptional cleanliness of the factory. Naturally, the areas dedicated to lens assembly are controlled environments where workers must wear masks and follow strict procedures. However, even in the metalworking division, the facility was remarkably clean.
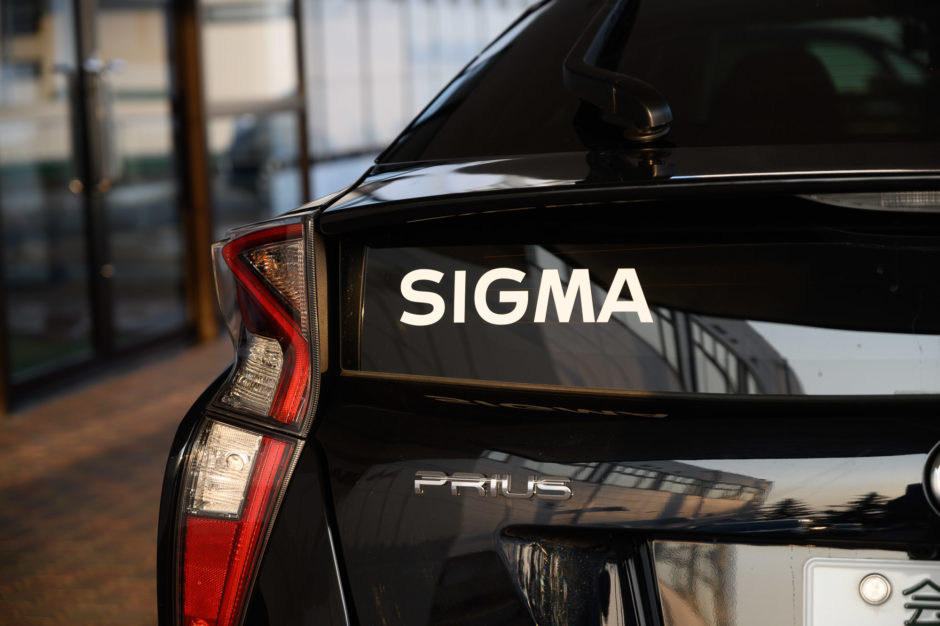
Another key takeaway from our visit was Sigma’s dedication to manufacturing every part of their lenses, not just the optical elements. By producing most of the components in-house instead of outsourcing, Sigma ensures exceptional quality and supports its local economy—a commendable approach in an era where many manufacturers relocate production to China, Vietnam, or Thailand.
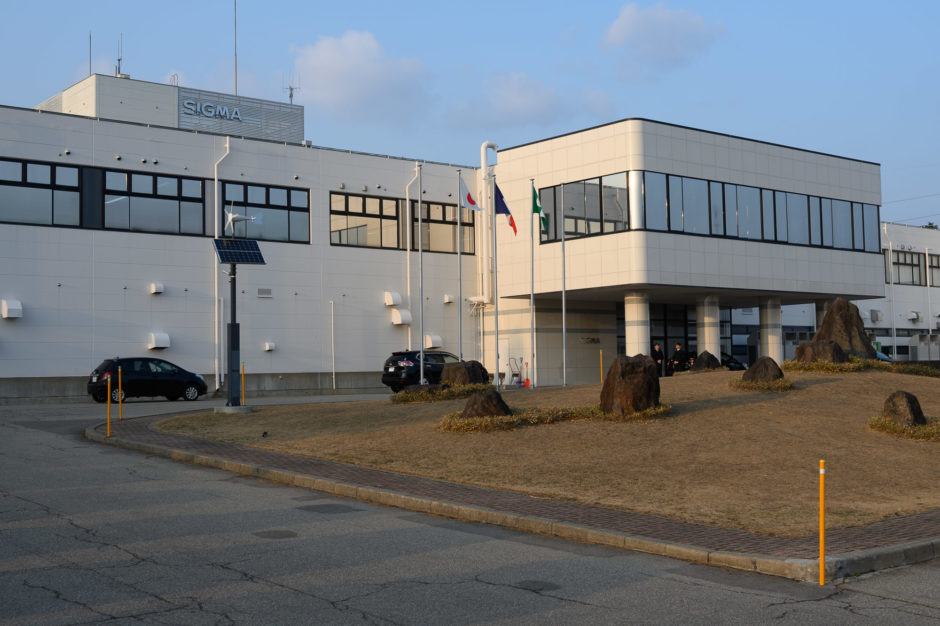
We would like to extend our thanks to the entire Sigma team for making this visit to Aizu possible, particularly Baudouin Prové and Renaud Coilliot from Sigma France, as well as Yasuhiro Ohsone and Manabu Sato from Sigma Corporation.
If you’d like to learn more, Sigma has released several videos showcasing the Aizu factory: